Chapter 1: The Overall Process Flow of Sand Casting

Here’s a step-by-step overview of the sand casting process, including designing models, preparing molds, preparing sand, casting and melting metals, cooling and solidification, demolding, cleaning, and post-processing:
1. Designing Models:
- The process starts with creating a pattern or model of the desired part. This can be made from wood, plastic, or metal.
- The pattern is an exact replica of the final casting, including any cavities, features, and surface textures.
2. Mold Preparation:
- A two-part mold is created around the pattern to form the cavity where the molten metal will be poured.
- The mold is typically made of sand, which is packed around the pattern.
3. Preparing Sand:
- Special molding sand is mixed with a binder (often clay) to improve its cohesiveness and strength.
- The sand mixture is compacted around the pattern to form the mold.
4. Core Assembly (Optional):
- Cores made from sand or other materials are inserted into the mold to create internal cavities in the casting.
- Cores are used when the casting requires hollow sections or complex internal geometries.
5. Casting and Melting Metals:
- The mold is securely closed, and molten metal is poured into the mold cavity through a gating system that directs the flow.
- The metal is often melted in a furnace and maintained at a specific temperature to ensure proper pouring and filling.
6. Cooling and Solidification:
- Once poured, the metal cools and solidifies within the mold.
- Solidification starts at the mold walls and progresses toward the center, influencing the casting’s microstructure and properties.
7. Demolding:
- After the metal has solidified and cooled, the mold is opened, and the casting is removed.
- The pattern may be destroyed during this process, as it is typically embedded within the sand mold.
8. Cleaning:
- The casting is cleaned to remove excess sand, mold materials, and any adhering residues.
- Techniques such as shaking, sandblasting, or mechanical methods are used for cleaning.
9. Post-Processing:
- The casting may undergo further processes to achieve desired dimensions, surface finish, and properties.
- Machining, grinding, heat treatment, and surface coating are common post-processing steps.
10. Inspection and Quality Control:
- The final casting is inspected for defects, dimensional accuracy, and adherence to specifications.
- Non-destructive testing methods may be used to identify any internal defects.
11. Final Product:
- The completed casting is now ready for use in its intended application.
Sand casting is a versatile and widely used manufacturing process that allows for the production of a wide range of parts, from small to large and simple to complex. The process flow described above provides a fundamental understanding of how sand casting works and the key steps involved in creating metal castings.
Chapter 2: Sand Casting Materials and Equipment
Understanding the materials and equipment used in sand casting is crucial for successful and efficient production. Here’s an overview of the characteristics, selection, treatment, and usage methods of the materials involved in sand casting, as well as relevant equipment:
1. Model Materials:
- Models are used to create patterns that form the mold cavity. Common model materials include wood, plastic, and metal.
- Characteristics: Models should be dimensionally stable, durable, and capable of replicating intricate details.
- Selection and Usage: Choose a model material based on factors such as part complexity, size, and production volume. Models are used to create the pattern for the mold.
2. Sand Materials:
- Sand is the primary molding material used to create the mold cavity.
- Characteristics: Sand should have good moldability, strength, refractoriness, and permeability.
- Selection and Usage: Different types of sand, such as green sand, resin-coated sand, and dry sand, can be used based on the casting requirements. Sand is packed around the pattern to create the mold.
3. Release Agents:
- Release agents are applied to the mold surface to prevent the casting from sticking to the mold.
- Characteristics: Release agents should provide a smooth and effective separation between the casting and the mold.
- Selection and Usage: Choose a release agent that is compatible with the sand and casting material. Apply the release agent to the mold cavity before packing the sand.
4. Melted Metals:
- Melted metals are poured into the mold cavity to create the final casting.
- Characteristics: Casting alloys should have the desired mechanical properties, melting points, and flow characteristics.
- Selection and Usage: Choose a suitable casting alloy based on the part’s intended use and characteristics. Melt the metal in a furnace and pour it into the mold cavity.
5. Mold Preparation Equipment:
- Mold preparation equipment includes tools and machinery used to create the mold cavity.
- Equipment: Molding machines, molding boxes, pattern plates, and core boxes.
- Usage: Use molding equipment to form the sand mold around the pattern and core boxes to create internal cavities.
6. Casting Furnaces:
- Casting furnaces are used to melt the metal to be poured into the mold.
- Equipment: Crucible furnaces, induction furnaces, and electric arc furnaces.
- Usage: Preheat the furnace, load the metal, and melt it to the desired temperature before pouring it into the mold.
7. Demolding Equipment:
- Demolding equipment helps remove the casting from the mold after solidification.
- Equipment: Knockout machines, vibratory tables, and hydraulic presses.
- Usage: Use demolding equipment to safely and efficiently remove the casting from the mold without causing damage.
8. Cleaning and Finishing Equipment:
- After demolding, castings need cleaning and finishing.
- Equipment: Shot blasting machines, tumbling barrels, and grinding equipment.
- Usage: Clean, deburr, and finish the casting to achieve the desired surface quality and dimensions.
Understanding the characteristics and proper usage of these materials and equipment is essential for ensuring high-quality and successful sand casting processes. The selection of materials and equipment should be based on the specific requirements of the casting project and the desired properties of the final castings.
Chapter 3: Preparation of Sand Casting Molds
sand casting is a widely used method for creating metal parts and components. The process involves creating a mold from a mixture of sand and a binder, and then pouring molten metal into the mold to create the desired shape. Here’s an overview of the mold preparation process for sand casting, including the steps you mentioned:
- Pattern or Model Making:
- The first step is to create a pattern or model of the desired object. This pattern is a replica of the final part and is used to create the mold. Patterns can be made from various materials such as wood, plastic, or metal.
- The pattern is usually slightly larger than the desired final part to account for the contraction of metal as it cools.
- Mold Box Preparation:
- A mold box, also known as a flask, is a frame that holds the sand mixture and the pattern. It is usually made of wood or metal.
- The mold box is divided into two halves: the top half (cope) and the bottom half (drag).
- Sand Mixing:
- Sand is mixed with a binder to hold its shape. The binder can be clay, resin, or a combination of materials.
- The sand mixture needs to have good flowability and compactability to ensure that it fills the mold cavity and reproduces the pattern accurately.
- Pattern Placement:
- The pattern is placed in the drag half of the mold box.
- To aid in mold release and prevent the pattern from sticking to the sand, a release agent such as talc or graphite is often applied.
- Sand Filling and Compaction:
- The drag is filled with the sand mixture and compacted using various methods, such as hand ramming, jolting, or squeezing.
- The sand is compacted around the pattern to create the mold cavity.
- Core Preparation (if required):
- Cores are used to create hollow areas or complex shapes within the final casting.
- Core boxes are created using a similar process to pattern making. The core box is filled with sand and compacted to create the core.
- Cores are then placed in the mold to form the desired internal features.
- Closing the Mold:
- The cope half of the mold box is placed on top of the drag half, enclosing the pattern and any cores.
- The two halves of the mold are securely clamped together.
- Pouring Channel and Vents:
- Channels for pouring molten metal (sprue) and for allowing gases to escape (vents) are created in the sand.
- These channels ensure proper filling of the mold and help prevent defects like porosity.
- Mold Release:
- The mold is carefully opened, and the pattern is removed, leaving behind the mold cavity and any cores.
- Casting:
- Molten metal is poured into the mold through the sprue.
- Cooling and Solidification:
- The metal cools and solidifies inside the mold, taking on the shape of the cavity.
- Casting Removal:
- After the metal has solidified, the mold is opened, and the casting is removed.
Vibration compaction is a technique used during the sand compaction step to further ensure that the sand is uniformly packed around the pattern. It helps reduce voids and ensures better surface finish.
It’s important to note that sand casting is a complex process that requires careful attention to detail and a good understanding of materials and techniques to produce high-quality castings. Different variations and improvements might exist based on specific requirements and the type of metal being cast.
Chapter 4: Sand Mold and Sand Material of Sand Casting
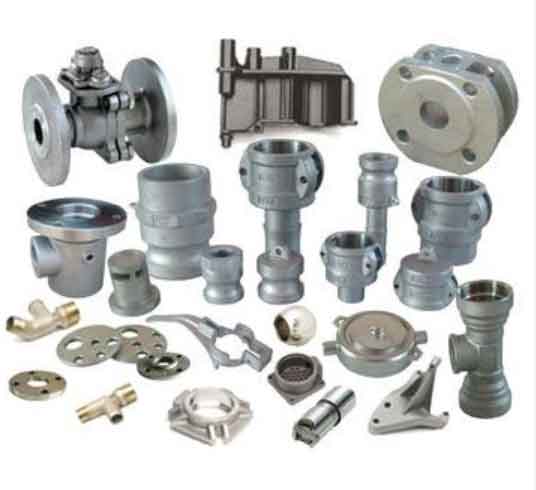
The choice of sand materials and their preparation are crucial aspects of sand casting. The properties of the sand used in the mold can greatly influence the quality of the final casting. Here’s an overview of different types of sand materials, their characteristics, preparation methods, and their applications in casting, as well as some key design principles for sand molds:
Types of Sand Materials:
- Green Sand:
- Green sand is the most commonly used material in sand casting.
- It consists of silica sand mixed with clay and water.
- The clay provides bonding properties, and water helps compact the sand around the pattern.
- Green sand is relatively low-cost and easy to work with.
- Dry Sand:
- Dry sand is sand that is dried before it is used in molding.
- It can be mixed with organic binders or resins to improve its strength and permeability.
- Dry sand molds offer better dimensional accuracy and surface finish than green sand molds.
- Resin-Bonded Sand:
- Resin-bonded sand molds use a mixture of sand and a resin binder.
- The resin is cured or hardened to create a strong mold.
- These molds have good strength, high dimensional accuracy, and good surface finish.
- Shell Molding Sand:
- Shell molding involves using resin-coated sand that is heated to create a shell-like mold.
- The molds have excellent surface finish and dimensional accuracy.
- Shell molding is suitable for high-precision casting.
- Ceramic Sand:
- Ceramic sand molds are made using a mixture of sand and inorganic binders.
- They offer good refractory properties and can handle high temperatures.
- Ceramic sand molds are used for casting metals with high melting points.
Sand Preparation Methods:
- Sand is prepared by mixing it with binders, additives, and water (if needed).
- The mixture is then compacted around the pattern to create the mold cavity.
- Different sand types require specific preparation methods, including mulling, mixing, and tempering.
Design Principles of Sand Molds:
- Parting Line and Draft Angle:
- The parting line is the dividing line between the cope and drag halves of the mold.
- Draft angles are included to allow for easy removal of the pattern and the casting from the mold.
- Core Design:
- Cores are used to create internal features in the casting.
- Core design should consider factors like core placement, venting, and core supports.
- Gating and Riser Design:
- Proper gating and riser design ensure a smooth flow of molten metal and help prevent defects like porosity and shrinkage.
- Ventilation:
- Vents are included in the mold to allow gases to escape during metal pouring.
- Proper venting prevents gas-related defects in the casting.
- Chaplets and Chills:
- Chaplets are used to support cores and prevent shifting during metal pouring.
- Chills are inserts placed in the mold to promote rapid cooling in specific areas.
Stability of Sand Molds:
- Mold stability is essential to ensure that the mold maintains its shape during metal pouring.
- Proper compaction, appropriate sand mix, and adequate support structures contribute to mold stability.
The selection of sand materials, their preparation, and the design of sand molds are critical factors in successful sand casting. Each type of sand material offers specific advantages and is suited to different casting requirements. Understanding the principles of mold design, stability, ventilation, and other factors ensures the production of high-quality castings with minimal defects.
Chapter 5: Sand Casting Production Process
Understanding the metal melting, pouring, cooling, and solidification processes in sand casting is essential for producing high-quality castings. Controlling the cooling rate and preventing defects like shrinkage and porosity are key aspects of achieving successful castings. Let’s delve deeper into these processes:
Metal Melting:
- The metal intended for casting is melted in a furnace.
- The furnace temperature is controlled to ensure complete melting and to maintain the desired pouring temperature.
- The composition of the metal is closely monitored to achieve the desired alloy properties.
Pouring:
- Once the metal is molten and at the correct temperature, it is poured into the mold.
- The metal is introduced through a pouring cup, sprue, and gating system, allowing it to flow into the mold cavity.
- Proper gating design and placement help achieve smooth, controlled metal flow and minimize turbulence.
Cooling and Solidification:
- After pouring, the molten metal starts to cool and solidify within the mold.
- The cooling rate influences the microstructure and properties of the casting.
- Slower cooling can result in larger grain size, while rapid cooling can lead to finer grain size.
- The cooling process determines the formation of shrinkage and porosity defects.
Controlling Cooling Rate:
- Proper control of cooling rate is critical for obtaining sound castings.
- Cooling rate can be controlled through the design of the gating and riser system, mold material, and mold preheating.
- Insulating the mold or using chill plates can help regulate cooling rates.
Preventing Shrinkage and Porosity Defects:
- Shrinkage Defects:
- Shrinkage defects occur due to the contraction of the metal as it solidifies.
- Designing proper risers (feeders) that provide additional molten metal to compensate for shrinkage is essential.
- Riser placement and size are determined by the part geometry and material properties.
- Porosity Defects:
- Porosity refers to voids or gas pockets within the casting.
- Proper venting in the mold allows gases to escape during metal pouring.
- Using suitable mold materials, controlling the moisture content of the sand, and degassing the metal before pouring can help reduce porosity.
Solidification Time and Sequence:
- Solidification time varies based on the metal’s composition, pouring temperature, mold material, and part geometry.
- Solidification sequence refers to the order in which different parts of the casting solidify.
- Understanding the solidification sequence helps in designing effective riser systems and minimizing shrinkage defects.
Chilling and Insulating:
- Chills can be strategically placed in the mold to promote rapid cooling in specific areas and prevent defects.
- Insulating the mold or using exothermic additives can help control cooling rates and maintain consistent temperature distribution.
Post-Casting Heat Treatment:
- Some castings may require post-casting heat treatment to relieve stresses, improve mechanical properties, and reduce defects.
- Heat treatment processes can include annealing, normalizing, or quenching and tempering, depending on the material and intended properties.
Controlling the melting, pouring, cooling, and solidification processes in sand casting is essential for producing castings with the desired properties and minimal defects. Proper gating and riser design, understanding the solidification sequence, and using techniques to control cooling rates are key factors in achieving successful sand castings. Regular monitoring, quality control, and adjustments based on experience contribute to consistent casting outcomes.
Chapter 6: The Common Defects in Sand Casting
Sand casting can be prone to various defects that can affect the quality of the final castings. These defects can be minimized or prevented through careful process parameter adjustment and effective quality control measures. Here are some common defects in sand casting and how to address them:
1. Shrinkage Defects:
- Description: Shrinkage defects occur due to the solidification contraction of the metal, resulting in voids or cavities in the casting.
- Prevention/Reduction: Use proper riser design to provide additional molten metal to compensate for shrinkage. Increase riser size and optimize riser placement. Adjust pouring temperature and gating system to control solidification rates.
2. Porosity Defects:
- Description: Porosity defects are caused by trapped gases in the casting, resulting in voids or bubbles.
- Prevention/Reduction: Ensure effective venting in the mold to allow gases to escape. Control sand moisture to reduce steam-related gas. Degas the molten metal before pouring. Modify gating and riser design to minimize turbulence.
3. Inclusions:
- Description: Inclusions are foreign particles (dirt, oxides, etc.) trapped in the casting.
- Prevention/Reduction: Use clean and properly prepared molding materials. Maintain proper furnace and crucible cleanliness. Filter the molten metal before pouring.
4. Sand Scars or Mold Erosion:
- Description: Sand scars occur when molten metal erodes the mold surface.
- Prevention/Reduction: Improve mold material quality. Use coatings or refractory materials to protect mold surfaces from erosion. Optimize gating and pouring system to reduce metal turbulence.
5. Cold Shuts:
- Description: Cold shuts happen when two streams of molten metal fail to fuse together during pouring.
- Prevention/Reduction: Optimize gating system design to ensure smooth metal flow and proper fusion. Adjust pouring temperature and speed.
6. Misruns:
- Description: Misruns occur when the molten metal fails to completely fill the mold cavity.
- Prevention/Reduction: Improve gating and riser design to ensure proper filling. Adjust pouring temperature, speed, and metal flow.
7. Runouts:
- Description: Runouts occur when molten metal leaks out of the mold.
- Prevention/Reduction: Ensure proper mold clamping and alignment. Avoid overfilling the mold.
8. Warpage and Distortion:
- Description: Warpage and distortion result from uneven cooling and solidification.
- Prevention/Reduction: Optimize cooling rates through gating and riser design. Use proper chills and insulating materials. Implement controlled cooling after solidification.
9. Mold Shift or Misalignment:
- Description: Mold shift or misalignment can lead to mismatched mold halves.
- Prevention/Reduction: Ensure proper mold alignment and clamping. Regularly inspect and maintain mold equipment.
Quality Control Measures:
- Regular inspection of patterns, molds, and gating systems for defects and wear.
- Monitoring and control of pouring temperature, metal composition, and moisture content.
- Non-destructive testing (e.g., X-ray, ultrasound) to detect internal defects.
- Post-casting inspections to identify and address defects before further processing.
Minimizing defects in sand casting requires a comprehensive understanding of the casting process, material properties, and proper mold design. Adjusting process parameters and implementing rigorous quality control measures can significantly improve casting quality and reduce defects.
Chapter 7: Post Treatment and Processing of Sand Casting
Post-treatment steps in sand casting are essential to ensure that the castings meet the desired quality, dimensions, and mechanical properties. These steps include cleaning, trimming, and heat treatment. Let’s delve into the purpose, methods, and impact of each of these post-treatment processes:
1. Cleaning:
- Purpose: The cleaning process removes residual sand, scale, oxides, and any other impurities from the surface of the casting.
- Methods: Cleaning methods include shot blasting, sandblasting, tumbling, or mechanical cleaning using tools and brushes.
- Impact: Cleaning enhances the appearance of the casting, prepares the surface for subsequent processing (e.g., machining, painting), and ensures that the casting’s dimensions are accurate.
2. Trimming or Finishing:
- Purpose: Trimming involves removing excess material or gating systems from the casting, bringing it to its final shape and size.
- Methods: Trimming can be done manually using hand tools, saws, or mechanical trimming machines. Precision machining may also be used for critical dimensions.
- Impact: Trimming ensures that the casting conforms to design specifications and eliminates any unwanted features from the gating and riser systems.
3. Heat Treatment:
- Purpose: Heat treatment involves controlled heating and cooling of the casting to achieve specific mechanical and metallurgical properties.
- Methods: Common heat treatment processes include annealing, normalizing, quenching, and tempering, depending on the material and desired properties.
- Impact: Heat treatment enhances the casting’s mechanical properties such as hardness, toughness, and strength. It can also relieve stresses and improve dimensional stability.
4. Surface Treatment:
- Purpose: Surface treatments, such as coating, plating, or painting, are applied to enhance corrosion resistance, improve appearance, and provide specific surface characteristics.
- Methods: Surface treatments can include electroplating, anodizing, powder coating, or applying protective coatings.
- Impact: Surface treatments improve the casting’s aesthetics, protect it from environmental factors, and may also provide functional benefits.
5. Non-Destructive Testing (NDT):
- Purpose: NDT methods are used to detect internal defects in the casting without causing damage.
- Methods: NDT techniques include X-ray, ultrasonic testing, dye penetrant inspection, magnetic particle testing, and more.
- Impact: NDT helps ensure casting integrity by identifying defects such as cracks, inclusions, and porosity that may not be visible on the surface.
6. Machining and Assembly:
- Purpose: Machining involves further shaping the casting using cutting tools to achieve precise dimensions and surface finish. Assembly may involve joining multiple castings together to create complex components.
- Methods: Machining processes include turning, milling, drilling, and grinding. Assembly may involve welding, bolting, or other joining methods.
- Impact: Machining and assembly prepare the casting for its final application and ensure that it fits accurately within the overall product.
Post-treatment steps play a critical role in transforming raw castings into finished, functional components. Each post-treatment process contributes to improving the casting’s quality, appearance, and performance, ensuring that it meets the requirements of the intended application.
Chapter 8: The Application Field of Sand Casting
Sand casting is indeed widely utilized across various industries due to its versatility, cost-effectiveness, and ability to produce complex shapes. Here’s an overview of the specific applications and characteristics of sand casting in different fields:
1. Automotive Manufacturing:
- Applications: Sand casting is used in the automotive industry to produce engine components (cylinder heads, blocks, manifolds), transmission housings, suspension parts, and other structural components.
- Characteristics: Sand casting allows for the production of large and intricate automotive parts. Its flexibility makes it suitable for producing both prototypes and high-volume production.
2. Aerospace Industry:
- Applications: Sand casting is employed in aerospace for manufacturing turbine blades, structural components, and other parts used in aircraft engines and airframes.
- Characteristics: While sand casting may not be as common as precision casting methods in aerospace, it is still utilized for components where shape complexity or lower production volumes are priorities.
3. Mechanical Manufacturing:
- Applications: Sand casting is extensively used in mechanical engineering for producing a wide range of parts, including gears, pulleys, pumps, valves, and brackets.
- Characteristics: Sand casting’s adaptability to different materials and shapes makes it a preferred method for producing various mechanical components.
4. Heavy Machinery and Equipment:
- Applications: Sand casting is employed to create components for heavy machinery, construction equipment, agricultural machinery, and mining equipment.
- Characteristics: The ability to cast large and robust parts makes sand casting suitable for the demands of heavy machinery industries.
5. Pump and Valve Manufacturing:
- Applications: Sand casting is used to manufacture components for pumps, valves, and other fluid-handling equipment.
- Characteristics: Sand casting allows for the production of complex valve bodies, pump casings, and impellers.
6. Marine Industry:
- Applications: Sand casting is utilized in the marine industry to produce ship engine components, propellers, and other structural elements.
- Characteristics: The cost-effectiveness and flexibility of sand casting make it a viable choice for manufacturing large marine parts.
7. Architectural and Decorative Elements:
- Applications: Sand casting is used to create architectural and decorative elements such as ornamental gates, balusters, and building facades.
- Characteristics: Sand casting enables the production of custom-designed and visually appealing components for architectural applications.
In summary, sand casting finds applications in a diverse range of industries due to its adaptability, cost-effectiveness, and suitability for producing both small and large parts. Its ability to handle different materials and accommodate intricate designs makes it a valuable method in various fields, from automotive and aerospace to art and architecture.
Chapter 9: The Impact of Sand Casting on the Environment and Worker Health
Sand casting, like any manufacturing process, can have environmental and health impacts. It’s important to be aware of these impacts and take appropriate measures to minimize them. Here’s an overview of the potential effects and the corresponding environmental protection and safety measures:
Environmental Impacts:
- Energy Consumption: Sand casting involves melting metals at high temperatures, which can lead to significant energy consumption and associated greenhouse gas emissions.
- Air Pollution: Melting and pouring metals can release pollutants into the air, including particulate matter, volatile organic compounds (VOCs), and potentially harmful gases.
- Waste Generation: Sand casting generates waste materials such as used sand, cores, and gating systems, which can contribute to landfill waste if not properly managed.
- Water Usage: Sand preparation and casting processes can require water for cooling and cleaning, leading to water consumption and potential wastewater discharge.
Environmental Protection Measures:
- Energy Efficiency: Implement energy-efficient technologies and practices, such as using energy-efficient furnaces and optimizing heating processes.
- Air Pollution Control: Install effective ventilation systems and pollution control equipment to capture and treat emissions. Use proper ventilation to reduce exposure to harmful fumes.
- Waste Management: Reuse and recycle sand as much as possible. Properly manage waste materials through recycling or disposal at authorized facilities.
- Water Conservation: Implement water-saving techniques and use closed-loop water systems to minimize water consumption and wastewater generation.
Worker Health and Safety:
- Exposure to Dust and Particulates: Sand preparation and casting processes can generate dust and particulates that can pose respiratory hazards to workers.
- Chemical Exposure: Handling binders, coatings, and other chemicals used in sand casting can lead to skin irritation or respiratory issues.
- High Temperatures: Workers involved in pouring and handling molten metal face the risk of burns and heat-related illnesses.
- Mechanical Hazards: Trimming and machining castings can expose workers to risks associated with rotating machinery and cutting tools.
Safety Regulations and Measures:
- Personal Protective Equipment (PPE): Provide workers with appropriate PPE, such as respirators, gloves, protective clothing, and eye protection, to minimize exposure to hazards.
- Engineering Controls: Implement engineering controls like local exhaust ventilation systems to capture and remove airborne contaminants.
- Training and Education: Train workers on proper handling of materials, machinery, and equipment. Educate them about potential hazards and safety protocols.
- Emergency Response: Have clear emergency response plans in place for incidents such as molten metal spills, fires, or chemical exposure.
- Regulatory Compliance: Adhere to relevant safety and environmental regulations, such as those set by occupational safety agencies and environmental protection authorities.
- Regular Monitoring: Conduct regular monitoring of air quality, noise levels, and other potential hazards to ensure a safe working environment.
It’s essential for sand casting facilities to prioritize the health and safety of workers and take proactive steps to minimize environmental impacts. Implementing proper safety measures and environmental protection practices not only safeguard workers’ well-being but also contribute to sustainable manufacturing practices.