Resin sand casting combines the traditional method of sand casting with modern technology, resulting in superior results and enhanced manufacturing capabilities. By integrating tradition and technology, resin sand casting offers several advantages:
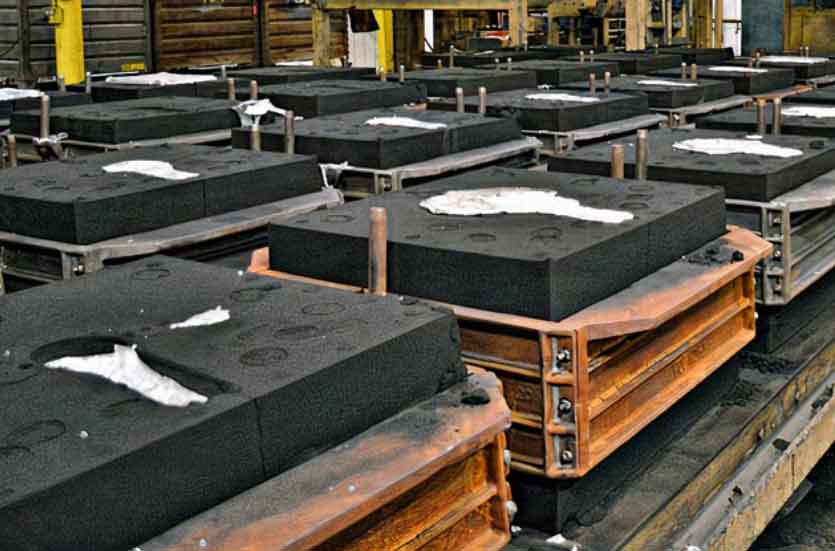
- Design Flexibility: Resin sand casting leverages the flexibility of computer-aided design (CAD) and 3D printing technologies to create intricate and complex patterns. This allows for the production of parts with unique geometries and fine details that were traditionally difficult to achieve using conventional sand casting methods. Designers can easily modify and iterate designs, enabling rapid prototyping and customization.
- Improved Dimensional Accuracy: The combination of precise 3D-printed patterns and high-quality resin-bonded sand leads to improved dimensional accuracy in resin sand casting. The fine sand particles and the controlled compaction process result in tighter tolerances and reduced casting variations. This level of accuracy is beneficial for applications that require precise fitment and alignment, such as automotive components or machinery parts.
- Enhanced Surface Finish: Resin sand casting delivers superior surface finish compared to traditional sand casting. The use of high-quality resin binders and fine-grained sand results in smoother mold surfaces, reducing the need for extensive post-casting finishing processes. The enhanced surface finish is advantageous for parts that require minimal machining or surface treatment, saving time and costs.
- Shortened Lead Times: The combination of 3D printing technology and resin sand casting enables faster production cycles and shorter lead times. The ability to directly produce patterns using 3D printers eliminates the need for pattern-making tools, reducing the setup time. This allows for quicker pattern fabrication and mold preparation, accelerating the overall casting process and enabling faster time-to-market for new products.
- Cost Efficiency: Resin sand casting offers cost advantages by combining the cost-effective nature of traditional sand casting with the design flexibility of 3D printing. The elimination of expensive tooling and the ability to produce complex patterns in-house significantly reduce upfront costs. Additionally, resin sand casting allows for batch production, making it suitable for medium to large production volumes, further enhancing cost efficiency.
- Wide Material Compatibility: Resin sand casting accommodates a wide range of metals and alloys, providing material versatility to meet diverse application requirements. It is compatible with various materials, including aluminum, iron, steel, bronze, and more. This allows manufacturers to choose the optimal material for specific performance characteristics, expanding the potential applications of resin sand casting across industries.
- Sustainability: Resin sand casting promotes sustainability by utilizing sand as the primary mold material. Sand is abundant, recyclable, and environmentally friendly compared to other mold materials. The process also minimizes material waste and energy consumption, contributing to a more sustainable manufacturing approach.
By combining traditional sand casting expertise with modern technologies, resin sand casting offers superior results in terms of design flexibility, dimensional accuracy, surface finish, and cost efficiency. This makes it a valuable manufacturing method across various industries, bridging the gap between tradition and technology to meet the evolving needs of modern production.