Resin sand casting is an advanced casting technique that combines the benefits of traditional sand casting with the versatility and design freedom offered by modern resins. It allows for the creation of complex and intricate metal parts with exceptional dimensional accuracy and surface finish. By pushing the boundaries of design and functionality, resin sand casting has revolutionized the manufacturing industry.
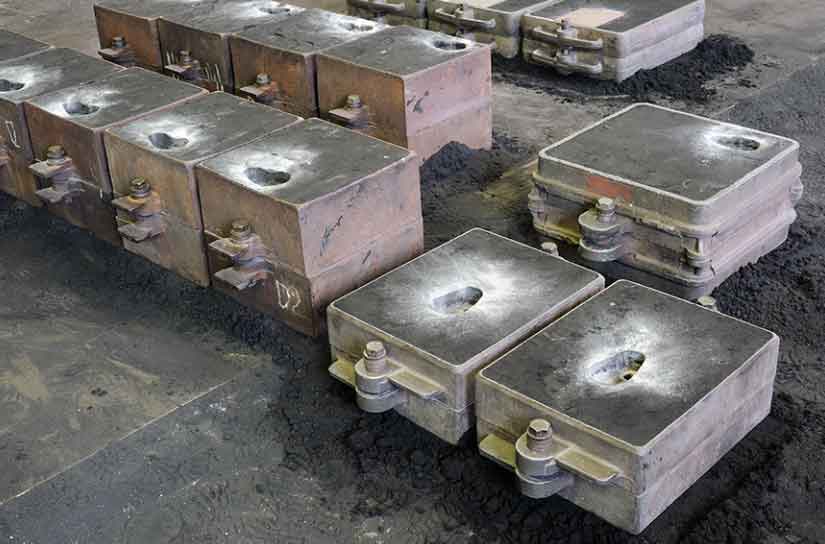
Here are some ways resin sand casting pushes the boundaries of design and functionality:
- Complex Geometries: Resin sand casting enables the production of intricate and complex part geometries that would be difficult or impossible to achieve using conventional sand casting methods. The use of resins allows for greater mold strength and stability, allowing for the creation of intricate details, thin walls, undercuts, and complex internal structures.
- Design Freedom: Resin sand casting provides designers and engineers with greater freedom in terms of part design. The use of resins allows for the production of parts with varying wall thicknesses, curved surfaces, and complex shapes. This design freedom opens up new possibilities for creating innovative and unique products.
- Improved Surface Finish: Resin sand casting offers superior surface finish compared to traditional sand casting methods. The resin-bonded sand used in this process provides a smoother and more consistent mold surface, resulting in parts with excellent dimensional accuracy and reduced surface defects. This makes resin sand casting suitable for applications where aesthetics and precision are crucial.
- Enhanced Functionality: Resin sand casting allows for the integration of functional features directly into the cast parts. With the ability to create complex internal structures, channels, and undercuts, it becomes possible to incorporate features such as cooling channels, fluid flow paths, and internal reinforcements. This opens up opportunities for creating parts with improved performance, efficiency, and functionality.
- Reduced Manufacturing Time: Resin sand casting can significantly reduce the manufacturing time compared to other casting processes. The use of resins enables faster mold production, as they cure more quickly than traditional binders. Additionally, the dimensional accuracy and excellent surface finish achieved in resin sand casting often eliminate or minimize the need for extensive post-casting machining, further reducing production time and costs.
- Material Versatility: Resin sand casting can be used with a wide range of metals and alloys, including aluminum, bronze, iron, and steel. This versatility allows manufacturers to select the most suitable material for their specific application, ensuring optimal performance and functionality of the cast parts.
Resin sand casting pushes the boundaries of design and functionality by offering designers and engineers greater freedom in part design, enabling the creation of complex geometries, providing improved surface finish, enhancing functionality through the integration of functional features, reducing manufacturing time, and accommodating a wide range of materials. This advanced casting technique has revolutionized the manufacturing industry by enabling the production of highly customized and innovative metal parts with exceptional precision and performance.