Resin sand casting is a valuable process for prototyping in the manufacturing industry. It offers several advantages that make it suitable for rapid iterations and design validation. Here’s how resin sand casting facilitates the prototyping process:
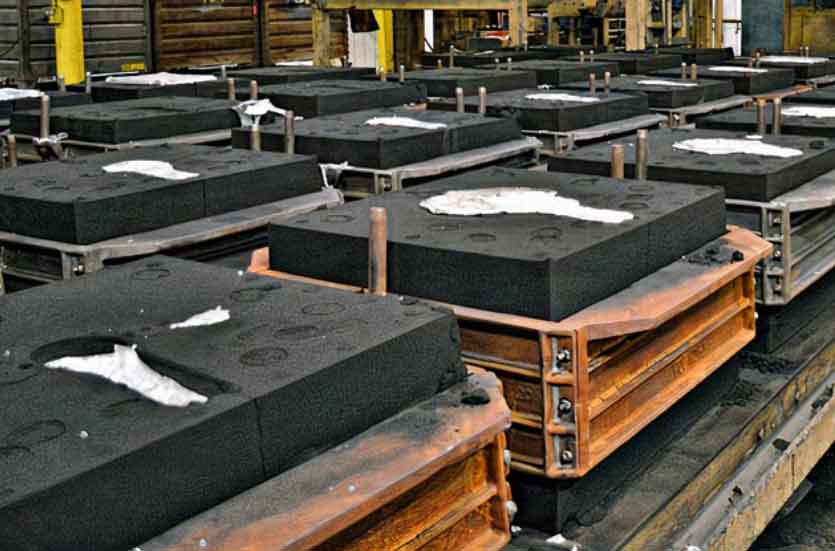
1. Quick Turnaround Time:
Resin sand casting enables relatively quick turnaround times for prototype production. The process does not require extensive tooling or complex setup, allowing for faster production cycles compared to other casting methods. This is particularly beneficial for iterative design processes that require multiple prototypes to be produced and tested within a short timeframe.
2. Cost-Effectiveness:
Resin sand casting is a cost-effective solution for prototype production. The lower tooling costs and material efficiency associated with resin sand casting help keep prototyping expenses manageable, especially in comparison to methods like die casting or investment casting. This cost-effectiveness allows for the production of multiple prototypes for testing and validation without significant financial burden.
3. Design Flexibility:
Resin sand casting offers design flexibility, making it suitable for prototyping complex and customized components. Design modifications can be easily incorporated during the pattern-making stage, allowing for iterative improvements based on testing and feedback. The ability to quickly iterate and validate design changes helps refine the product concept and optimize its functionality.
4. Material Selection:
Resin sand casting supports a wide range of materials, including various alloys, which allows for material selection based on prototyping needs. Different material properties can be explored and tested in the prototype stage to determine the most suitable material for the final product. This flexibility in material selection helps ensure that prototypes accurately represent the intended performance and characteristics of the end product.
5. Dimensional Accuracy and Detail:
Resin sand casting can achieve high dimensional accuracy and capture intricate details, making it suitable for prototyping components with complex geometries and fine features. This allows designers and engineers to validate the form, fit, and function of the prototype accurately. The high level of detail in resin sand casting helps ensure that prototypes closely resemble the final product.
6. Functional Testing:
Resin sand casting produces prototypes that are structurally sound and can undergo functional testing. The prototypes can be subjected to various tests, such as mechanical stress, thermal performance, or fluid flow analysis, to validate their functionality and performance. This enables engineers to identify design flaws or areas for improvement early in the prototyping process.
7. Design Validation and Feedback:
Resin sand casting provides physical prototypes that can be evaluated and tested for design validation. The prototypes can be reviewed by stakeholders, clients, or end-users to gather feedback and make necessary design adjustments. This iterative feedback loop helps refine the design, ensuring that the final product meets the desired requirements and user expectations.
By leveraging resin sand casting for prototyping, manufacturers can rapidly iterate designs, validate concepts, and gather crucial feedback before proceeding to full-scale production. The cost-effectiveness, design flexibility, dimensional accuracy, and functional testing capabilities of resin sand casting make it an effective tool for prototype development and design validation processes.