According to the principle of conventional parting surface selection: the parting surface shall be as simple as possible, and the flat parting surface shall be taken to avoid sand hanging tire (except for special circumstances). The parting surface shall be the largest horizontal plane of the casting as far as possible, and shall simplify the process, facilitate operation, and facilitate inspection and measurement.
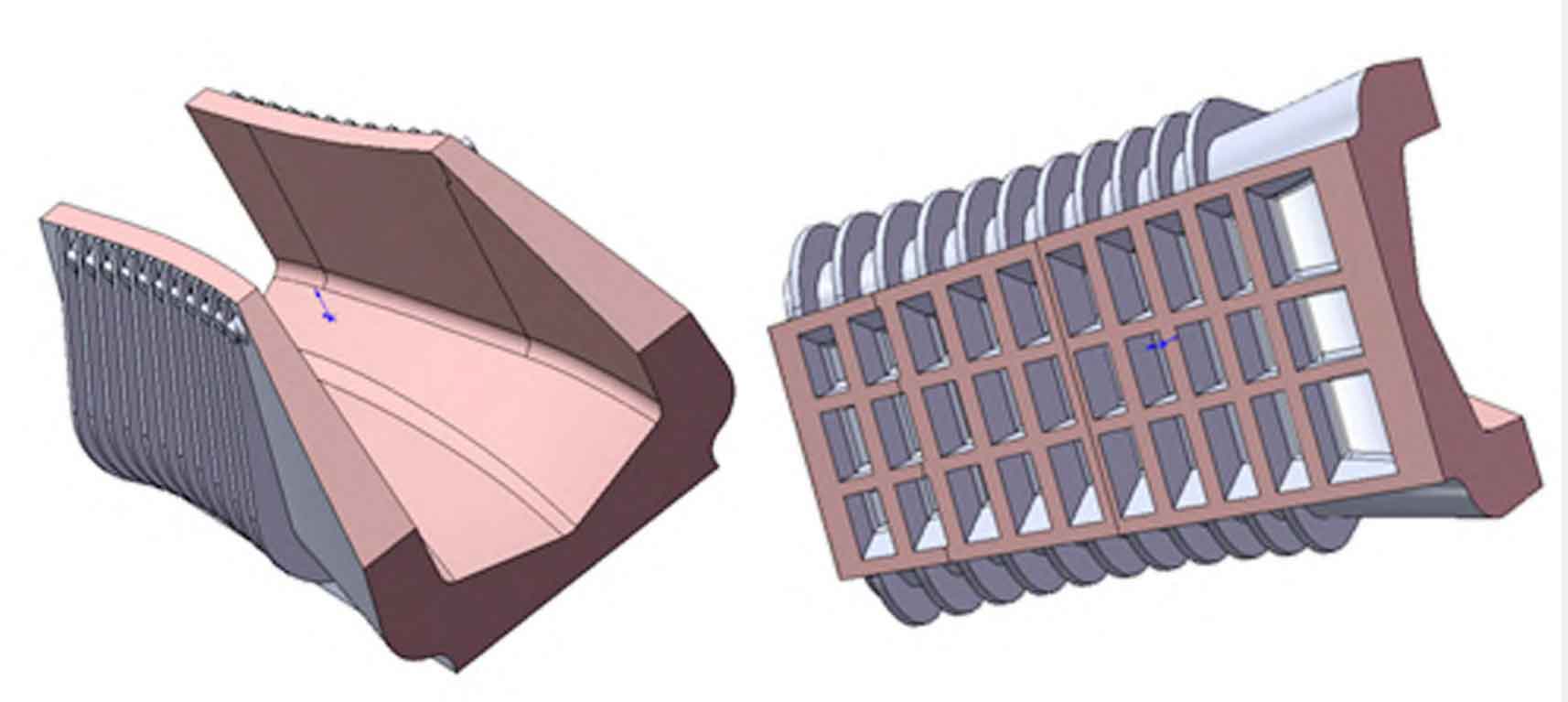
However, it can be seen from the stereogram in Figure 1 that the bottom of the saddle head is a large plane, and there are many blank weight reduction grooves with a depth of 300 mm~700 mm under the entire large plane. If this plane is selected as the parting surface, in order to ensure the overall quality of the casting, it is undoubtedly necessary to cast all the non machined weight reduction grooves under the riser, which will add great difficulty and workload to the subsequent cleaning work. Therefore, another scheme is selected, in which the saddle groove is upward and the parting surface is curved. As shown in Figure 2, the modeling structure is shown, in which NO.9 NO.11 NO.12 is the upper box sand core.
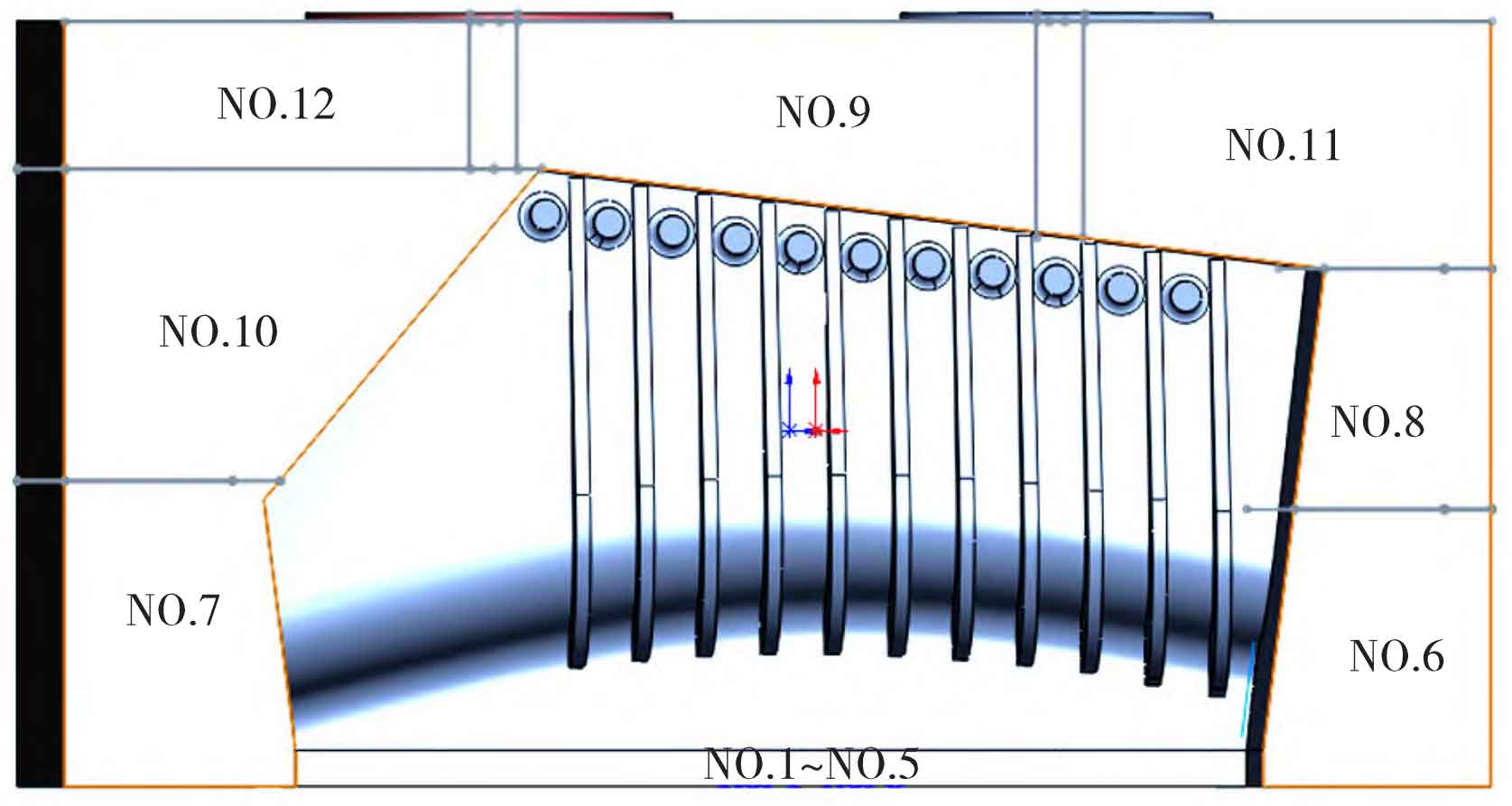