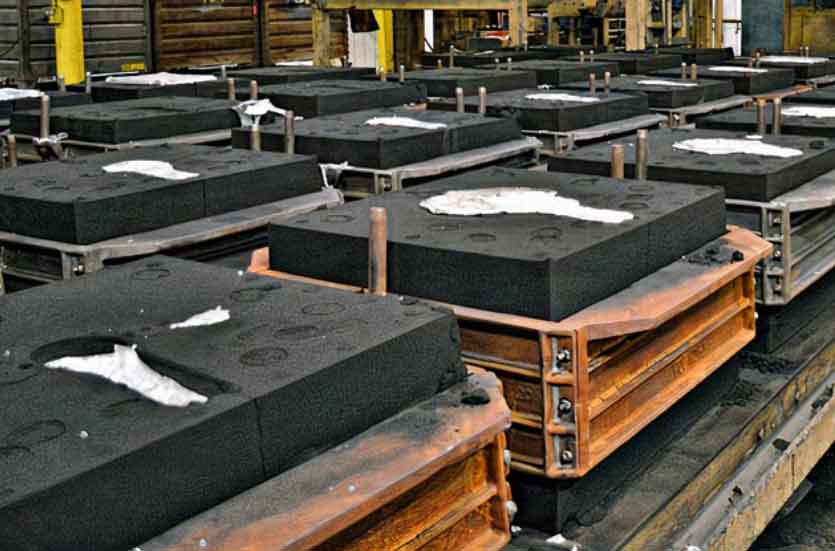
Resin sand casting offers several benefits for prototyping and low-volume production applications. It is a cost-effective and versatile casting method that allows manufacturers to quickly produce complex and customized castings without the need for expensive tooling. Here are the key benefits and considerations of using resin sand casting for prototyping and low-volume production:
Benefits of Resin Sand Casting for Prototyping and Low-Volume Production:
- Rapid Prototyping: Resin sand casting enables the quick production of patterns, allowing for rapid prototyping and iterative design improvements. Manufacturers can test multiple design iterations and make adjustments before committing to final production, reducing time-to-market.
- Design Flexibility: Resin sand casting offers design flexibility, allowing for the creation of intricate and complex geometries that may be challenging with other casting methods. This flexibility is ideal for prototyping and low-volume production of custom components.
- Cost-Effectiveness: For low-volume production runs, resin sand casting is more cost-effective than investing in expensive tooling required for other casting processes. This makes it an attractive option for small batch production or one-off custom parts.
- Customization: Resin sand casting allows for customization of castings to meet specific requirements and design changes. Manufacturers can easily modify patterns and molds for each unique casting, providing tailor-made solutions.
- Minimal Material Waste: The ability to create 3D-printed patterns directly reduces material waste, making resin sand casting an eco-friendly option for low-volume production.
- Shorter Lead Times: Compared to conventional production methods, resin sand casting offers shorter lead times for casting production, making it suitable for time-sensitive projects.
- Reduced Machining: Resin sand casting can produce near-net shape castings with less machining required, further reducing production time and costs.
Considerations for Resin Sand Casting in Prototyping and Low-Volume Production:
- Limited Production Quantity: While resin sand casting is cost-effective for low-volume production, it may not be the most efficient option for high-volume manufacturing. For large quantities, other casting methods like die casting or investment casting might be more suitable.
- Surface Finish: The surface finish of castings in resin sand casting might not be as smooth as other casting methods, which may require additional post-casting finishing processes.
- Pattern Wear: Repeated use of 3D-printed patterns can lead to wear and reduced pattern accuracy over time. Regular inspection and maintenance of patterns are essential for consistent casting quality.
- Pattern Complexity: Highly complex patterns may require longer production times and could increase the cost of prototyping and low-volume production.
- Dimensional Tolerance: Although resin sand casting can achieve good dimensional accuracy, it may not be as precise as certain precision casting methods like investment casting.
- Tooling and Equipment: While resin sand casting requires less expensive tooling compared to other methods, initial tooling costs and the need for specialized equipment should be considered for prototyping and low-volume production.
Resin sand casting offers significant benefits for prototyping and low-volume production, including rapid prototyping, design flexibility, cost-effectiveness, and customization. However, manufacturers should also consider the specific requirements of their projects, including production quantity, surface finish expectations, and pattern complexity, to determine if resin sand casting is the best fit for their needs. When appropriately applied, resin sand casting can be a valuable solution for producing high-quality prototypes and low-volume custom castings efficiently and economically.