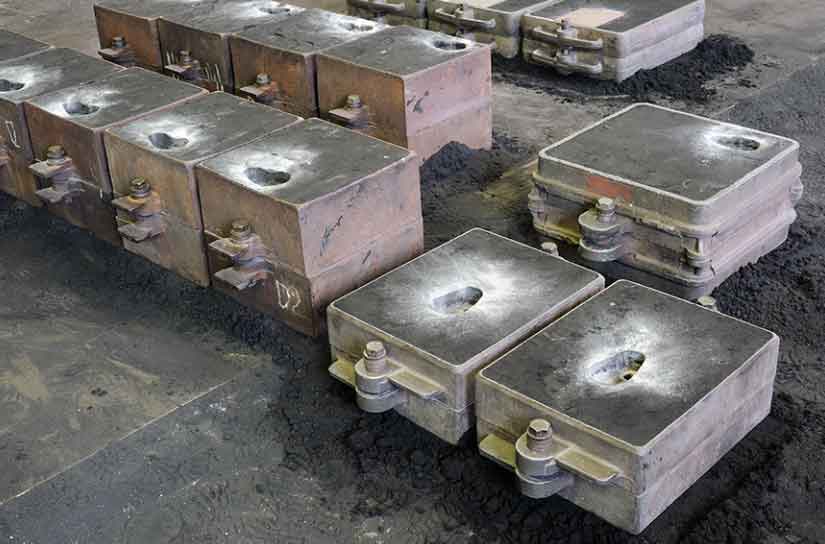
Resin sand casting is an excellent choice for prototyping and low-volume production due to its cost-efficiency and versatility. It offers several advantages that make it a preferred method for producing small batches of components or creating rapid prototypes. Here are the reasons why resin sand casting is a cost-efficient choice for prototyping and low-volume production:
1. Reduced Tooling Costs:
- Resin sand casting eliminates the need for expensive permanent molds or dies, which can be a significant cost-saving factor, especially for low-volume production or prototyping. Patterns for resin sand casting can be 3D printed or made from cost-effective materials, reducing the initial tooling investment.
2. Quick Prototyping:
- Resin sand casting allows for the rapid production of prototypes using 3D printed patterns or temporary molds. This quick turnaround time allows designers and engineers to test and validate their designs before committing to full-scale production, reducing development cycles and costs.
3. Flexibility in Design Changes:
- During prototyping and low-volume production, design changes are common. Resin sand casting offers the flexibility to modify patterns and molds easily, making it cost-effective to iterate and refine the design based on feedback and testing.
4. Material Versatility:
- Resin sand casting accommodates a wide range of materials, including various metals and alloys. This versatility allows for material selection that suits the specific performance requirements of the prototype or low-volume production run.
5. Low Production Set-Up Time:
- Compared to other casting methods, resin sand casting has relatively low production set-up time. The molds can be prepared quickly, making it suitable for cost-efficient production of small batches.
6. Minimal Waste:
- Resin sand casting generates less waste compared to other casting processes, as the sand can be reused and the patterns can be easily modified or replaced. This reduces material waste and contributes to cost savings.
7. Improved Surface Finish and Dimensional Accuracy:
- Resin sand casting offers superior surface finish and dimensional accuracy compared to traditional green sand casting. This reduces the need for post-casting finishing, saving time and costs.
8. Cost-Effective for Small Production Runs:
- Resin sand casting strikes a balance between cost-effectiveness and quality for small to medium production volumes. It is particularly advantageous for low-volume production or limited runs of custom components.
9. Lower Risk Investment:
- For prototyping, investing in resin sand casting provides a lower-risk option to test the viability and functionality of a new design or product concept before committing to more substantial investments in higher-volume production processes.
10. Environmental Benefits:
- The reduced waste and energy consumption in resin sand casting contribute to a more environmentally friendly and sustainable manufacturing process.
Resin sand casting’s cost-efficiency, quick turnaround time for prototyping, and flexibility in design changes make it an attractive choice for prototyping and low-volume production. It empowers manufacturers to produce high-quality components at a lower cost while ensuring the feasibility and performance of the final product before scaling up to higher volumes.