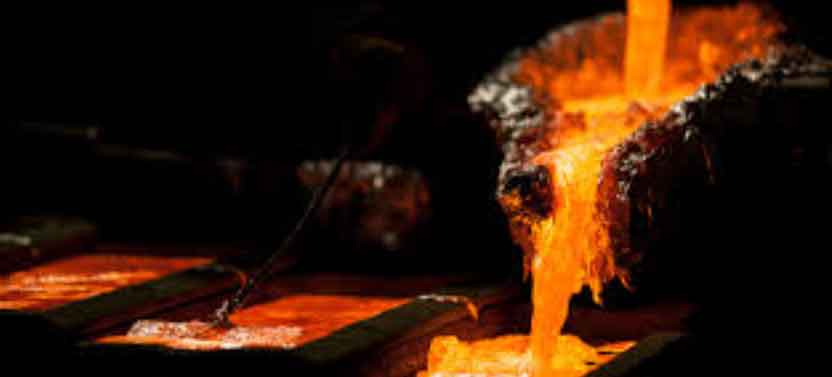
Sand casting is a widely used method for creating metal parts and components. It involves the pouring of molten metal into a mold made of compacted sand. Sand casting is a versatile and cost-effective process that allows for the production of complex shapes and sizes. Let’s explore the techniques involved in sand casting, including molds, cores, and pouring.
- Molds:
- Pattern: Sand casting begins with the creation of a pattern, which is a replica of the final part. Patterns are typically made of wood, metal, or plastic. They are larger than the finished part to account for the shrinkage of the metal during cooling. The pattern includes gating and riser systems to facilitate the flow of molten metal and prevent defects.
- Mold Preparation: The pattern is placed in a box known as a flask, which is divided into two halves: the cope (upper) and drag (lower). The flask is filled with a special molding sand mixture, usually consisting of silica sand mixed with a binder such as clay, resin, or sodium silicate. The sand mixture is tightly packed around the pattern, creating an impression of the part.
- Mold Assembly: Once the sand is packed, the cope and drag are separated, and the pattern is removed, leaving behind a cavity known as the mold. The cope and drag are then reassembled, ensuring proper alignment and the creation of channels called sprues and runners for pouring the molten metal.
- Venting and Chaplets: Vent holes are created in the mold to allow gases to escape during pouring. In the case of heavy sections or parts with internal cavities, chaplets (metal supports) may be used to hold the core in place and prevent it from shifting during pouring.
- Cores:
- Core Preparation: Cores are used to create internal cavities and complex features in the final part. Cores are made from sand mixed with binders and are often produced separately from the mold. They are shaped using core boxes or other techniques.
- Core Placement: Cores are positioned in the mold before closing the cope and drag. They are held in place by the sand and chaplets, if required. The molten metal flows around the cores, creating the desired internal features.
- Pouring:
- Furnace and Melting: The metal for sand casting is typically melted in a furnace, such as a cupola, electric arc furnace, or induction furnace. The metal is heated to its liquid state, ensuring it is free from impurities and at the correct temperature for casting.
- Pouring: Once the metal has reached the desired temperature, it is poured into the mold. The molten metal is usually poured into the sprue, which feeds the metal into the runners and eventually into the cavity of the mold. Proper gating design is crucial to ensure a successful pour and avoid defects such as porosity or insufficient filling.
- Solidification and Cooling: After pouring, the molten metal begins to solidify and cool within the mold. The cooling rate affects the properties of the final part. Once the metal has solidified, the mold is opened, and the casting is removed. The casting may require further cleaning, machining, or finishing operations to achieve the desired specifications.
Sand casting offers numerous advantages, such as low tooling costs, flexibility in design, and the ability to cast a wide range of metals. However, it also has some limitations, including dimensional tolerances, surface finish, and the need for post-casting processes. Advanced techniques and technologies, such as computer simulations and additive manufacturing, are employed to optimize the sand casting process and improve its efficiency and quality.