Soft nitriding, also known as nitrocarburizing, is a process of infiltrating nitrogen into the surface of workpieces and also carbon elements. Nitriding occupies a dominant position, and carburizing is used as an auxiliary. The treatment temperature ranges from 500 ℃ to 600 ℃. Gas medium, molten salt or granular nitriding agent are several common nitrocarburizing process mediums. In the early stage of nitriding process, the treatment time is very long, and the depth of nitrided layer after treatment is about several tenth of millimeter.
It is expected that shorter treatment time will make the process more economical and effective. The two-stage and three-stage gas nitriding, glow plasma nitriding and nitrocarburizing processes have been developed. With the addition of carbon atoms, nitrogen atoms have to penetrate faster, so the mutual promotion between nitrogen and carbon atoms accelerates the infiltration speed. Both nitriding and nitrocarburizing can improve the surface hardness, friction and wear resistance and corrosion resistance of steel parts. At the same time, considering the economy and environmental protection, gas nitriding and nitrocarburizing have low cost, simple operation and easy control, so they are widely used in industry.
Compared with the nitriding process, the surface brittleness of the workpiece is improved more effectively after nitrocarburizing, and the surface strengthening layer is mainly composed of nitride and a small amount of carbide. Therefore, the mechanical properties of the workpiece treated by this process are excellent, with high corrosion resistance and small deformation. Nitrocarburizing process is also widely used in the treatment of grinding machine spindle, exhaust valve, boring bar, engine cylinder and other parts.
Based on the ternary phase diagram of Fe-C-N system, the surface of workpiece was nitrocarburized. Taking iron and steel materials as an example, the solubility of each phase will be changed due to the interaction between carbon and nitrogen atoms, in which the lattice constant of ε – Ee2-3 (n, c) phase (containing nitrogen and carbon compounds) increases. After nitrogen and carbon atoms enter the sample, the brittleness of ε – Fe2-3 (n, c) phase formed on the surface is smaller than that of ε – Fe2-3n phase, and a compound layer with high toughness will be formed on the surface. At the same time, the hardness of ε – Fe2-3 (n, c) phase
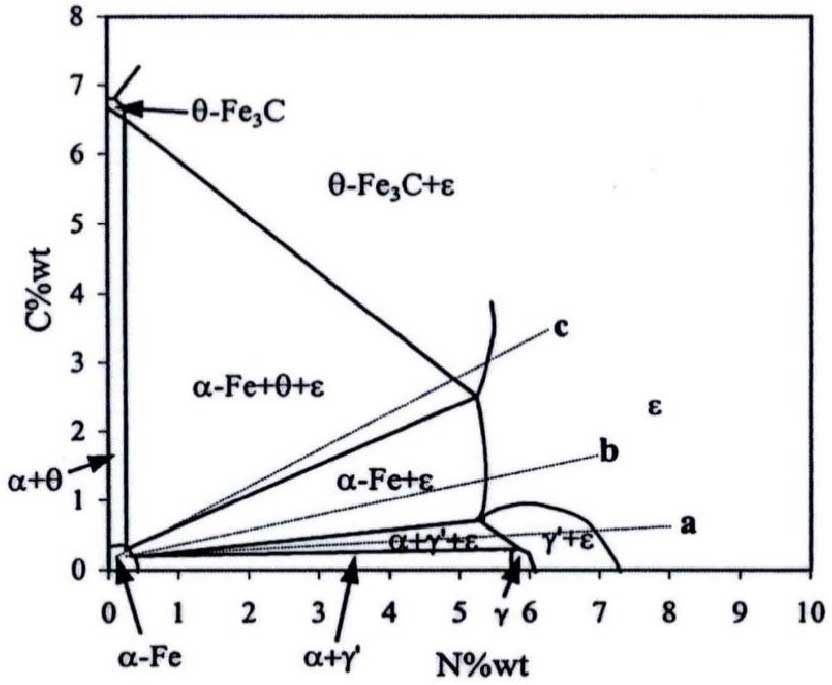
It has been reported that the anti-corrosion effect of ε – fe2-3 (n, c) phase is good. Therefore, one of the means to improve the corrosion resistance of workpiece surface is to increase the content of ε – fe2-3 (n, c) phase in the compound layer. Fig. shows the phase diagram of Fe-C-N system at 570 ℃ ~ 580 ℃. Therefore, in order to obtain the unidirectional compound layer with dense structure, the infiltration parameters can be changed appropriately.