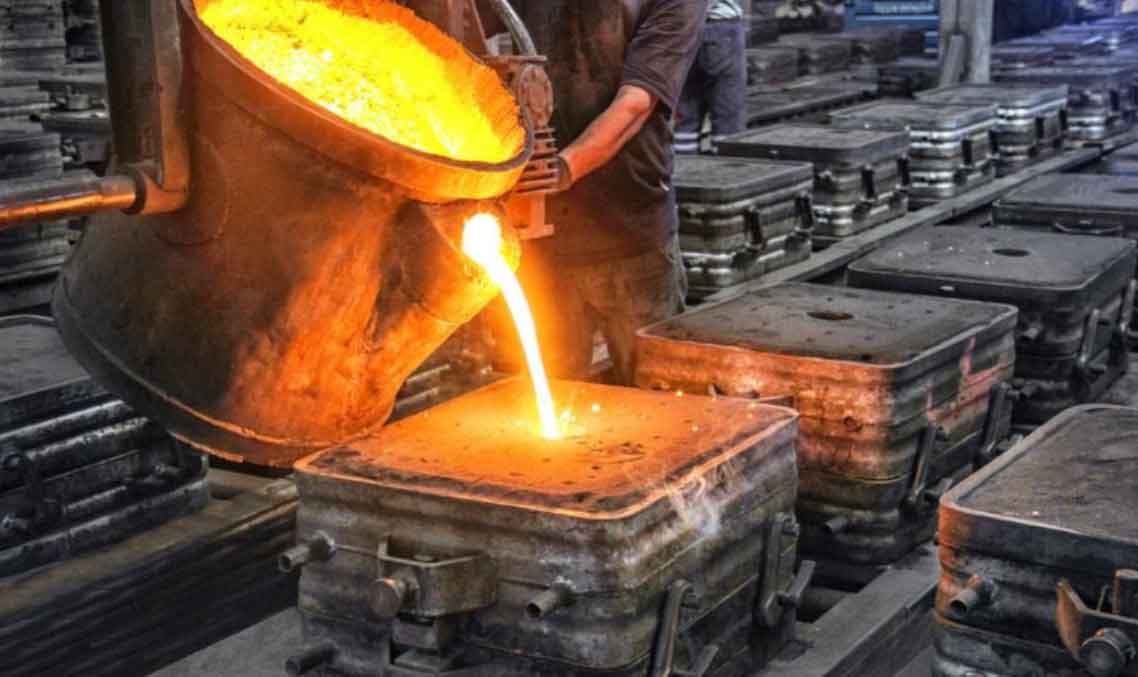
When choosing between sand casting and other casting methods, it’s essential to consider the specific requirements of your project and the advantages offered by each process. Here’s a comparison of sand casting with other common casting methods to help you determine when to choose a sand casting manufacturer:
1. Sand Casting:
- Advantages:
- Versatility: Sand casting can accommodate a wide range of sizes and shapes, making it suitable for both small and large components.
- Lower Tooling Costs: Sand casting typically involves lower initial tooling costs compared to other casting methods, making it cost-effective for low to medium production volumes.
- Complex Geometry: Sand casting is capable of producing components with intricate shapes and complex internal features.
- Suitable for Various Materials: Sand casting supports a broad range of materials, including ferrous and non-ferrous alloys.
- When to Choose Sand Casting:
- For medium to large-sized components with complex geometries.
- When cost-effectiveness and lower tooling costs are crucial for low to medium production volumes.
- When the casting design allows for the use of sand molds.
2. Investment Casting (Lost-Wax Casting):
- Advantages:
- High Dimensional Accuracy: Investment casting produces castings with excellent dimensional accuracy and smooth surface finish.
- Fine Details: It is suitable for creating intricate and detailed parts with close tolerances.
- Versatility in Material Selection: Investment casting can be used with a wide variety of materials, including stainless steel, aluminum, and superalloys.
- When to Choose Investment Casting:
- For components that require high dimensional accuracy, fine details, and a smooth surface finish.
- When casting small to medium-sized parts with complex shapes.
3. Die Casting:
- Advantages:
- High Production Rates: Die casting is ideal for high-volume production due to its rapid cycle times.
- Good Surface Finish: Die castings have a smooth surface finish.
- Consistency: Die casting offers consistent part-to-part quality.
- When to Choose Die Casting:
- For high-volume production of small to medium-sized components with consistent geometry.
- When faster production rates are essential.
4. Permanent Mold Casting:
- Advantages:
- Reusability: Permanent molds can be used repeatedly, reducing the need for constant mold remaking.
- Improved Surface Finish: Permanent mold castings often have better surface finish compared to sand castings.
- When to Choose Permanent Mold Casting:
- For medium to high-volume production of components with fine surface finish requirements.
- When the cost of permanent tooling is justified by the production volume.
Choose a sand casting manufacturer when you require a cost-effective casting method for medium to large-sized components with complex geometries. Sand casting is highly versatile and suitable for a wide range of materials, making it an excellent choice for projects that do not require extremely high dimensional accuracy and surface finish. However, for applications that demand high precision and intricate details, investment casting or other specialized casting methods may be more suitable. Consider the specific requirements of your project, production volume, and desired part characteristics to make an informed decision.