Semisolid forming (SF) was proposed and founded by Professor Flemings of Massachusetts Institute of Technology and his scientific research team in the 1970s. It refers to the forming and manufacturing of semi-solid metal billets in the liquid-solid paste region. The nucleation and growth of dendritic dendrites can be effectively inhibited by strong stirring or controlling the solidification process in the metal solidification process, and the formed dendritic dendrites can be continuously broken, and the equiaxed, fine, uniform primary phase suspended semi-solid metal slurry can be prepared in the liquid phase. This semi-solid metal slurry has excellent thixotropic fluidity even if the solid content exceeds 60% under the action of external force, and can realize the precision forming and manufacturing of complex structural parts. Semi-solid forming mainly consists of thixoforming, rheological forming, semi-solid rolling, semi-solid extrusion and semi-solid forging.
The preparation of fine and uniform equiaxed crystal billets or slurries is the key of semi-solid forming technology. At present, the commonly used preparation processes of semi-solid billets and slurries mainly include the following three methods:
(1) Liquid phase method. Including mechanical stirring method and electromagnetic stirring method. Typical preparation methods mainly include the MHD preparation method of Alcoa, the traveling wave electromagnetic stirring method of PECHINEY, the RDC double-propeller stirring method of BRUNEL University, the SSR collector mechanical stirring method of MIT, the composite electromagnetic stirring method of Beijing Research Institute, the MSB rotary drum stirring method of Beijing University of Science and Technology and the LSPWES low superheat weak electromagnetic stirring method Two-way electromagnetic stirring method of Tsinghua University, etc.
(2) Solidification control method. By controlling the nucleation and growth of dendritic dendrites during solidification, or adding nucleation catalysts or inhibitors, grain refinement can be achieved, and the spheroidization of grain structure during secondary solid solution process can be promoted. Typical preparation methods mainly include the near-liquidus semi-continuous casting method of Northeastern University, the chemical grain refining method of NORSK HYDRO Company of Norway, the NRC cooling slope method of URE Company of Japan and the CRP liquid flow mixing method of WPI in the United States.
(3) Solid phase method. Such as spray deposition method, RAP recrystallization remelting method, SIMA strain-induced melting activation method and powder metallurgy method.
Compared with investment casting, semi-solid forming technology can obtain higher comprehensive mechanical properties, and the production cycle of product process is very short, and the cost of mass production is lower. As shown in the picture, the microstructure of A356 aluminum alloy investment casting and semi-solid forming is compared, which shows that the grain has been significantly refined and spheroidized under semi-solid forming conditions.
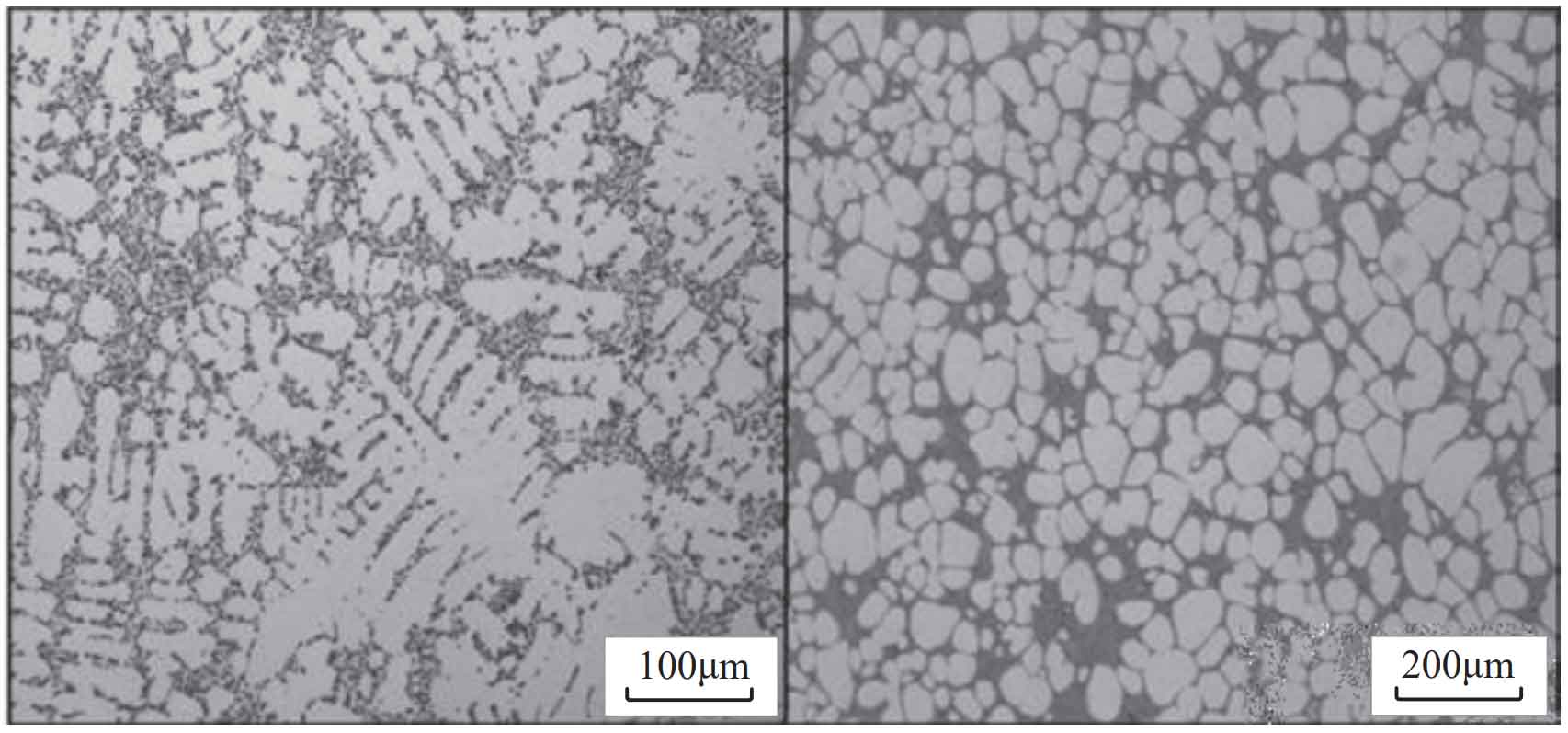
At present, the key restricting the semi-solid forming technology is that it can not manufacture products with complex shapes or cavity pipes. The mold manufacturing costs are high and the skill requirements for operators are high. However, the semi-solid forming technology is becoming increasingly perfect and mature. In the future, it will form a strong competition against the investment casting technology in the mass manufacturing of simple structural parts.