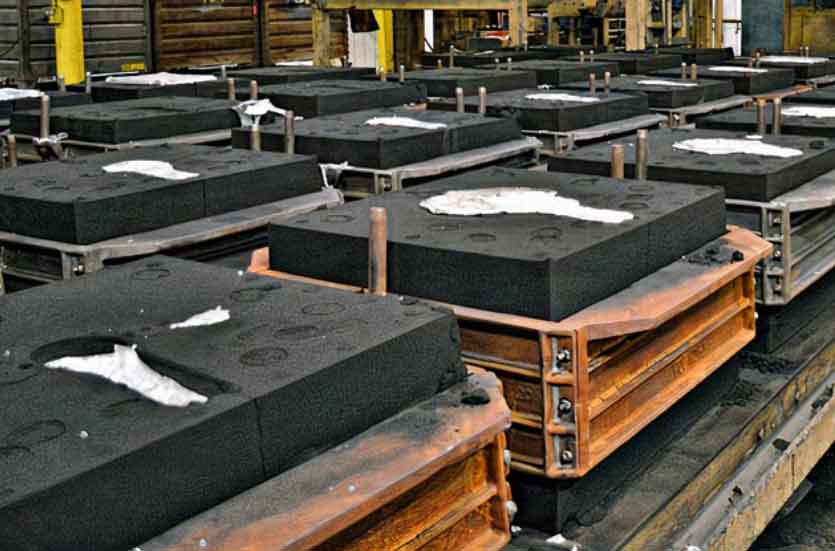
Resin sand casting plays a crucial role in automotive engineering, providing a cost-effective and versatile casting method for producing various automotive components. Its ability to create complex shapes and intricate details makes it well-suited for a wide range of applications in the automotive industry. Let’s explore some of the key applications and innovations of resin sand casting in automotive engineering:
Applications of Resin Sand Casting in Automotive Engineering:
- Engine Blocks and Cylinder Heads: Resin sand casting is commonly used to manufacture engine blocks and cylinder heads. The process allows for intricate cooling passages and precise machining features to optimize engine performance and fuel efficiency.
- Transmission Housings: Automotive transmission housings often require complex shapes and internal structures. Resin sand casting enables the production of such components with high dimensional accuracy.
- Intake Manifolds and Exhaust Manifolds: Resin sand casting is employed to produce intake manifolds and exhaust manifolds, which demand intricate designs and tight tolerances for proper airflow and exhaust gas management.
- Suspension Components: Automotive suspension components, such as control arms and knuckles, can be cast using resin sand casting to achieve the necessary strength and durability.
- Brake Components: Brake calipers, brackets, and other brake system components can be efficiently produced through resin sand casting.
- Steering System Parts: Steering gear housings and other steering system components are well-suited for resin sand casting due to their complex geometries.
- Exterior and Interior Trim: Resin sand casting can be used to create decorative trim pieces for both the exterior and interior of vehicles.
Innovations in Resin Sand Casting for Automotive Engineering:
- Lightweighting Solutions: Resin sand casting is being used in automotive engineering to explore lightweighting options. By optimizing casting designs and using lightweight materials like aluminum alloys, automotive manufacturers can reduce vehicle weight, leading to improved fuel efficiency and reduced emissions.
- Additive Manufacturing Integration: Resin sand casting can be combined with additive manufacturing (3D printing) to create hybrid molds that allow for even more intricate designs and rapid prototyping of automotive components.
- Sustainable Casting Practices: There is a growing focus on adopting sustainable practices in automotive engineering. Manufacturers are exploring the use of eco-friendly resins and reclaimed sand to reduce the environmental impact of the casting process.
- Improved Surface Finish: Advancements in molding technologies and materials are leading to improved surface finish in resin sand casting, reducing the need for post-casting machining and finishing.
- In-Mold Cores and Inserts: Innovations in core and insert design allow for the incorporation of precast components within the mold, enabling the creation of complex internal features in the castings.
- Simulation and Optimization Software: Automotive engineers are increasingly utilizing simulation and optimization software to analyze and optimize the casting process, leading to improved efficiency and casting quality.
- Integration of Advanced Materials: Resin sand casting is being adapted to work with advanced materials like high-strength alloys, enabling the production of lightweight yet durable automotive components.
Resin sand casting plays a critical role in the automotive engineering industry, offering numerous applications and possibilities for innovation. The ability to produce complex shapes, optimize casting designs, and integrate advanced materials makes resin sand casting an indispensable process for manufacturing high-quality automotive components efficiently. As automotive manufacturers continue to seek lightweight and sustainable solutions, resin sand casting is likely to see further advancements and wider adoption in the automotive engineering sector.