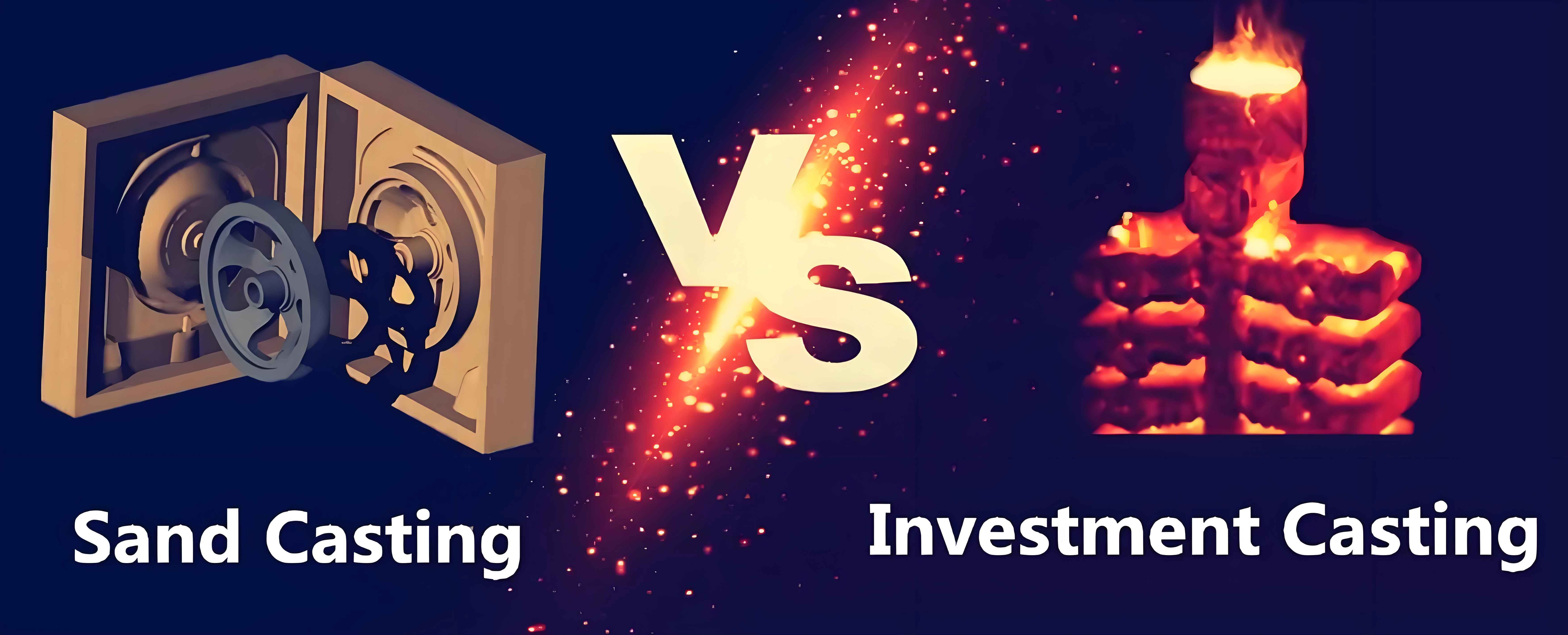
When it comes to heavy machinery production, selecting the appropriate casting method is crucial to ensure the efficiency, durability, and quality of the final products. Two of the most commonly used casting methods are sand casting and investment casting. Each of these methods has its own set of advantages and disadvantages, making them suitable for different applications. This article will explore the differences between sand casting and investment casting, particularly in the context of heavy machinery production.
Sand Casting
Sand casting is one of the oldest and most versatile methods of casting metals. It involves creating a mold from a sand mixture and pouring molten metal into the mold to form the desired shape. This method is particularly popular in heavy machinery production due to its flexibility and cost-effectiveness.
Advantages of Sand Casting
- Cost-Effectiveness
- Sand casting is relatively inexpensive compared to other casting methods, making it ideal for large-scale production.
- Flexibility in Design
- Sand casting allows for a wide range of shapes and sizes, accommodating complex geometries.
- Material Versatility
- Sand casting can be used with almost any metal or alloy, providing a broad range of material choices.
- Large Component Capability
- Sand casting is suitable for producing large and heavy components, which are common in heavy machinery.
Disadvantages of Sand Casting
- Surface Finish
- Sand casting often results in a rough surface finish that may require additional machining.
- Dimensional Accuracy
- Sand casting has lower dimensional accuracy compared to investment casting, which can lead to higher tolerances.
- Defects
- Common casting defects such as porosity, shrinkage, and sand inclusion can occur, affecting the quality of the final product.
Advantages | Disadvantages |
---|---|
Cost-Effectiveness | Rough Surface Finish |
Flexibility in Design | Lower Dimensional Accuracy |
Material Versatility | Potential for Casting Defects |
Large Component Capability |
Investment Casting
Investment casting, also known as lost-wax casting, involves creating a wax model of the desired part, coating it with a ceramic material to form a mold, and then melting the wax away. Molten metal is then poured into the ceramic mold to create the final part. This method is known for its precision and high-quality surface finish.
Advantages of Investment Casting
- Precision and Accuracy
- Investment casting offers superior dimensional accuracy, making it suitable for complex and precise components.
- High-Quality Surface Finish
- The process produces a smooth surface finish, reducing the need for additional machining.
- Design Flexibility
- Investment casting can accommodate intricate designs and fine details that are difficult to achieve with sand casting.
- Reduced Material Waste
- Investment casting produces less material waste compared to sand casting, as the wax models can be reused.
Disadvantages of Investment Casting
- Higher Cost
- Investment casting is generally more expensive due to the complexity of the process and the materials used.
- Size Limitations
- Investment casting is typically used for smaller components and may not be suitable for very large or heavy parts.
- Longer Production Time
- The process involves multiple steps, leading to longer lead times compared to sand casting.
Advantages | Disadvantages |
---|---|
Precision and Accuracy | Higher Cost |
High-Quality Surface Finish | Size Limitations |
Design Flexibility | Longer Production Time |
Reduced Material Waste |
Comparison in Heavy Machinery Production
Material Choice
- Sand Casting: Suitable for a wide range of materials including iron, steel, aluminum, and brass.
- Investment Casting: Commonly used for high-strength alloys and specialty metals.
Component Size
- Sand Casting: Ideal for large and heavy components, making it a preferred choice for heavy machinery parts such as engine blocks, frames, and large gears.
- Investment Casting: Best suited for smaller, precision components like turbine blades, valve parts, and intricate housings.
Production Volume
- Sand Casting: More cost-effective for large production runs of sizable parts.
- Investment Casting: Suitable for smaller batch production of high-precision parts.
Surface Finish and Tolerances
- Sand Casting: Requires additional machining to achieve a smooth surface and tight tolerances.
- Investment Casting: Delivers a superior surface finish and high dimensional accuracy, often reducing the need for secondary operations.
Conclusion
In the production of heavy machinery, the choice between sand casting and investment casting depends on several factors including the size and complexity of the component, the required material properties, production volume, and budget considerations. Sand casting is an excellent choice for large, heavy components with complex shapes and is cost-effective for high-volume production. Investment casting, on the other hand, is ideal for smaller, precision components that require high dimensional accuracy and superior surface finish. By understanding the strengths and limitations of each casting method, manufacturers can make informed decisions to optimize their production processes and achieve the desired quality and performance in their heavy machinery components.