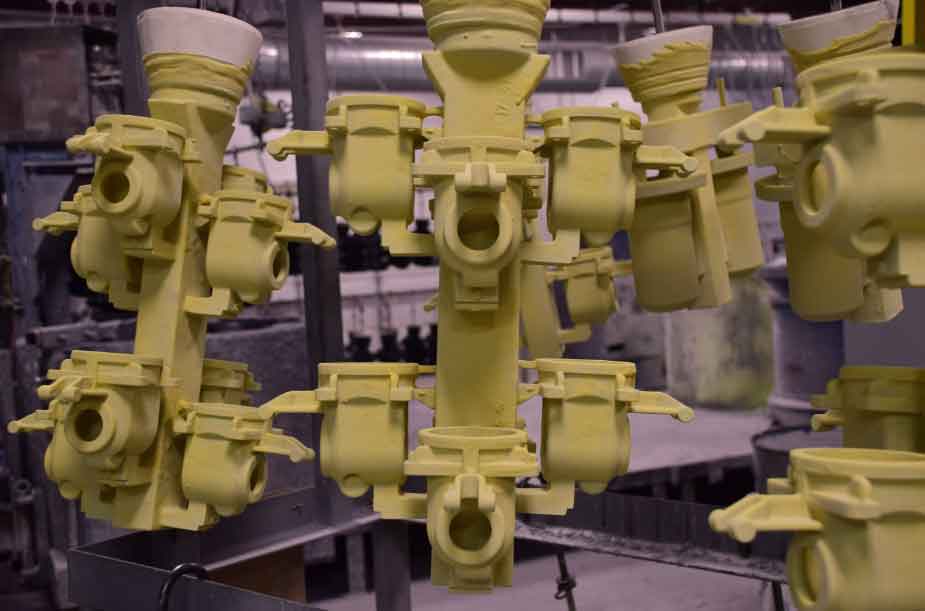
Sand casting in the foundry involves various techniques, poses unique challenges, and requires adherence to best practices to ensure successful casting production. Let’s explore these aspects of sand casting in the foundry:
Techniques:
- Pattern Making: Pattern making is the process of creating a replica of the desired part in wood, plastic, or metal. It involves carefully considering factors such as shrinkage, draft angles, and parting lines to ensure proper mold formation.
- Mold Preparation: The mold is created by compacting special molding sand around the pattern. Techniques such as green sand molding (using moist sand), dry sand molding (using chemically bonded sand), or shell molding (using resin-coated sand) may be employed, depending on the requirements of the casting.
- Core Making: Cores are used to create internal cavities or features in the castings. Cores can be made from sand or other materials and are placed inside the mold to form hollow sections or intricate shapes within the casting.
- Mold Assembly: The mold is assembled by joining the cope (top half) and drag (bottom half) of the mold, with cores appropriately positioned if needed. The mold is then securely closed to create a cavity in the shape of the desired part.
- Pouring and Solidification: Molten metal is poured into the mold cavity through a gating system. The metal fills the mold, displacing the air, and solidifies to form the casting. Proper gating design is crucial to ensure proper flow and avoid defects.
- Shakeout and Finishing: After solidification, the mold is removed from the casting in a process called shakeout. The casting is then cleaned, removing any excess sand or other impurities, and further finishing processes such as machining, grinding, or heat treatment may be performed.
Challenges:
- Dimensional Accuracy: Achieving precise dimensional accuracy in sand casting can be challenging due to factors like pattern and mold distortion, sand movement during pouring, and metal shrinkage. Proper mold and pattern design, along with meticulous control of the casting process, help mitigate these challenges.
- Surface Finish: Obtaining the desired surface finish can be challenging in sand casting. Factors such as the type of sand, mold surface quality, and mold coating affect the surface texture of the castings. Post-casting finishing processes, like shot blasting or grinding, may be necessary to achieve the desired surface quality.
- Defects: Sand casting can be susceptible to various defects, including porosity, shrinkage, sand inclusions, and surface defects. These issues can arise due to improper gating and risering design, inadequate venting, or insufficient control over the solidification process. Stringent quality control measures and process optimization can help minimize these defects.
Best Practices:
- Design for Manufacturability: Consider the casting process during the design stage to ensure the part is suitable for sand casting. Incorporate proper draft angles, fillets, and allowances for shrinkage and machining. Collaborate with foundry professionals to optimize the design for manufacturability.
- Pattern and Mold Quality: Invest in high-quality patterns and molds to ensure dimensional accuracy and surface finish. Regular maintenance and inspection of patterns and molds help detect and rectify any issues promptly.
- Gating and Riser Design: Optimize gating and risering systems to promote proper filling, minimize turbulence, and facilitate effective feeding of molten metal. Well-designed gates and risers promote sound castings with minimal defects.
- Sand Control and Testing: Implement proper sand control measures, including moisture content control, sand quality testing, and sand reclamation processes. Regular testing of sand properties ensures consistent casting quality.
- Process Control and Monitoring: Establish robust process control systems to monitor key parameters such as pouring temperature, metal quality, mold hardness, and cooling rates. Regular inspection and testing at various stages of the process help identify deviations and take corrective actions.
- Continuous Improvement: Foster a culture of continuous improvement by analyzing defects, identifying root causes, and implementing corrective measures. Regular review of process performance and the implementation of best practices help enhance casting quality and efficiency.
By following these techniques, overcoming challenges, and adhering to best practices, foundries can achieve consistent and high-quality sand castings, meeting the specifications and requirements of various industries.