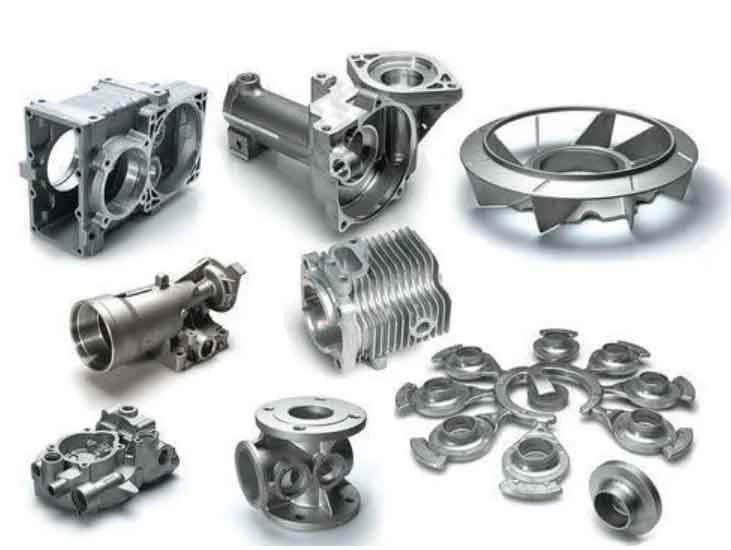
Resin sand casting and green sand casting are two popular metal casting methods used in the foundry industry. Both processes involve the use of sand molds, but they differ in the sand preparation and bonding techniques. Here’s a comparison of resin sand casting and green sand casting:
Resin Sand Casting:
- Sand Preparation: Resin sand casting uses pre-coated sand, where the sand grains are coated with a resin binder before molding. This resin-coated sand mixture is referred to as “shell sand.”
- Mold Hardening: The mold is hardened by curing the resin-coated sand with a catalyst or heat. This results in a hard and rigid mold with a smooth surface finish.
- Mold Reusability: Resin sand molds are typically expendable and cannot be reused, as the sand becomes chemically bonded during the curing process.
- Surface Finish: Resin sand casting offers a superior surface finish and dimensional accuracy compared to green sand casting.
- Casting Quality: Resin sand casting tends to produce high-quality castings with minimal defects, thanks to the precise mold cavity and reduced gas-related issues.
- Suitable Applications: Resin sand casting is well-suited for complex shapes, thin sections, and applications that require high dimensional accuracy and fine surface finish.
- Cost: While the initial setup costs for resin sand casting might be higher due to the need for resin-coated sand and mold hardening equipment, the process can be cost-effective for both low and high-volume production runs due to reduced finishing requirements and improved casting quality.
Green Sand Casting:
- Sand Preparation: Green sand casting uses naturally bonded sand, known as “green sand,” which is a mixture of silica sand, clay, water, and other additives.
- Mold Hardening: The mold is not hardened by curing; instead, it relies on the moisture content in the green sand to maintain mold integrity.
- Mold Reusability: Green sand molds can be reused multiple times by reconditioning the sand mixture through a mulling process.
- Surface Finish: Green sand casting may result in a slightly rougher surface finish compared to resin sand casting due to the nature of the sand mixture.
- Casting Quality: While green sand casting can produce quality castings, the surface finish and dimensional accuracy may not be as precise as resin sand casting.
- Suitable Applications: Green sand casting is versatile and suitable for a wide range of applications, including large and simple shapes.
- Cost: Green sand casting is generally more cost-effective for large and simple castings, especially when the molds can be reused multiple times.
Resin sand casting is preferred when high dimensional accuracy, fine surface finish, and complex shapes are required. Green sand casting, on the other hand, is more suitable for applications where cost-effectiveness and mold reusability are essential, especially for large and simple castings. Both methods have their advantages and are valuable in different casting scenarios based on specific requirements and project constraints.