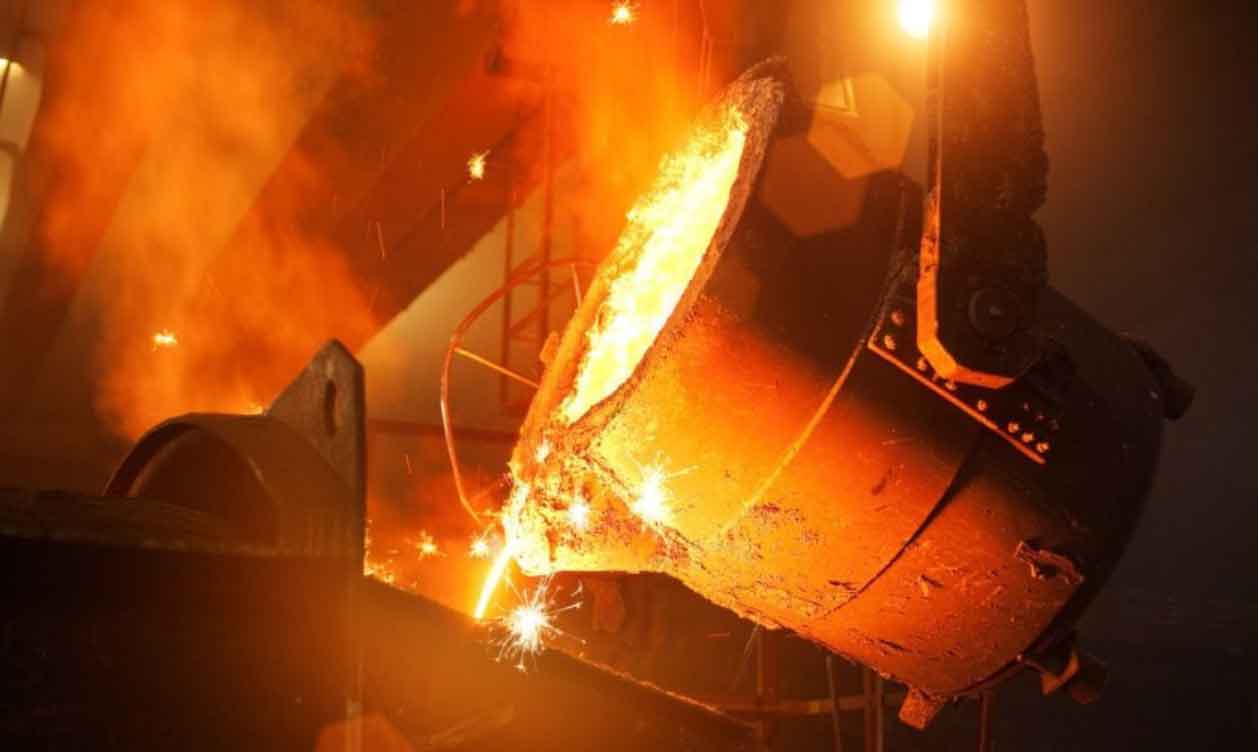
Sand casting and die casting are both popular methods used in the manufacturing industry for producing metal parts. While they share similarities, they differ in various aspects. Let’s compare sand casting and die casting in terms of their process, cost, complexity, and applications.
- Process:
- Sand Casting: In sand casting, a pattern of the desired part is created using wood, metal, or plastic. A mold is then made by packing sand around the pattern. Molten metal is poured into the mold, and after solidification, the mold is broken to retrieve the casting.
- Die Casting: Die casting involves creating a reusable mold, known as a die, which consists of two halves. The mold is precision-machined to the shape of the desired part. Molten metal is injected under high pressure into the die cavity, and once cooled, the die is opened to extract the casting.
- Cost:
- Sand Casting: Sand casting is generally more cost-effective for small-scale or low-volume production. The initial setup cost is lower because sand molds are less expensive to create than dies. However, labor costs for mold-making and post-casting finishing can be higher.
- Die Casting: Die casting is more cost-effective for large-scale or high-volume production due to its higher initial setup cost. Dies are expensive to manufacture, but they can produce a large number of castings with minimal labor and post-processing requirements.
- Complexity:
- Sand Casting: Sand casting is a versatile method that can accommodate complex shapes, intricate details, and large parts. It allows for greater design flexibility and modifications to the mold during production.
- Die Casting: Die casting is suitable for producing parts with precise dimensions and intricate details. It is particularly well-suited for high-volume production of small to medium-sized parts that require consistent quality.
- Surface Finish and Tolerances:
- Sand Casting: Sand castings typically have rougher surface finishes compared to die castings. The tolerances achieved in sand casting are generally lower than in die casting.
- Die Casting: Die castings provide smoother surface finishes and tighter dimensional tolerances due to the high precision of the die mold. Minimal post-processing is usually required.
- Material Selection:
- Sand Casting: Sand casting supports a wide range of materials, including ferrous and non-ferrous metals, such as iron, steel, aluminum, brass, and bronze. It is suitable for casting both low- and high-melting-point metals.
- Die Casting: Die casting is primarily used for non-ferrous metals, such as aluminum, zinc, and magnesium. These metals have lower melting points and better flow properties, making them ideal for the high-pressure injection process.
- Applications:
- Sand Casting: Sand casting finds applications in various industries, such as automotive, aerospace, agriculture, and general manufacturing. It is commonly used for producing large engine blocks, pump housings, and heavy machinery parts.
- Die Casting: Die casting is widely used in industries like automotive, electronics, appliances, and telecommunications. It is suitable for manufacturing complex components, such as automotive engine components, computer parts, and household appliances.
Sand casting is advantageous for low-volume production, larger parts, and greater design flexibility. On the other hand, die casting is more suitable for high-volume production, precise dimensions, and excellent surface finish. The choice between the two methods depends on factors such as production volume, part complexity, cost considerations, and the desired material.