The thickness of nitrided layer in three parts of lzqt600-3 ductile iron profile was measured. It can be seen from the surface that with the increase of nitriding temperature, the diffusion of active N atoms and C atoms will accelerate, and the thickness of CLS layer and DLS layer on the surface of the sample will increase, which basically conforms to the parabola law, that is, the growth rate of the infiltrated layer is fast in a short time, and then gradually slows down. After increasing the holding time, the thickness of the infiltrated layer continues to increase, and finally reaches a stable value.
According to the internal measurement data, the thickness of the nitrocarburized layer at the edge, 1 / 2R and the center is different. The nitrided layer at the edge and 1 / 2R is thicker than that at the core, and the thickness of the carburized layer at 1 / 2 of the samples is the highest after nitrocarburizing. This is due to the fact that the cooling rate of molten iron at the edge is faster than that at the 1 / 2R and the core parts in the horizontal continuous casting process. Therefore, the nucleation rate at the edge is high, the number of graphite balls is the largest, the grain size is small and the grain boundary ratio is high. In addition, due to the randomness of sampling at the edge, 1 / 2R and the center, the expected experimental results are more instructive. If the sample at 1 / 2R is taken from the lower end of the profile, the molten iron formed in the solidification process is inclined to the upper part because of its own gravity, so the grain size at 1 / 2R is smaller than that at the edge. The infiltration and diffusion of N and C is along the grain boundary from the surface of the sample to the matrix. Therefore, the thickness of the layer at 1 / 2R is the largest, followed by the edge and the thinnest at the center.
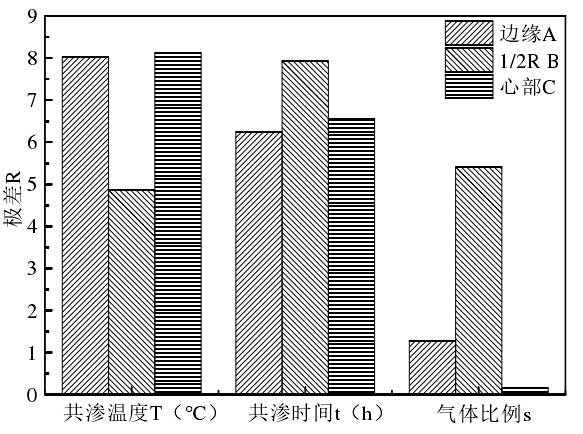
After using the orthogonal test method, the results need to be processed by range analysis and variance analysis. Among them, range analysis can reflect the significance of each factor from the range of the average index at different levels of each factor, and find the optimal collocation. The range analysis was carried out for the thickness data of the three different parts of the edge, 1 / 2R and the center, and the R value was calculated, and the results as shown in Fig. 1 were obtained. By comparing the magnitude of range R in the figure, the important order of the three factors can be obtained. It can be seen from the figure that the primary and secondary order of the factors influencing the thickness of the permeating layer at 1 / 2R in the orthogonal experiment in this paper is as follows: the permeating time t > the gas proportion s > the nitriding temperature T; the primary and secondary order of the factors affecting the thickness of the infiltration layer at the edge and the core is the infiltration temperature T > the time t > the gas proportion s. Considering the application in actual production, the primary and secondary order of influencing factors of 1 / 2R position of lzqt600-3 ductile iron profile is selected as the standard. Therefore, the primary and secondary order of influence of nitriding parameters on the thickness of carburizing layer of lzqt600-3 ductile iron profile is as follows: nitriding time t > gas proportion s > nitriding temperature T.