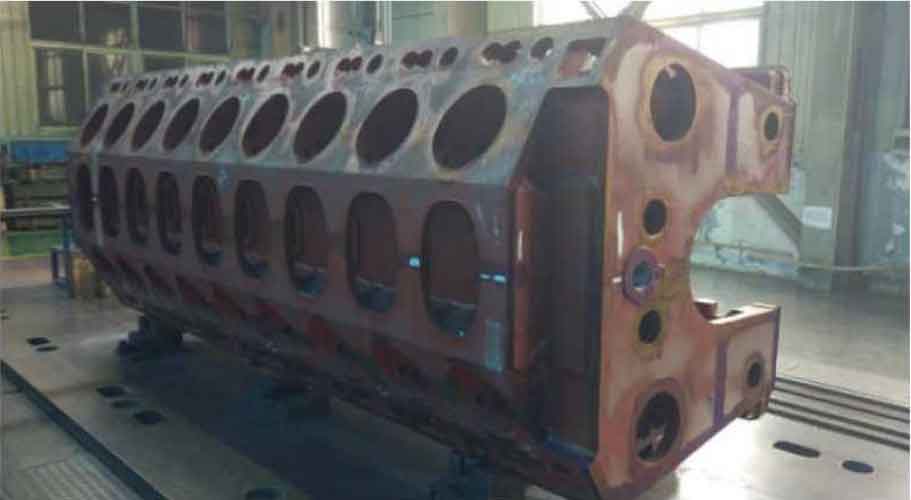
The links are mainly from the molding, core making, box matching, pouring, cleaning and heat treatment processes. Firstly, the heat treatment and cleaning procedures are excluded. The reason is that the cleaning procedure is mainly to polish the internal and external surfaces of the casting after the sand casting is completed. The purpose is to remove the excessive parts such as the slug system and the flash, and will not affect the solid quality of the sand casting. The heat treatment method is annealing, which is used to eliminate the internal stress. At this time, the external state of the sand casting has been finalized, and it will not be scrapped due to the heat treatment.
1.Shape
In order to ensure the product quality, the sand mold casting of the fuselage adopts the method that the cylinder hole faces down. According to this process design, the molding process mainly uses the mold to make the upper mold and the lower mold, and the main part of the casting exists in the lower mold. Take this casting mold as an example. First, the cold iron and ceramic pipe shall be placed at the designated position of the mold according to the process requirements, and then sand filling, box turning, mold repairing, coating and drying shall be carried out. The difficulty in the process is that there are many cold irons with different shapes. It is necessary to ensure the correct position. In addition, it is necessary to ensure the strength of the sand mold, especially the turnover link.
2.Core making
18PA6B cement core has a large number and complex types, with more than 40 kinds and more than 120 pieces. The process is to inject the evenly stirred resin sand into the core box, harden the core, brush the surface of the cement core with paint, and then dry it. The difficulty in the process is that the number of cement cores is relatively large, and individual cement cores are large in size, with many curved surfaces and complex shapes, which makes it difficult to manufacture. Most of the cement cores need to be placed at the specified position. If the cold iron is not well combined with the cement core, it will become loose, and sand mold casting defects such as sand holes and air holes will appear in the later stage. Finally, the strength of the sand mold. If the strength is not enough, various defects will occur in the pouring process.
3.Distribution box
The distribution box is to assemble the manufactured and qualified cement core according to the process requirements, and finally dry the distribution box with hot air. The distribution box is similar to the assembly link in mechanical equipment manufacturing, but it has the characteristics of the industry, and there are many hidden links in the process. The main reason is that after the cement core is installed, it is impossible to carry out coverage inspection on the previous process, and the inspection method is single, only visual inspection supplemented by simple measurement. It is also impossible to inspect the cavity. Although the endoscope and other measuring tools are introduced, due to the complexity of the internal structure, it is impossible to ensure 100% inspection, and it is not fully integrated into the production at the trial stage. Therefore, this process relies more on the experience of personnel, and requires higher skills and sense of responsibility. Finally, it is the characteristics of sand casting industry. The ventilation and lighting environment in the workshop are relatively poor, and there is much dust. It is difficult to control the cleanliness and prevent foreign matters.
4.Pouring
During pouring, the raw materials are first refined in the medium frequency furnace, and then the molten iron is injected into the cavity of the distribution box. The process focuses on temperature control and slag removal during smelting to ensure the removal of harmful elements such as s and P. At the same time, attention should be paid to the addition of spheroidizing agent and inoculant to improve the spheroidizing inoculation effect. Combined with the actual situation of the production workshop, the intermediate frequency furnace is a distance from the distribution box. It is difficult to control the molten iron temperature and pouring time when the molten iron ladle is used to transfer the molten iron. In addition, safety supervision shall be simulated during pouring to avoid safety accidents.