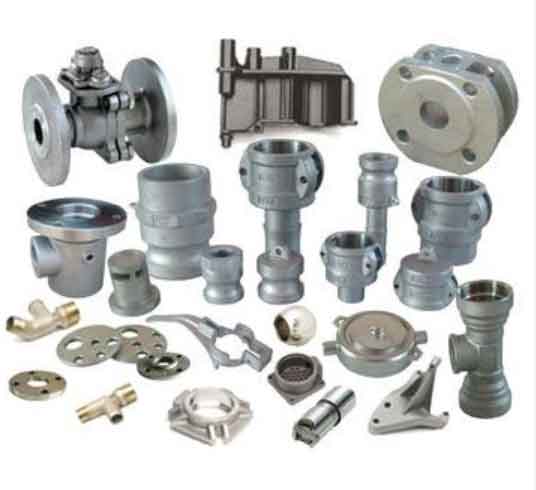
Sand casting, a traditional foundry technique that dates back thousands of years, remains relevant and widely used in modern manufacturing processes. Despite advancements in technology and the emergence of alternative casting methods, sand casting continues to offer several advantages that make it a viable and preferred choice for producing a wide range of metal parts. Let’s explore why sand casting remains relevant in today’s industrial landscape:
Versatility and Adaptability:
Sand casting is highly versatile and can accommodate the production of small to large-scale components with varying levels of complexity. Its adaptability to different shapes, sizes, and alloys makes it suitable for a wide range of industries, including automotive, aerospace, construction, and more. Sand casting can produce intricate designs, complex geometries, and components of various weights, meeting diverse manufacturing needs.
Cost-Effectiveness:
Sand casting offers cost advantages, particularly when producing medium to large volumes of parts. The low initial tooling costs and the use of relatively inexpensive materials, such as sand and pattern materials, make sand casting a cost-effective option compared to other casting methods. Additionally, the ability to reuse sand through reclamation processes further enhances the cost efficiency of sand casting.
Design Freedom:
Sand casting allows for design flexibility and freedom that other manufacturing processes may not offer. Complex shapes, undercuts, and internal cavities can be easily incorporated into sand castings. Design modifications and iterations can be quickly implemented during the pattern-making stage, enabling designers to refine and optimize their designs before committing to mass production.
Prototype Development:
Sand casting is well-suited for prototype development and low-volume production. Its relatively low tooling costs and shorter lead times compared to other casting methods make it an ideal choice for producing prototypes for functional testing, evaluation, and market validation. Sand casting enables designers and engineers to iterate and refine their designs quickly, reducing the time and cost associated with the product development cycle.
Material Compatibility:
Sand casting is compatible with a wide range of metal alloys, including ferrous and non-ferrous metals. It can produce castings from aluminum, bronze, iron, steel, and many other alloys. This material compatibility allows manufacturers to choose the most suitable alloy for the desired properties of the final product, such as strength, corrosion resistance, or heat resistance.
Tooling Flexibility:
Sand casting offers flexibility in tooling, allowing for quick modifications or adaptations. If design changes are required during the production process, adjustments to the sand mold or pattern can be made relatively easily and at a lower cost compared to other casting methods. This tooling flexibility facilitates agility in manufacturing, accommodating design changes or customization requirements.
Time-Tested Reliability:
Sand casting has a long history of successful use in various industries. Its time-tested reliability and proven track record make it a trusted method for producing high-quality castings. Foundries and casting professionals have honed their skills and expertise in sand casting, ensuring consistent results and reliable production processes.
While newer casting technologies, such as investment casting or die casting, have emerged, sand casting continues to be a viable and preferred choice for many applications. Its versatility, cost-effectiveness, design freedom, and time-tested reliability make sand casting a valuable technique in the modern manufacturing landscape. By leveraging its strengths and advancements in process control and optimization, sand casting remains a relevant and widely adopted method for producing metal parts.