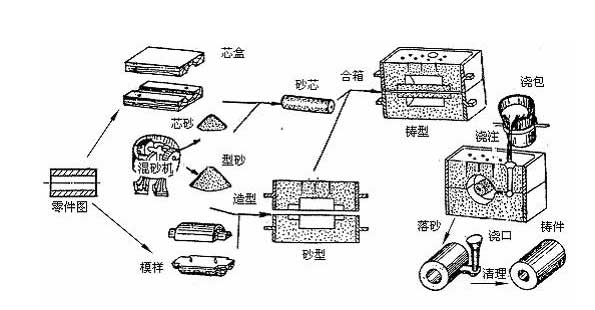
Sand casting is a kind of traditional casting technology which takes sand as the main molding material to make the mold. Generally, gravity casting is used for sand mold, and low-pressure casting, centrifugal casting and other processes can be used when there are special requirements. Sand casting has a wide range of adaptability, small, large, simple, complex, single, mass can be used. The mold used for sand casting was usually made of wood, commonly known as wood mold. In addition, the fire resistance of sand mold is higher than that of metal mold, so the materials with higher melting point, such as copper alloy and ferrous metal, also use this process. However, there are some disadvantages of sand casting: because each sand casting can only be poured once, the mold is damaged after the casting is obtained, and must be reshaped, so the production efficiency of sand casting is low; and because the overall property of sand is soft and porous, the size accuracy of sand casting is low, and the surface is rough.
Steel, iron and most non-ferrous alloy castings can be obtained by sand casting. Because the molding materials used in sand casting are cheap and easy to obtain, and the mold manufacturing is simple, it can adapt to the single production, batch production and mass production of castings. For a long time, it has been the basic process in casting production.
The mold used in sand casting is generally composed of outer sand mold and core. In order to improve the surface quality of castings, a layer of coating is often applied to the surface of sand mold and core. The main components of the coating are powder materials and binders with high fire resistance and high temperature chemical stability. In addition, carriers (water or other solvents) and various additives are added for easy application.