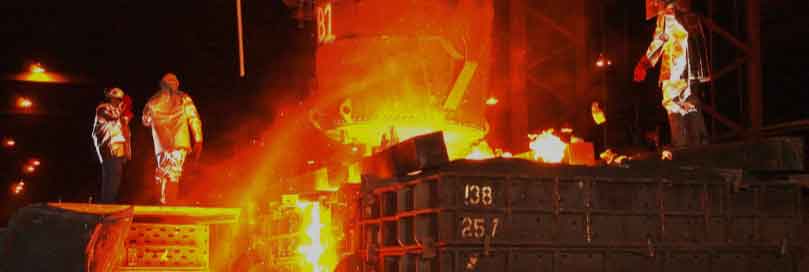
In the age of sustainability, sand casting manufacturers are increasingly adopting eco-friendly practices and initiatives to reduce their environmental impact and promote sustainable manufacturing. Here are some common eco-friendly practices that sand casting manufacturers are implementing:
- Sand Reclamation: Sand reclamation systems are used to recycle and reuse sand after the casting process. This reduces the need for fresh sand, conserves natural resources, and minimizes waste generation.
- Use of Eco-Friendly Binders and Coatings: Manufacturers are opting for eco-friendly binders and coatings in the sand casting process. These alternatives have lower environmental impacts compared to traditional chemical binders.
- Energy Efficiency: Sand casting foundries are investing in energy-efficient technologies to reduce energy consumption. Implementing energy-efficient equipment and processes can lower greenhouse gas emissions and decrease the overall environmental footprint.
- Water Recycling and Conservation: Foundries are implementing water recycling systems to reduce water consumption and minimize water wastage during the casting process.
- Waste Minimization and Recycling: Manufacturers are taking measures to minimize waste generation and increase recycling rates. Scrap metal and other recyclable materials are often recycled instead of being discarded.
- Green Packaging: Eco-friendly packaging materials, such as biodegradable or recyclable materials, are being used to reduce packaging waste.
- Pollution Control: Sand casting manufacturers are implementing pollution control measures to reduce air emissions and ensure compliance with environmental regulations.
- Life Cycle Assessments: Some manufacturers conduct life cycle assessments to evaluate the environmental impacts of their sand casting processes. This helps identify areas for improvement and sustainable practices.
- Green Certifications: Some sand casting foundries seek green certifications, such as ISO 14001 (Environmental Management System), to demonstrate their commitment to environmental responsibility.
- Sustainable Sourcing: Manufacturers are increasingly sourcing raw materials, such as sand and metal alloys, from sustainable and responsible suppliers.
- Community Engagement: Sand casting manufacturers engage with local communities to raise awareness of environmental issues and implement sustainable practices beyond their facility boundaries.
- Research and Development: Investment in research and development focuses on developing new, sustainable materials and processes that further reduce the environmental impact of sand casting.
As global awareness of environmental issues grows, the demand for sustainable manufacturing practices increases. Many sand casting manufacturers recognize the importance of adopting eco-friendly initiatives to stay competitive, meet customer expectations, and contribute to a greener future. Embracing sustainable practices not only benefits the environment but also enhances the reputation of sand casting manufacturers as responsible and forward-thinking partners in the industry.