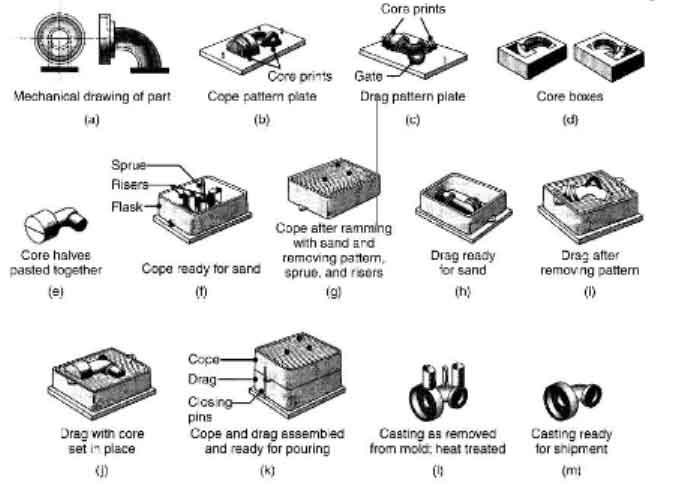
Sand casting is widely recognized for its versatility and flexibility in metal fabrication. It offers numerous advantages that make it a preferred choice for producing a wide range of metal components. Let’s delve into the key aspects that highlight the versatility and flexibility of sand casting:
Wide Range of Metal Alloys:
Sand casting is compatible with a broad spectrum of metal alloys, including ferrous and non-ferrous materials. This includes alloys such as aluminum, bronze, brass, iron, steel, and many others. The ability to work with diverse metal alloys allows manufacturers to select the most suitable material for the specific application, considering factors like strength, corrosion resistance, and cost.
Complex Geometries:
Sand casting enables the production of components with intricate and complex geometries. The molding sand can be easily shaped to create complex features, undercuts, thin walls, and intricate details. This versatility allows for the fabrication of parts with unique shapes, internal cavities, and challenging geometries that may be difficult to achieve using other fabrication methods.
Large and Small Components:
Sand casting is capable of producing both large and small components. It is particularly advantageous for manufacturing large-scale parts, such as engine blocks, gearbox housings, turbine blades, and structural components. At the same time, it can also be utilized for smaller components with intricate details and fine features, such as jewelry, decorative items, or precision mechanical parts.
Prototyping and Low-Volume Production:
Sand casting is well-suited for prototyping and low-volume production. The relatively low tooling costs and shorter lead times compared to other casting methods make it an economical choice for producing prototypes and small production runs. This flexibility allows for iterative design improvements, testing, and validation before committing to mass production.
Design Freedom and Customization:
Sand casting provides design freedom and customization options. Designers can easily modify the pattern or mold to incorporate design changes or cater to specific requirements. This flexibility allows for quick adaptations, design iterations, and customization, making sand casting a suitable choice for industries where product customization or variation is essential.
Reproducibility and Scalability:
Sand casting offers reproducibility and scalability. Once the mold is created, it can be used repeatedly to produce identical castings. This consistency is beneficial for maintaining product quality and meeting production demands. Furthermore, sand casting can be scaled up to accommodate higher production volumes when needed, making it a versatile solution for varying production requirements.
Cost-Effectiveness:
Sand casting is a cost-effective manufacturing process, particularly for medium to large production runs. The low tooling costs and the use of readily available and inexpensive materials, such as sand and pattern materials, contribute to its cost efficiency. Additionally, the ability to reclaim and reuse sand reduces material waste and lowers production costs.
Compatibility with Various Industries:
Sand casting finds applications in various industries, including automotive, aerospace, construction, energy, and more. Its versatility and adaptability make it suitable for producing components used in engine systems, pumps, valves, turbines, heavy machinery, architectural structures, and many other applications.
Sand casting’s versatility and flexibility make it a valuable technique in metal fabrication. Its ability to accommodate a wide range of alloys, produce complex geometries, fabricate both large and small components, and offer customization options make it an ideal choice for diverse manufacturing needs. With advancements in process control, material science, and sustainability practices, sand casting continues to thrive as a versatile and reliable method in the world of metal fabrication.