Introduction
Sand casting is a complex process that involves various principles to achieve successful and high-quality castings. Here are the key principles of sand casting:
1. Pattern Design and Preparation:
The pattern, which represents the final casting’s shape, must be designed carefully to account for factors like shrinkage and draft angles. It should also be constructed for easy removal from the mold without damaging the mold cavity.
2. Mold Making:
The mold is created by packing special molding sand around the pattern. The mold must be properly designed to allow for proper filling, cooling, and easy removal of the casting. The cope and drag halves of the mold should align accurately.
3. Gating and Risering:
The gating system (gates, runners, and sprue) is designed to ensure a smooth and controlled flow of molten metal into the mold. The risers provide extra metal to compensate for shrinkage during solidification and prevent porosity.
4. Metal Pouring:
The molten metal is poured into the mold through the sprue, displacing air and filling the mold cavity. The pouring process must be controlled to prevent turbulence and ensure uniform filling.
5. Solidification and Cooling:
The molten metal solidifies inside the mold cavity. The cooling process must be controlled to prevent defects like shrinkage, distortion, and cracks. Proper risering helps ensure adequate metal supply during solidification.
6. Mold Removal:
After the metal has solidified, the mold is broken apart to reveal the casting. Careful removal of the mold is essential to prevent damage to the casting or the mold cavity.
7. Cleaning and Finishing:
The casting is cleaned to remove excess sand, gating components, and any other residues. Surface finishes and minor repairs are performed if necessary.
8. Inspection and Testing:
The casting undergoes visual inspection, dimensional measurement, and various testing methods (like dye penetrant, radiographic, or ultrasonic testing) to ensure quality and detect defects.
9. Post-Casting Processes (Optional):
Additional processes such as heat treatment, machining, coating, and painting may be applied to achieve desired properties and appearance.
10. Environmental Considerations:
Sustainability and environmental protection are increasingly important. Using eco-friendly sand, implementing energy-efficient melting methods, and proper waste management contribute to responsible casting practices.
11. Process Control and Quality Assurance:
Consistent and controlled process parameters, from sand composition to pouring temperature, are crucial to achieving repeatable and high-quality castings. Regular quality checks and adjustments are essential.
12. Continuous Improvement:
Regularly analyzing the casting process, identifying areas for improvement, and implementing best practices help enhance casting quality, efficiency, and sustainability.
13. Safety:
Safety measures are essential to protect workers from the hazards of working with molten metal, high temperatures, and heavy equipment.
Applying these principles ensures that the sand casting process yields castings that meet specifications, exhibit desired mechanical properties, and maintain consistent quality.
Chapter 1: The Complete Process Flow of Sand Casting
Here’s a comprehensive overview of the complete sand casting process, including each step from mold preparation to post-treatment:
1. Pattern Design and Preparation:
- Design a pattern to replicate the final casting’s shape, considering shrinkage and draft angles.
- Construct the pattern using wood, plastic, or metal, ensuring it’s easily removable from the mold.
2. Mold Preparation:
- Place the pattern in the bottom half of the mold (drag).
- Close the mold with the top half (cope).
- Compact molding sand around the pattern to create the mold cavity.
3. Core Production:
- If internal features are required, produce sand cores to create voids within the casting.
- Core boxes are used to create the desired core shapes.
4. Gating and Risering:
- Design gating system (sprue, runners, and gates) to control metal flow and prevent turbulence.
- Design risers (feeders) to provide extra molten metal to compensate for shrinkage.
5. Mold Assembly:
- Place cores in the mold if needed, ensuring proper positioning.
- Assemble the cope and drag halves of the mold, ensuring proper alignment.
6. Metal Melting:
- Charge the furnace with gray cast iron or other chosen metal.
- Melt the metal using fuel or electricity until it reaches the required pouring temperature.
7. Pouring:
- Open the mold and position it for pouring.
- Pour the molten metal into the sprue, allowing it to flow into the mold cavity.
8. Solidification and Cooling:
- The molten metal solidifies as it cools within the mold cavity.
- Proper gating and risering help ensure uniform solidification and minimize defects.
9. Mold Cooling:
- Allow the casting to cool and solidify within the mold.
- Cooling rates affect microstructure and mechanical properties.
10. Mold Removal (Shakeout): – Open the mold and remove the casting after it has solidified. – Shake or vibrate the mold to release sand and debris from the casting.
11. Cleaning and Finishing:
- Remove excess sand, gating components, and any other residues.
- Use tools, brushes, and sometimes sandblasting to clean the casting’s surface.
12. Inspection and Testing:
- Visually inspect the casting for defects like cracks, porosity, and surface irregularities.
- Perform dimensional measurements to ensure accuracy.
- Conduct non-destructive testing (NDT) methods like X-ray, ultrasonic, or dye penetrant testing.
13. Post-Treatment (Optional):
- Heat treatment: Modify material properties through annealing, quenching, or tempering.
- Machining: Remove excess material and achieve precise dimensions.
- Coating and painting: Apply protective coatings for corrosion resistance and aesthetics.
14. Final Inspection and Quality Control:
- Verify that the casting meets all specifications and quality standards.
- Ensure that post-treatment processes were successful if applied.
15. Packaging and Shipping:
- Properly package the castings to prevent damage during transport.
- Arrange for shipping to the designated destination.
Throughout the process, safety measures must be followed to ensure the well-being of workers dealing with molten metal, high temperatures, and heavy equipment. The sand casting process demands careful execution at each stage to achieve accurate and high-quality castings that meet the intended design and performance requirements.
Chapter 2: Selection of Metal Materials for Sand Casting
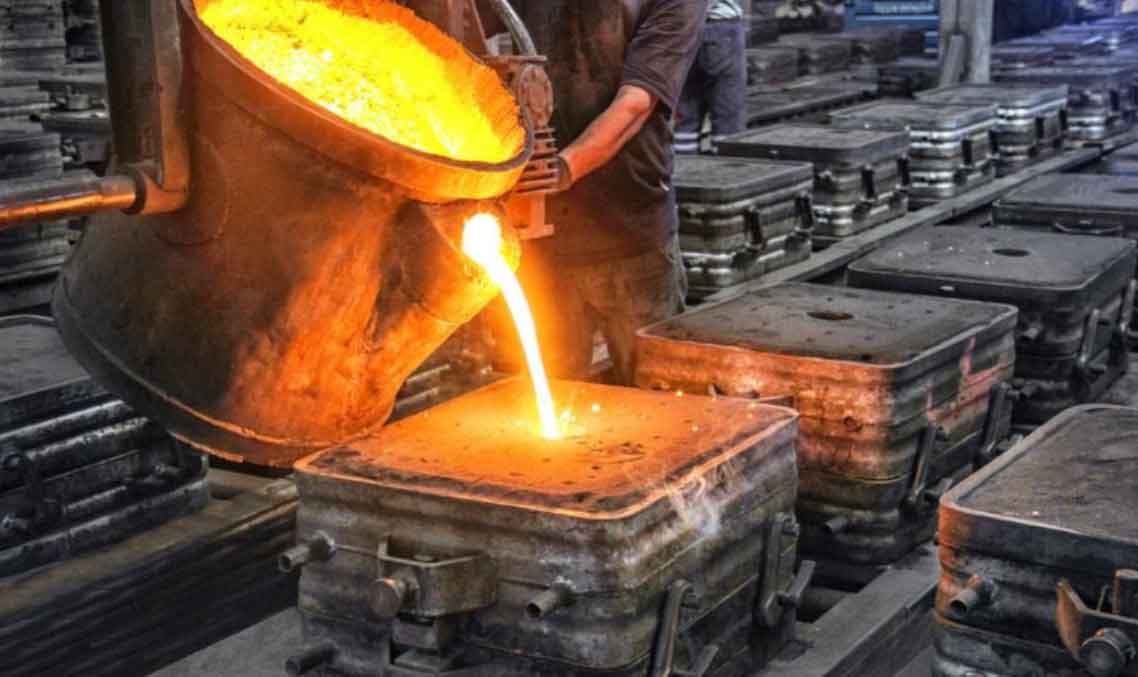
The selection of metal materials for sand casting is a crucial step in ensuring the successful production of castings with the desired properties. Different metals offer varying characteristics in terms of strength, ductility, corrosion resistance, heat resistance, and more. Here are some common factors to consider when selecting metal materials for sand casting:
- Casting Requirements:
- Determine the specific requirements of the casting, such as mechanical properties, wear resistance, heat resistance, and corrosion resistance.
- Application:
- Consider the intended use of the casting, whether it’s for automotive parts, machinery components, structural elements, or other applications.
- Material Properties:
- Evaluate the required tensile strength, hardness, toughness, and other mechanical properties based on the application’s demands.
- Corrosion Resistance:
- Choose a material that can withstand the environmental conditions and potential exposure to corrosive agents.
- Heat Resistance:
- Consider the casting’s operating temperature and whether the material can retain its properties under those conditions.
- Machinability:
- Some materials are easier to machine than others. Consider the required level of machining and how the material responds to cutting tools.
- Cost Considerations:
- Balance the desired material properties with cost constraints, as certain materials might be more expensive than others.
- Availability:
- Ensure that the chosen material is readily available from suppliers.
- Compatibility with Sand Casting Process:
- Consider how well the material can be cast using the sand casting process. Certain materials may have specific requirements for gating, risering, and cooling.
Common metals used in sand casting include:
1. Gray Cast Iron (GCI):
- Excellent damping capacity, good wear resistance, and high thermal conductivity.
- Widely used for automotive engine components, machine tool bases, and more.
2. Ductile Cast Iron (SG Iron or Nodular Iron):
- Offers higher tensile strength, toughness, and ductility compared to gray cast iron.
- Suitable for applications requiring greater mechanical strength, such as heavy machinery components.
3. Carbon Steel:
- Offers a range of mechanical properties based on carbon content.
- Used for a variety of applications, including machinery parts, automotive components, and structural elements.
4. Aluminum Alloys:
- Lightweight, good corrosion resistance, and excellent heat conductivity.
- Suitable for parts in automotive, aerospace, and marine industries.
5. Bronze and Brass Alloys:
- Good corrosion resistance, aesthetics, and machinability.
- Used for decorative elements, marine components, and architectural applications.
6. Copper Alloys:
- Good electrical and thermal conductivity, along with corrosion resistance.
- Used in electrical components, plumbing fixtures, and more.
Choosing the right material involves a careful balance between performance requirements, manufacturing capabilities, and economic considerations. Collaborating with materials experts and considering the specific needs of the casting will help ensure a successful material selection process.
Chapter 3: Selection of Sand Mold and Core Materials for Sand Casting
Selecting the appropriate sand mold and core materials is crucial in the sand casting process, as they directly impact the quality of the final casting. The properties of the sand used for molds and cores influence factors like mold strength, surface finish, dimensional accuracy, and the overall casting quality. Here are considerations for selecting sand mold and core materials:
1. Sand Characteristics:
- Refractoriness: The sand must be able to withstand the high temperatures of molten metal without deforming or breaking down.
- Permeability: Adequate permeability ensures gases can escape during pouring and solidification, preventing defects.
- Collapsibility: The sand should be collapsible to allow easy removal of the casting.
2. Type of Casting:
- Different castings have varying requirements. For intricate or detailed castings, finer sands might be preferred.
3. Casting Material:
- The casting material’s temperature and reactivity with the sand affect sand selection.
4. Surface Finish:
- The sand’s grain size and quality impact the surface finish of the casting.
5. Ventilation and Gas Escape:
- The sand should have appropriate permeability to allow gases to escape without causing defects.
6. Binder Compatibility:
- If binders or additives are used, ensure they’re compatible with the chosen sand material.
7. Recyclability:
- Reusability of sand can reduce waste and costs. Consider whether the sand can be reclaimed efficiently.
8. Environmental Impact:
- Choose environmentally friendly sand options that minimize ecological impact.
9. Core Strength:
- Core sand should possess adequate strength to maintain its shape during handling and pouring.
10. Dimensional Accuracy: – The sand should allow for precise replication of patterns and cores.
Common Sand Mold and Core Materials:
1. Green Sand:
- A mixture of sand, clay, water, and additives.
- Economical, versatile, and used for a wide range of applications.
- Offers good refractoriness and permeability.
2. Silica Sand:
- High-quality sand with excellent refractoriness and permeability.
- Used for producing high-quality castings and intricate details.
3. Resin-Bonded Sand:
- Sand mixed with a resin binder to enhance strength and reduce collapsibility.
- Used for producing precise and complex castings.
4. Shell Molding Sand:
- Pre-coated sand with a resin binder to create a shell-like mold.
- Offers good surface finish and dimensional accuracy.
5. Ceramic Sand (Cerabeads):
- Synthetic sand with consistent properties for high-quality castings.
- Provides good surface finish and low thermal expansion.
6. Chromite Sand:
- Contains chromite as a refractory material for high-temperature applications.
- Used in molds and cores for steel and iron castings.
Selecting the right sand mold and core materials involves evaluating the specific requirements of the casting, the casting process, and the desired casting quality. Collaborating with materials experts and performing tests can aid in determining the best sand materials for your specific casting needs.
Chapter 4: The Preparation Process of Sand Casting Molds
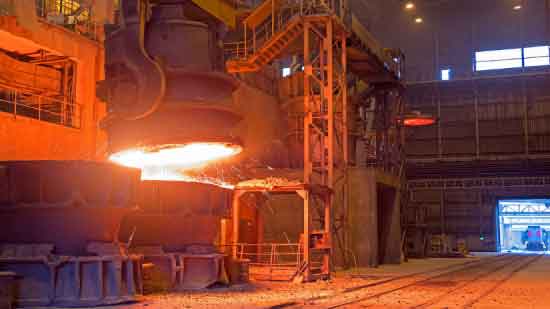
The preparation process of sand casting molds involves several crucial steps to ensure the successful creation of molds that accurately replicate the desired casting shape. Here’s a breakdown of the key steps:
1. Pattern or Model Production:
- Create a pattern or model that represents the final shape of the casting.
- Patterns can be made from wood, metal, or plastic, depending on the complexity and size of the casting.
2. Cavity Design:
- Based on the pattern, design the cavity or mold cavity that will form the negative space of the final casting.
- Consider factors such as draft angles, parting lines, and gating system placement.
3. Model Coating:
- Apply a parting compound or mold release agent to the pattern’s surface. This prevents the sand mold from sticking to the pattern and aids in pattern removal.
- The parting compound can be a thin layer of graphite, talc, or other release agents.
4. Mold Box Preparation:
- Place the pattern in a mold box, also known as a flask.
- The flask consists of two halves, the drag (bottom) and cope (top), which separate to create the mold cavity.
5. Sand Preparation:
- Prepare molding sand with the right properties, including refractoriness, permeability, and cohesiveness.
- Proper sand preparation ensures the mold holds its shape and allows for smooth metal flow during pouring.
6. Ramming:
- Compact the sand around the pattern in the drag and cope halves of the flask.
- Use a ramming tool to ensure proper compaction and density.
7. Pattern Alignment and Packing:
- Ensure the pattern is properly aligned within the mold box to achieve accurate casting dimensions.
- Add additional sand and compact it around the pattern to create a uniform mold cavity.
8. Mold Assembly:
- Separate the cope and drag halves of the flask and remove the pattern.
- The cope and drag are ready to be assembled, forming the complete mold cavity.
9. Core Placement (If Needed):
- If internal features are required in the casting, insert sand cores into the mold cavity to create voids.
- Cores are placed in the mold before assembly or added later through core prints.
10. Gating and Venting: – Design and create gating system components like runners, gates, and risers to facilitate the molten metal’s flow into the mold and to allow gases to escape. – Proper gating and venting prevent defects like porosity and incomplete filling.
11. Closing and Securing the Mold: – Close the cope and drag halves of the mold box, ensuring proper alignment and contact. – Use pins, clamps, or other mechanisms to secure the mold halves.
12. Mold Release and Pouring: – Open the mold, removing the gating components. – Prepare the mold for pouring by applying a coating or facing material to enhance the casting’s surface finish.
13. Metal Pouring: – Position the mold for pouring and carefully pour the molten metal into the sprue or gating system. – Ensure a controlled pour to prevent turbulence and ensure even filling.
Each of these steps requires attention to detail and precision to create molds that result in accurate, high-quality castings. Proper execution of the mold preparation process ensures that the final castings meet the intended design and quality standards.
Chapter 5: Production Method and Material Selection of Sand Casting Core
Sand casting cores play a crucial role in creating complex internal features within castings. Cores are used to form voids, recesses, holes, and other intricate shapes that cannot be achieved solely using the pattern. Here’s an overview of the production method and material selection for sand casting cores, along with their role in forming the internal structure of parts:
Production Method of Sand Casting Cores:
- Core Box Preparation:
- A core box is used to shape the sand into the desired core geometry.
- The core box can be made of wood, metal, or other materials, and it’s designed to create the negative shape of the core.
- Core Sand Preparation:
- Special core sand is used to ensure the core maintains its shape during handling and pouring.
- The core sand is mixed with a binder or other additives to enhance its strength and cohesion.
- Core Assembly and Packing:
- The core sand is packed into the core box, ensuring proper compaction to achieve the desired density and surface finish.
- Cores may consist of multiple parts that need to be assembled accurately in the mold.
- Core Removal:
- After the mold has been filled and the metal has solidified, the mold is opened, and the sand cores are removed.
- Cores must be designed to be collapsible or breakable for easy removal without damaging the casting.
Material Selection for Sand Casting Cores:
- Core Sand:
- Core sand is typically a mixture of sand, binder, and additives.
- The binder can be organic (like resin) or inorganic (like sodium silicate).
- Additives can enhance properties such as strength, collapsibility, and heat resistance.
- Core Binders:
- Organic binders provide good strength and collapsibility.
- Inorganic binders like sodium silicate offer high-temperature resistance.
- Additives:
- Additives such as coal dust, cereal, or sawdust can be used to enhance collapsibility and permeability.
Role of Cores in Forming Internal Structures:
- Creating Internal Cavities:
- Cores are used to create internal voids, recesses, and cavities within castings.
- These internal features could be complex shapes that cannot be achieved using the pattern alone.
- Forming Passageways and Holes:
- Cores are used to form passageways for gases, fluids, or other materials.
- These can include holes for cooling channels, fluid passages, and more.
- Aiding in Assembly:
- Cores can include features that help align and assemble multiple castings together.
- Preserving Tolerances:
- Cores play a role in maintaining dimensional accuracy and tolerances of internal features.
- Creating Undercuts and Projections:
- Cores can create undercuts and projections that add complexity to the casting’s geometry.
- Managing Wall Thickness:
- Cores help control wall thickness and maintain uniformity in casting dimensions.
Sand casting cores enable the creation of intricate internal structures, enhancing the functionality and design possibilities of castings. Careful core design, material selection, and production techniques ensure that cores maintain their shape during casting, contribute to accurate casting dimensions, and allow for successful removal after solidification.
Chapter 6: The Process of Metal Melting in Sand Casting
The metal melting and pouring process in sand casting is a critical step that requires careful attention to ensure successful castings. Here’s an overview of the process, precautions during pouring, and the interaction between the molten metal and the sand mold:
Metal Melting and Pouring Process:
- Furnace Preparation:
- Charge the furnace with the chosen metal material (e.g., gray cast iron, aluminum, etc.).
- Preheat the furnace to the desired pouring temperature, which depends on the metal’s melting point.
- Metal Melting:
- As the metal heats up, it gradually melts into a molten state.
- Depending on the furnace type, fuel source, and metal properties, the melting process can take varying amounts of time.
- Temperature Control:
- Monitor the metal’s temperature closely using temperature gauges or pyrometers to ensure it reaches the appropriate pouring temperature.
- Degassing and Alloying (if needed):
- Degassing techniques may be used to remove gases from the molten metal.
- Alloying elements can be added to achieve specific material properties.
- Pouring Ladle Preparation:
- Transfer the molten metal to a pouring ladle, which will be used for controlled pouring into the mold.
Precautions During Pouring:
- Safety Measures:
- Ensure that all safety equipment, such as protective clothing, helmets, gloves, and face shields, is worn by workers involved in the pouring process.
- Pouring Speed and Control:
- Control the pouring speed to prevent turbulence, splashing, and metal erosion of the mold surfaces.
- A controlled pour ensures even filling and minimizes defects like gas entrapment.
- Pouring Height:
- Pour the metal from a sufficient height to promote a smooth flow and prevent the formation of oxide films on the metal’s surface.
- Pouring Sequence:
- Follow a sequence when pouring multiple molds to ensure uniform metal flow and consistent cooling times.
- Gating System:
- Ensure the gating system (sprue, runners, and gates) is designed to facilitate smooth metal flow without causing turbulence or blockages.
Interaction Between Metal and Sand Mold:
- Thermal Shock:
- The molten metal’s high temperature can cause thermal shock to the sand mold’s inner surfaces. Proper gating design and preheating the mold can mitigate this.
- Heat Transfer:
- The metal rapidly transfers heat to the mold, causing the sand to heat up and potentially change its properties. This can affect surface finish and mold erosion.
- Gas Evolution:
- The heat can cause gases to evolve from the mold and the core, which need proper venting to prevent defects like porosity.
- Sand Expansion:
- The heat can cause sand expansion, which could lead to mold distortion or cracking. Adequate mold strength and proper support are essential.
- Sand-Metal Reaction:
- Some metals may react with certain components in the sand, like clay binders, potentially affecting casting quality.
Understanding the interaction between the molten metal and the sand mold is crucial for producing high-quality castings. Proper precautions during pouring and well-designed gating systems contribute to successful castings with minimal defects and optimal properties.
Chapter 7: Cooling Process of Sand Casting
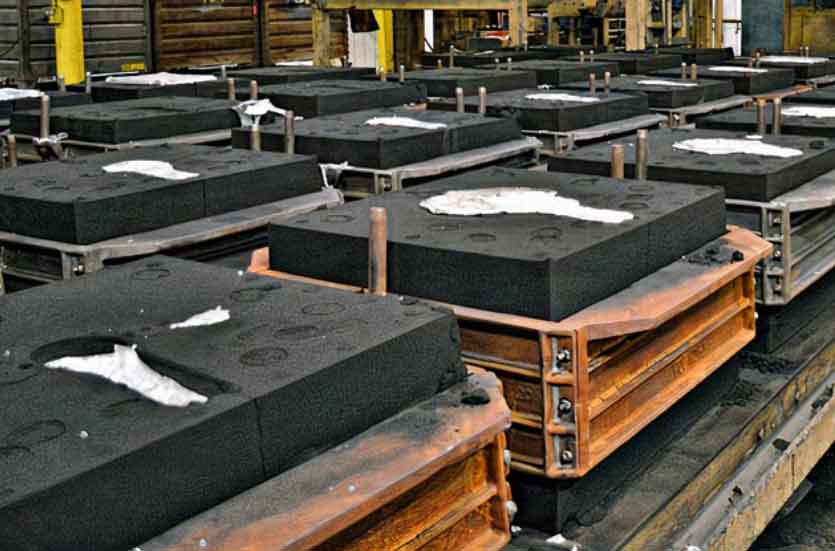
The cooling process in sand casting refers to the gradual solidification of the molten metal inside the mold after it has been poured. This process is critical as it influences the microstructure, mechanical properties, and overall quality of the casting. The cooling rate during solidification plays a significant role in determining casting performance. Additionally, the demolding methods and techniques are essential for safely and effectively removing the casting from the mold.
Cooling Process and Impact on Casting:
- Cooling Rate:
- The cooling rate affects the formation of the casting’s microstructure, which in turn influences its mechanical properties.
- Faster cooling rates can lead to finer grains and higher strength, while slower cooling rates may result in coarser grains and improved ductility.
- Shrinkage:
- As the molten metal solidifies, it undergoes volumetric contraction (shrinkage).
- Proper riser design and gating system ensure that additional molten metal is available to compensate for this shrinkage, preventing defects like shrinkage cavities.
- Solidification Front:
- The solidification front moves inward from the mold surfaces toward the center of the casting.
- Proper gating and risering help ensure a uniform solidification front and prevent the formation of shrinkage-related defects.
- Microstructure and Properties:
- The cooling rate influences the size, shape, and distribution of grains within the casting’s microstructure.
- Fine-grained microstructures generally exhibit improved mechanical properties, including strength and hardness.
- Casting Integrity:
- Proper cooling and solidification minimize the formation of defects like porosity, shrinkage cavities, and cracks.
Demolding Methods and Techniques:
- Vibration and Knockout:
- Mild vibrations or tapping can help loosen the sand around the casting, aiding in its removal from the mold.
- Mechanical knockout equipment can also be used to dislodge the casting.
- Use of Parting Compound:
- Applying a parting compound or mold release agent to the pattern can ease the removal of the casting from the mold.
- Sand Ejection Pins:
- In some cases, sand ejection pins can be installed in the mold to help push the casting out during demolding.
- Hydraulic or Pneumatic Methods:
- Hydraulic or pneumatic devices can exert controlled pressure to eject the casting from the mold.
- Heating the Mold:
- In certain situations, preheating the mold slightly can help expand the mold and facilitate demolding.
- Casting Design Considerations:
- Draft angles and proper core design can aid in easy and safe demolding.
- Cautious Handling:
- Careful handling during demolding is crucial to avoid damaging the casting or the mold cavity.
The cooling process and demolding techniques are interconnected, as the solidification of the metal affects the mechanical properties and the ease of casting removal. Both aspects require a deep understanding of the casting process, material behavior, and proper design and operational considerations to ensure successful castings with minimal defects and efficient demolding.
Chapter 8: Subsequent Process of Sand Casting Demolding
After the demolding process in sand casting, there are several subsequent processes that may be required to achieve the desired final properties, dimensions, and surface finish of the castings. These processes vary based on the specific casting and application. Here are some common subsequent processes:
1. Deburring and Deflashing:
- Remove excess metal, sharp edges, and burrs created during the casting process.
- Deburring enhances safety and improves the casting’s appearance.
2. Trimming and Machining:
- Machining processes such as milling, turning, drilling, and grinding may be performed to achieve accurate dimensions and precise features.
- Trimming ensures that the casting meets the required tolerances.
3. Heat Treatment:
- Heat treatment processes like annealing, quenching, tempering, and normalization can be applied to improve mechanical properties.
- Heat treatment enhances hardness, strength, and toughness, as well as relieves residual stresses.
4. Surface Treatment:
- Surface treatment processes are used to improve the casting’s appearance, corrosion resistance, and wear resistance.
- Common surface treatments include painting, plating, anodizing, powder coating, and shot blasting.
5. Shot Peening:
- Shot peening involves bombarding the casting’s surface with small metal or ceramic particles to induce compressive stresses and improve fatigue resistance.
6. Inspection and Quality Control:
- Perform detailed inspections using non-destructive testing (NDT) methods such as X-ray, ultrasonic testing, and dye penetrant testing.
- Dimensional measurement and visual inspection ensure the casting meets quality standards.
7. Assembly and Joining:
- If the casting is part of a larger assembly, it may require joining or welding to other components.
- Assembly processes ensure that the casting functions as intended within the larger system.
8. Painting and Coating:
- Apply protective coatings, paints, or sealants to enhance corrosion resistance and improve aesthetics.
- Coatings can provide additional surface protection in harsh environments.
9. Polishing and Finishing:
- For decorative castings or applications requiring a smooth surface finish, polishing and buffing may be employed.
10. Non-Destructive Testing (NDT): – Additional NDT methods like radiographic testing and ultrasonic testing can be performed to ensure the integrity of the casting.
11. Final Inspection and Documentation: – Perform a final inspection to ensure all subsequent processes have been correctly carried out and that the casting meets specifications. – Document the results of inspections and treatments for quality control and traceability.
Each subsequent process contributes to refining the casting’s properties and appearance according to the intended use. Proper execution of these processes ensures that the castings meet performance requirements, safety standards, and aesthetic expectations.
Chapter 9: The Quality Control and Inspection of Sand Casting
Ensuring the quality of sand castings involves a combination of various testing and analysis methods. Here’s how metallographic analysis, dimensional measurement, non-destructive testing (NDT), and other means can be used to ensure casting quality:
1. Metallographic Analysis:
- Metallography involves examining the microstructure of the casting under a microscope. This analysis provides insights into the casting’s grain size, phase distribution, and potential defects.
- Sample preparation involves cutting, grinding, polishing, and etching the casting to reveal its microstructure.
- Metallographic analysis helps identify issues like improper cooling, incomplete solidification, and segregation.
2. Dimensional Measurement:
- Precise dimensional measurement ensures that the casting’s dimensions, tolerances, and features meet design specifications.
- Coordinate measuring machines (CMMs), calipers, micrometers, and other metrology tools are used for dimensional checks.
- Inspection reports compare measurements against CAD data to identify discrepancies.
3. Non-Destructive Testing (NDT):
- NDT methods evaluate casting integrity without damaging the casting itself.
- Common NDT methods include:
- Ultrasonic Testing (UT): Detects internal defects using sound waves.
- X-ray and Radiographic Testing (RT): Reveals internal voids and discontinuities.
- Magnetic Particle Testing (MT): Detects surface and near-surface defects using magnetic fields.
- Dye Penetrant Testing (PT): Identifies surface cracks and defects by applying a dye penetrant and developer.
4. Visual Inspection:
- Thorough visual inspection detects surface defects, such as cracks, porosity, and irregularities.
- Skilled inspectors examine castings using proper lighting, magnification, and knowledge of common defects.
5. Hardness Testing:
- Hardness testing measures the casting’s surface hardness, which can provide insights into material properties and potential variations.
- Tests like Rockwell or Brinell hardness testing assess the casting’s hardness characteristics.
6. Chemical Composition Analysis:
- Chemical analysis confirms that the casting’s alloy composition matches the desired specifications.
- Spectroscopy or chemical analysis equipment identifies element concentrations.
7. Pressure Testing:
- Pressure testing checks for leaks or defects in sealed castings, such as engine blocks or pressure vessels.
- Castings are pressurized and monitored for pressure drops that indicate leaks.
8. Mechanical Testing:
- Tensile, impact, and other mechanical tests evaluate the casting’s strength, ductility, and impact resistance.
- Mechanical tests help ensure that the casting meets performance requirements.
9. Ultrasonic Shearography:
- This advanced NDT method identifies internal defects by analyzing surface deformations caused by ultrasonic waves.
10. Resonance Testing:
- Utilizes vibrations to detect internal defects and inconsistencies in the casting’s structure.
Combining these methods provides a comprehensive approach to quality assurance in sand casting. Inspections are performed at various stages of the process, from raw materials to finished castings. Thorough quality control helps identify defects early, minimize scrap rates, and ensure that the final products meet the intended specifications and performance criteria.
Chapter 10: The Widespread Application of Sand Casting

Sand casting is a versatile and widely used casting process that finds application in various industries. Some of the fields where sand casting is commonly utilized include:
- Automotive Manufacturing:
- Engine blocks, cylinder heads, transmission housings, and other automotive components are often produced using sand casting.
- Sand casting’s flexibility allows for intricate shapes and the production of both small and large parts.
- Mechanical Engineering:
- Sand casting is used to manufacture a wide range of mechanical components, such as pumps, valves, gears, and pulleys.
- Its adaptability to various materials and sizes makes it suitable for diverse mechanical applications.
- Aerospace and Defense:
- Sand casting is employed to create complex aerospace components like engine parts, structural elements, and landing gear components.
- The ability to produce one-off or small-batch parts is advantageous in the aerospace sector.
- Heavy Machinery and Equipment:
- Sand casting is used to produce parts for heavy machinery and equipment, including construction machinery, agricultural equipment, and mining machinery.
- Energy and Power Generation:
- Parts for power plants, turbines, generators, and other energy-related equipment are often made through sand casting.
- Sand casting accommodates the production of components with intricate cooling passages and complex shapes.
- Oil and Gas Industry:
- Sand casting is employed in producing components for pumps, valves, and other equipment used in the oil and gas sector.
- Its versatility allows for the production of parts for various environmental conditions.
- Railway and Transportation:
- Sand casting is used for producing components in the railway industry, such as train wheels, couplings, and brake components.
- Marine Industry:
- Marine components like propellers, ship engine parts, and navigation equipment can be produced through sand casting.
- Architectural and Artistic Applications:
- Sand casting is utilized in creating decorative architectural elements, sculptures, and artistic pieces.
- Mining Industry:
- Sand casting is employed to produce components used in mining equipment and machinery, including wear-resistant parts.
- Foundry and Metalworking Industry:
- Sand casting is essential within the foundry industry itself for producing molds and cores used in other casting methods.
Sand casting’s adaptability, cost-effectiveness, and ability to handle a wide range of materials make it suitable for various industries. Its capability to accommodate both small-scale and large-scale production, along with the flexibility in casting size and complexity, makes it a popular choice for many applications.
Chapter 11: Environmental Protection and Sustainability of Sand Casting
The sand casting process can have several environmental impacts, including resource consumption, energy use, waste generation, and emissions. However, there are various measures that can be taken to improve the sustainability and reduce the environmental footprint of sand casting:
- Resource Management:
- Sand Consumption: Optimize sand usage by implementing sand reclamation systems to recycle and reuse sand.
- Responsible Sand Sourcing: Choose sand from sustainable sources to minimize environmental disruption.
- Energy Efficiency:
- Melting Furnaces: Opt for energy-efficient melting furnaces and technologies to reduce energy consumption during metal melting.
- Heat Recovery: Implement heat recovery systems to capture and reuse waste heat from furnaces and other equipment.
- Emission Reduction:
- Air Emissions: Install effective exhaust systems and filters to reduce emissions of pollutants and particulate matter.
- Green Technologies: Explore cleaner energy sources, such as natural gas or renewable energy, to power melting furnaces.
- Waste Management:
- Waste Minimization: Implement waste reduction techniques and proper waste segregation to minimize waste generation.
- Recycling: Recycle metal scraps, sand, and other materials whenever possible to reduce the need for virgin resources.
- Water Conservation:
- Water Usage: Use water efficiently during processes like sand preparation and cooling.
- Water Recycling: Implement water recycling systems to reuse water for processes like sand cooling and mold preparation.
- Eco-Friendly Binders:
- Consider using eco-friendly binders that have lower environmental impact compared to traditional binders.
- Evaluate alternative binder systems, like water-based or solvent-free binders.
- Green Sand Additives:
- Choose environmentally friendly additives and materials for sand preparation that minimize emissions during the casting process.
- Lean Manufacturing:
- Optimize production processes to reduce material waste, energy consumption, and unnecessary handling.
- Design Optimization:
- Optimize casting designs to minimize material use, avoid complex shapes that lead to higher waste, and reduce machining needs.
- Environmental Compliance:
- Adhere to local environmental regulations and standards for air quality, water use, waste disposal, and emissions.
- Continuous Improvement:
- Implement a culture of continuous improvement by regularly assessing processes and identifying opportunities for sustainability enhancements.
- Training and Education:
- Educate employees about environmental impacts and sustainability practices to foster a culture of responsible production.
By adopting these measures, sand casting operations can significantly reduce their environmental impact and contribute to improved sustainability. Sustainable practices not only benefit the environment but can also lead to cost savings, enhanced reputation, and compliance with increasingly stringent environmental regulations.
Chapter 12: Innovation and Trends in Sand Casting
In the field of sand casting, innovative trends are emerging that leverage digital manufacturing technologies and the application of new materials. These trends aim to enhance efficiency, accuracy, sustainability, and the overall casting quality. Here are some notable trends:
1. Digital Manufacturing and Simulation:
- Digital Twin Technology: Creating virtual replicas of casting processes and products to optimize designs, predict performance, and identify potential defects before physical production.
- Process Simulation: Advanced software simulates the entire casting process, predicting solidification patterns, thermal stresses, and defects, enabling process optimization.
- Additive Manufacturing Integration: Combining sand casting with additive manufacturing (3D printing) to produce intricate cores, patterns, and prototypes more efficiently.
2. Data-Driven Decision-Making:
- IoT Integration: Sensors and IoT devices monitor process parameters in real time, enabling data-driven decisions for improved quality and process control.
- Big Data Analysis: Analyzing data from various stages of casting processes helps identify patterns, anomalies, and areas for optimization.
3. Sustainable Practices:
- Green Binders and Additives: Developing and using environmentally friendly binders and additives that reduce emissions and waste.
- Sustainable Sand Management: Efficient sand reclamation systems that recycle and reuse sand, reducing resource consumption and waste.
4. Advanced Materials:
- High-Performance Alloys: Application of advanced alloys with superior mechanical properties and corrosion resistance in critical applications.
- Metal Matrix Composites (MMCs): Integrating reinforcement materials like ceramic fibers or particles into metal matrix for enhanced strength and properties.
5. Automation and Robotics:
- Robotic Pouring: Automated pouring systems using robots to precisely control pouring speed, angle, and consistency, reducing defects.
- Robotic Finishing: Robots with advanced sensors and tools for precise deburring, grinding, and finishing tasks.
6. Artificial Intelligence (AI) and Machine Learning (ML):
- Defect Prediction: AI algorithms analyze historical data to predict defects and their causes, helping operators prevent issues in real time.
- Quality Assurance: ML models monitor process variables and use predictive analytics to optimize parameters for higher quality castings.
7. Novel Coating Techniques:
- Advanced Surface Treatments: Application of advanced coatings, platings, and surface treatments to improve wear resistance, corrosion resistance, and other performance characteristics.
8. Hybrid Processes:
- Combining Processes: Integration of sand casting with other manufacturing processes like investment casting, die casting, and machining to create hybrid solutions for complex parts.
9. Design Optimization Tools:
- Topology Optimization: Using AI and simulation tools to generate optimized designs that balance performance, material usage, and manufacturing considerations.
10. Renewable Energy for Melting: – Induction Heating: Transitioning from conventional fuel-based melting to induction-based heating systems for energy efficiency and reduced emissions.
These trends reflect a shift toward more efficient, sustainable, and technologically advanced sand casting practices. By adopting these innovations, manufacturers can achieve higher precision, reduce defects, and produce castings with improved mechanical properties and environmental impact.