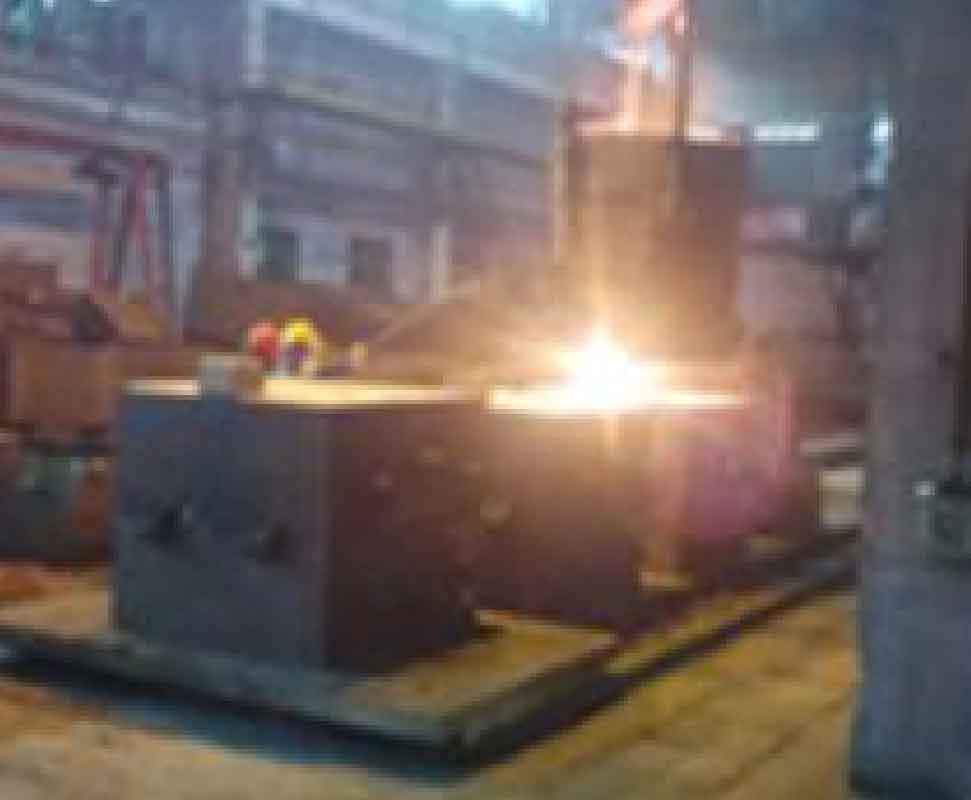
The steam turbine end cover is used to seal the steam in the condensate. It has high requirements on the airtightness and compression resistance of sand castings. It is necessary to carry out the leak detection of the compressor. During the use process, the requirements for the internal quality of the product are very strict.
In order to ensure the quality of sand castings, the solidification process of sand castings was simulated with MAGMA simulation software, and the possible defects were predicted in advance. The sand casting defects such as porosity, slag inclusion and shrinkage porosity were reduced as much as possible. The process was optimized according to the actual situation, and a reasonable sand casting process was designed to meet the product quality requirements.
The current process plan is simulated by MAGMA software for solidification and mold filling. The results show that the slag inclusion and porosity defects of sand castings have been significantly improved by using the small mouth up scheme, which shows that the process design is feasible in theory and can meet the customer’s quality requirements. At present, the sand casting has passed the actual production and subsequent NDT, and the results basically meet the drawing requirements. The current scheme is also applicable to other key products.
For similar sand castings, it is necessary to carry out preliminary planning for slag inclusion and porosity defects in key parts during process design. Reasonable design of riser specification and placement position can effectively collect slag inclusion and porosity defects on the surface of sand castings. For the gating system, try to reduce the entrainment generated in the gating process, which can greatly shorten the trial production cycle of products, save costs and improve production efficiency.