Aluminum alloy castings are widely used in railway, military, aerospace, automotive, medical and other fields because of their good comprehensive mechanical properties. Aluminum alloy castings have the characteristics of low density, high strength coefficient and hardness, and become one of the most suitable materials to realize light-weight structural thin-walled parts. However, a series of problems will occur in the manufacturing process of thin-walled castings. Too fast cooling speed will reduce the fluidity of molten metal, which makes the metal solidify prematurely before the mold cavity of thin-walled castings is fully filled, resulting in incomplete filling or porosity of castings. A light-weight aluminum alloy thin-walled part applied to maglev train is selected, its structural characteristics and product quality performance requirements are analyzed, effective solutions to specific problems are put forward, and efficient and reasonable casting process schemes are explored.
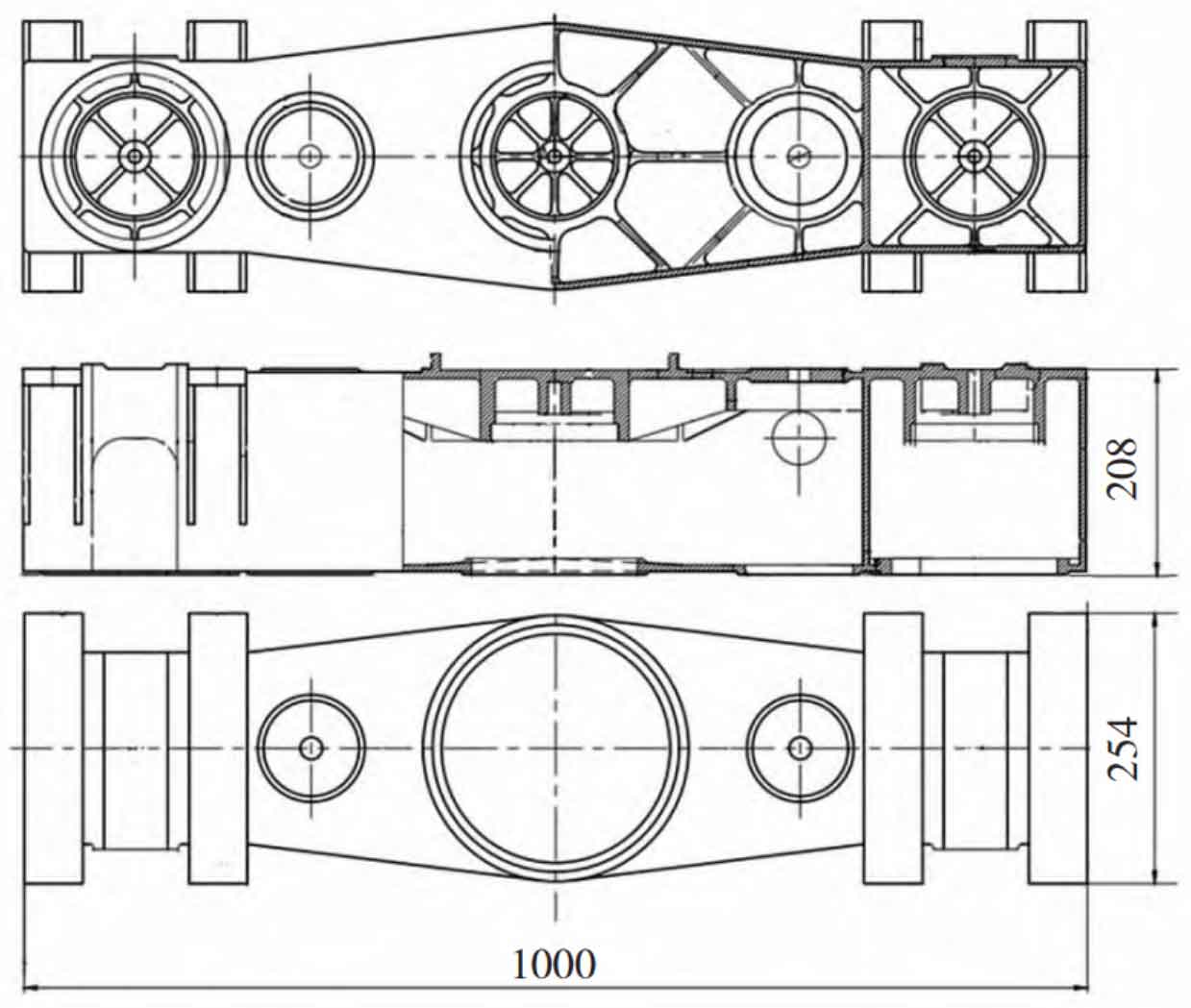
External dimension of parts 1000mm × 254mm × 208mm, uniform wall thickness 6mm, as shown in the figure 1. The internal quality of castings shall be inspected by X-ray according to ASTM e155 standard for pinholes and other casting defects, and the internal defect grade limit is ≤ level 1. The casting surface shall be free of cold shuts, cracks, shrinkage cavities, penetrating defects and serious defects, and the surface roughness shall be ra25; The material is ZL101A and treated with T6. The mechanical properties require that the tensile strength ≥ 275mpa, yield strength ≥ 190mpa, elongation ≥ 2% and hardness HB ≥ 80.
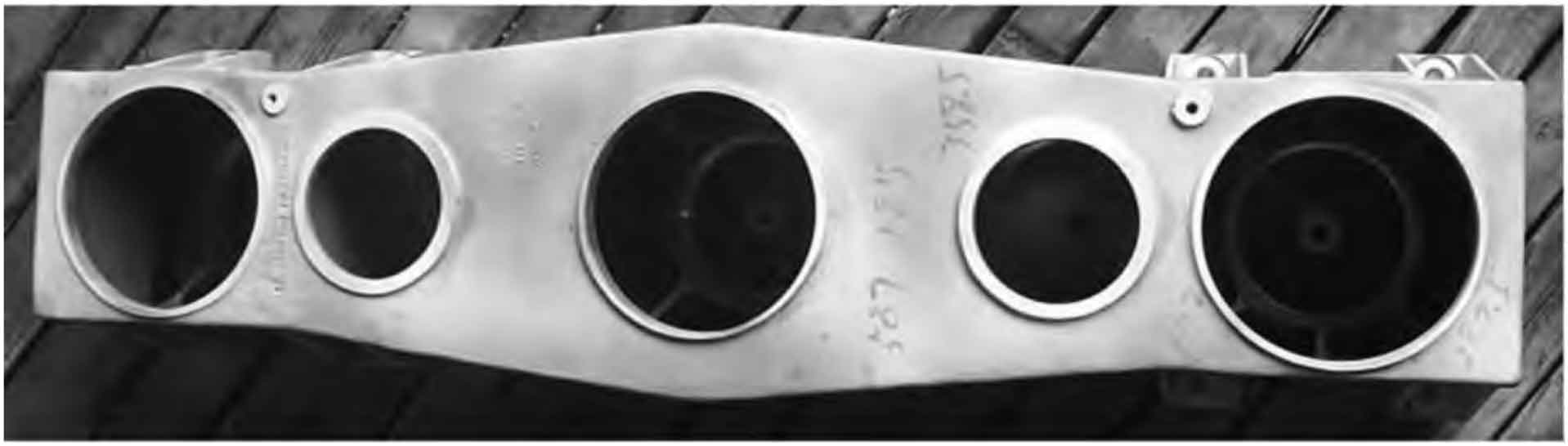
An efficient and reasonable process is designed according to the structure and performance characteristics of the casting. The process is proved to be feasible through computer numerical simulation. In view of the casting defects in the production of trial products, the causes are analyzed and corresponding control measures are taken. Finally, the parts are delivered qualified. The sand mold low-pressure casting method is adopted to pressurize the molten metal during solidification to achieve a good feeding effect, effectively avoid shrinkage cavity, porosity, porosity and other defects of thin-walled castings, and obtain better tissue density and higher internal quality stability. Figure 2 shows the finished product, with a casting qualification rate of more than 98%, almost without any casting defects, meeting the product technical requirements.