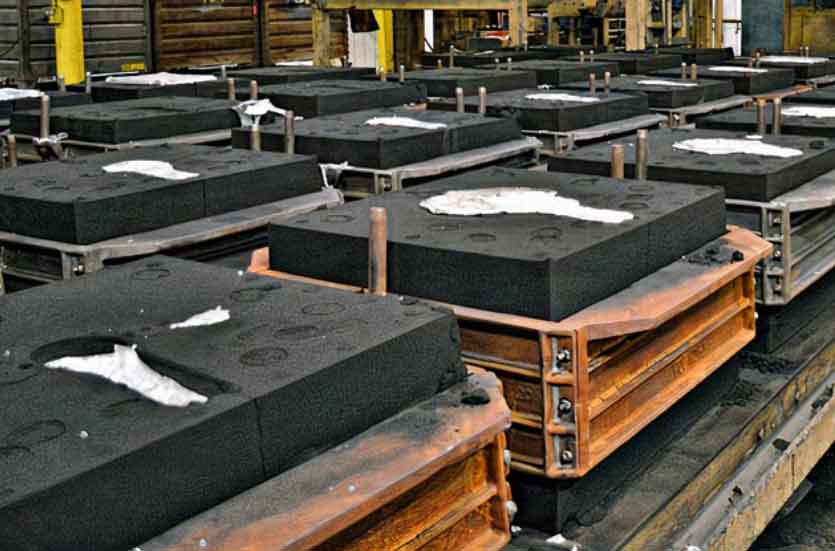
In the era of 3D printing, resin sand casting remains a valuable and relevant casting method, and its combination with 3D printing technology opens up new possibilities for the manufacturing industry. By blending traditional resin sand casting with modern 3D printing techniques, manufacturers can leverage the strengths of both approaches, allowing for greater design flexibility, rapid prototyping, and cost-effective production. Here’s how the combination of old and new techniques can enhance the resin sand casting process:
1. Rapid Prototyping and Pattern Creation:
3D printing enables the quick and precise fabrication of intricate patterns directly from digital designs. This significantly reduces the time and cost required for pattern making in traditional resin sand casting. Rapid prototyping with 3D printing allows manufacturers to test multiple design iterations, identify potential issues, and optimize designs before producing the final pattern.
2. Complex Geometry and Customization:
With 3D printing, intricate and complex geometries that were difficult to achieve with traditional pattern-making methods can be easily realized. By 3D printing the pattern directly, manufacturers can create highly customized and unique castings, catering to specific customer requirements or design needs.
3. Hybrid Molds:
3D printing can be used to create hybrid molds, combining 3D-printed cores or inserts with traditional resin sand mold components. This approach allows for the production of complex castings with internal features that may not be feasible using traditional methods alone.
4. Reduced Material Waste:
Combining 3D printing with resin sand casting allows for more precise and efficient material usage. 3D printing enables the production of patterns with minimal material waste, reducing overall material costs.
5. Enhanced Casting Simulation:
By using 3D-printed patterns, manufacturers can perform advanced casting simulations with greater accuracy. This helps predict casting defects and optimize the resin sand casting process for better quality and dimensional accuracy.
6. Improved Casting Accuracy and Consistency:
The combination of 3D printing and resin sand casting allows for better control over pattern quality and mold production. This results in improved casting accuracy and consistency, leading to fewer defects and a higher quality end product.
7. Customization and Low-Volume Production:
The integration of 3D printing with resin sand casting enables cost-effective customization and low-volume production. Manufacturers can produce small batches of complex and customized castings without the need for expensive tooling.
8. Bridging the Skills Gap:
The adoption of 3D printing in resin sand casting can help bridge the skills gap by reducing the reliance on highly skilled pattern makers. The technology allows for more automated and digital workflows, making it easier for new talent to adapt and contribute to the manufacturing process.
Combining traditional resin sand casting with 3D printing presents a powerful and versatile approach to modern manufacturing. The integration of these techniques allows for greater design flexibility, faster prototyping, reduced material waste, and improved casting accuracy. By embracing the best of both worlds, manufacturers can stay competitive and meet the increasing demands for customized, complex, and high-quality castings in various industries.