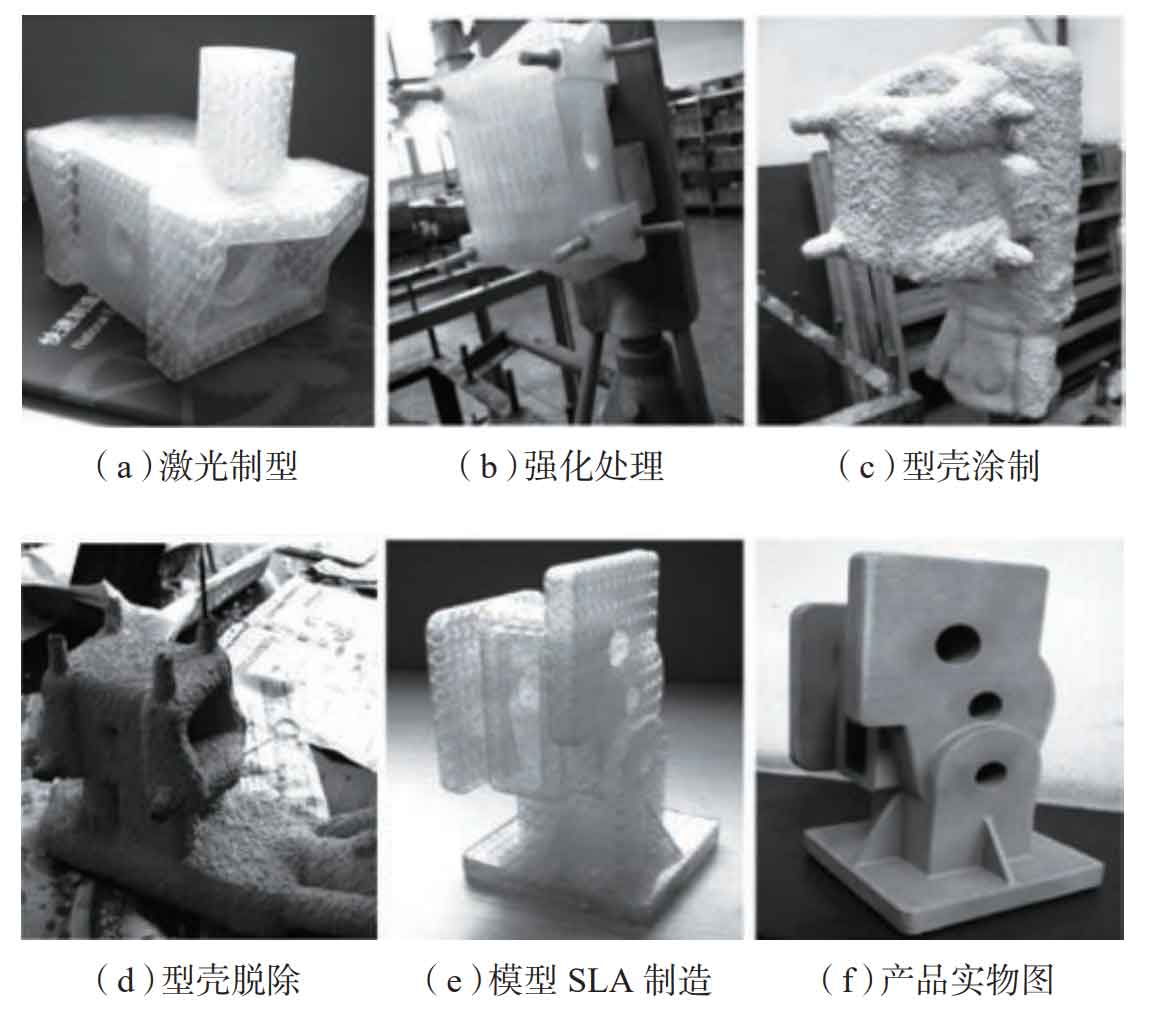
Additive manufacturing technology has become one of the key supports to improve the technical level in the aerospace field. At present, it is mainly applied in three aspects: structural contour verification, product forming manufacturing and investment mold precision prototype manufacturing. Boeing has completed the production of more than 300 kinds of 7X7 series civil aircraft parts with different structures in combination with additive manufacturing technology, and has passed the airworthiness certification. At the same time, Boeing and Honeywell jointly studied and proposed to use additive manufacturing technology to produce large products such as integral wings, annular frame beams, side panels, etc. China’s universities and scientific research institutions engaged in additive manufacturing mainly include Beijing University of Aeronautics and Astronautics, Tsinghua University, Xi’an Jiaotong University, Huazhong University of Science and Technology, Northwestern Polytechnic University, South China University of Technology, Beijing Longyuan Company, AVIC Heavy Machinery Laser, etc. Yan Yongnian team of Tsinghua University mainly focuses on the research of EBM and laser deposition deposition forming (LCD) additive manufacturing technology. Wang Huaming team of Beijing University of Aeronautics and Astronautics and Shi Yusheng team of Huazhong University of Science and Technology mainly focus on the selective laser sintering technology. In 2005, Wang Huaming’s team successfully realized the installation and application of three kinds of laser rapid prototyping titanium alloy structural parts on two kinds of aircraft, making China the second country in the world to master the application technology of laser rapid prototyping for aircraft titanium alloy structural parts. In recent years, Shi Yusheng’s team has focused on selective laser sintering rapid prototyping, selective laser melting rapid prototyping, and laser/isostatic pressing composite near-net forming technology. In recent years, the Lu Bingheng team of Xi’an Jiaotong University has developed the international first UV rapid prototyping machine and the integrated rapid additive manufacturing equipment and special material system of machinery, light and electricity. In recent years, the team of Huang Weidong from Northwestern Polytechnic University has deeply studied the production process of LENS additive manufacturing, and has solved the problem of precision manufacturing of key titanium alloy structural parts of C919 aircraft in cooperation with COMAC, forming a new process of characteristic additive manufacturing with independent intellectual property rights.
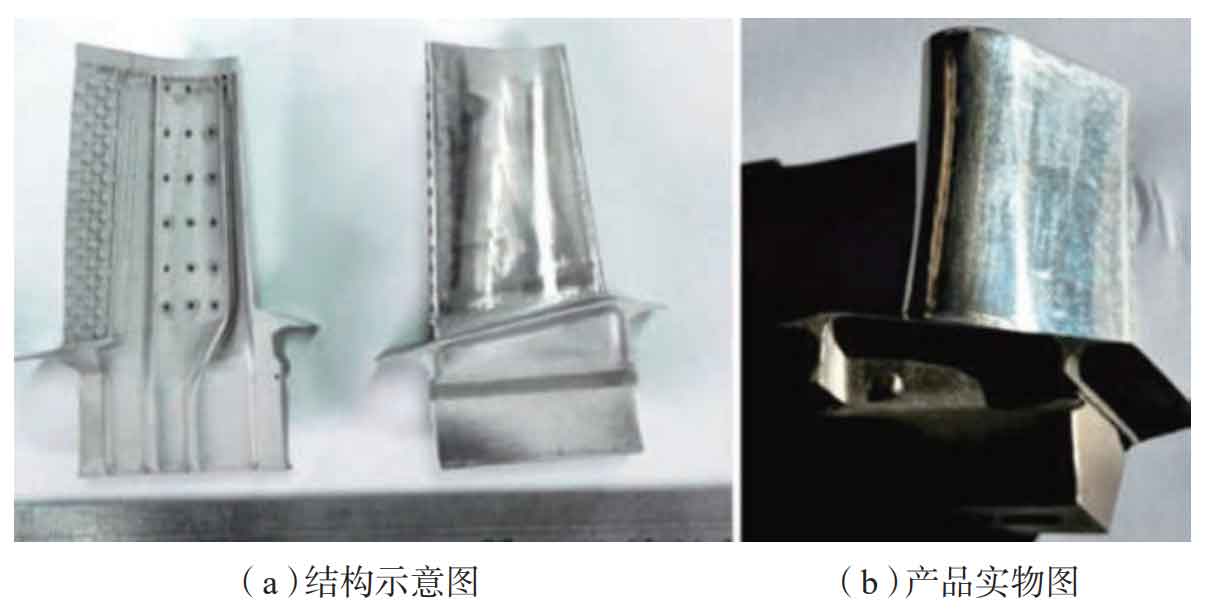
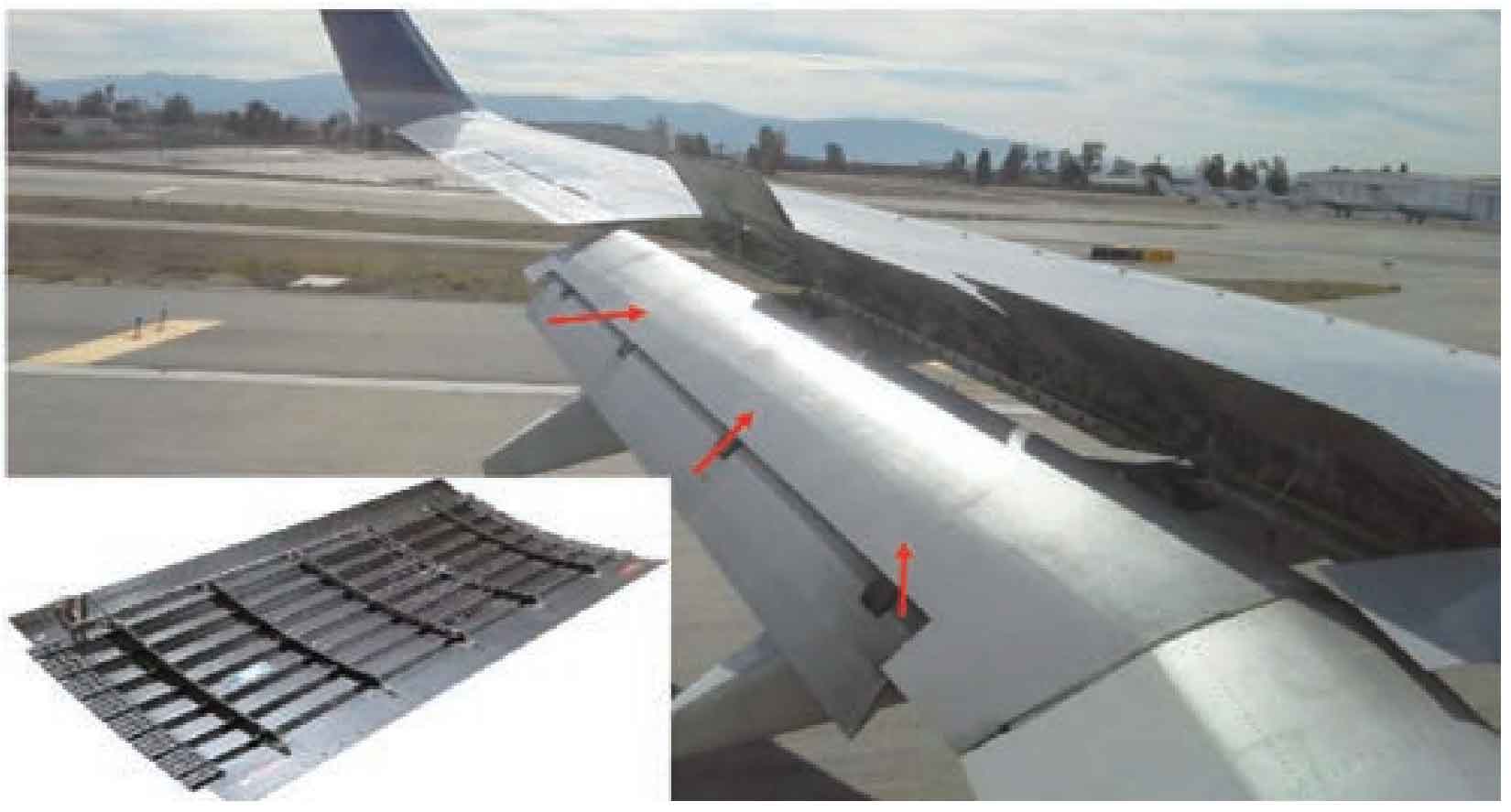
Figure 1 shows that Xi’an Qing’an Group Co., Ltd. used SLA laser additive manufacturing technology to realize rapid manufacturing of shell and parts during the development of aluminum alloy precision castings. Compared with investment casting shell, the cycle is shortened by 86%; Compared with investment casting parts, the cycle is shortened by 78%, which has significant economic benefits. Zong Xuewen of Xi’an Jiaotong University used FEM to analyze the thermal deformation mechanism of the photocurable resin prototype and the shell during the high-temperature baking process, established the prototype – shell thermal deformation mathematical model and cracking criteria, and successfully solved the shell cracking problem in the rapid prototyping process of the new gas turbine guide additive manufacturing.
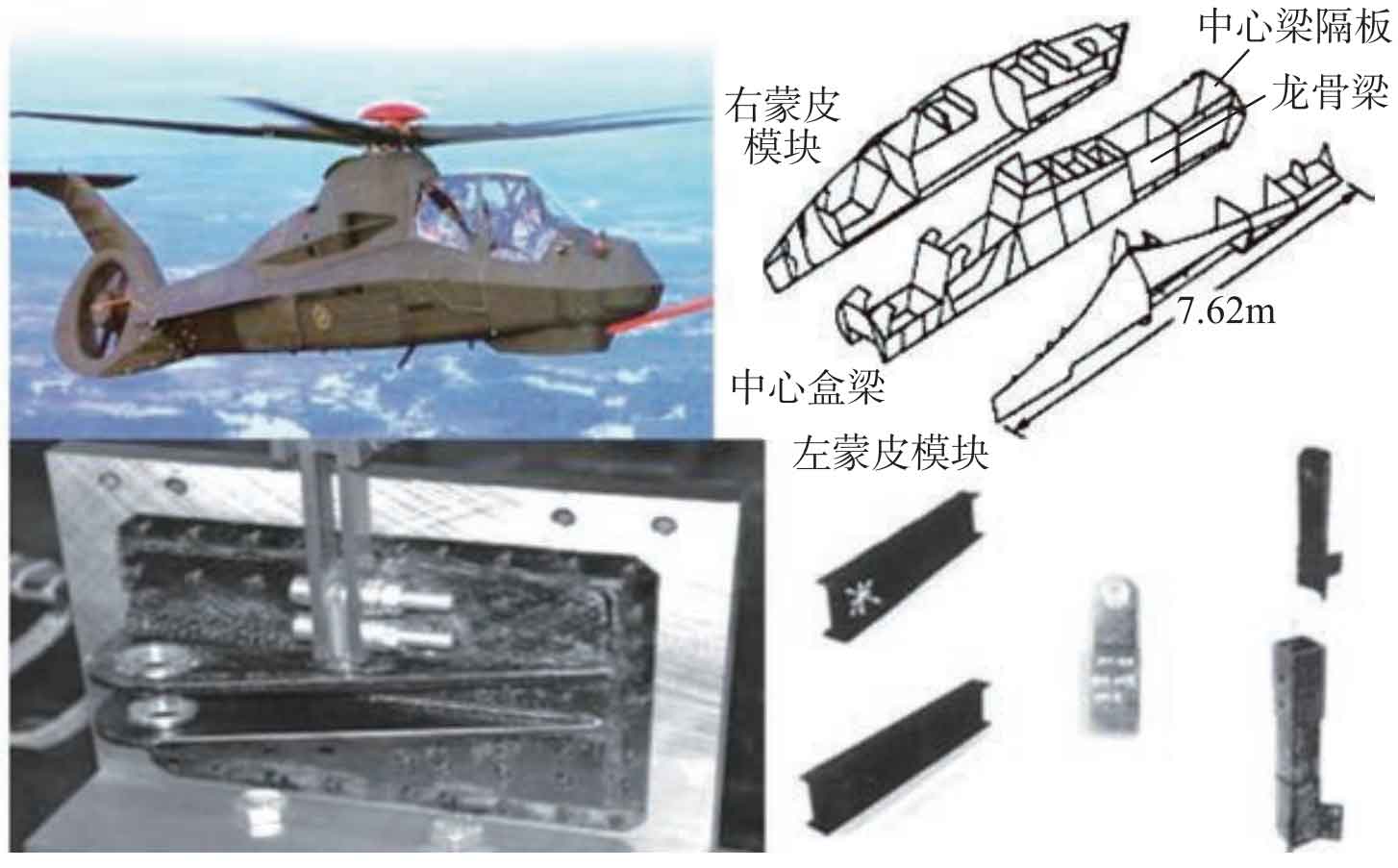
Jiang Yaolin, Zhejiang Institute of Mechanical and Electrical Design and Research, completed the structural optimization of the impeller gating system with the help of ProCast analysis results. The integrated forming of the impeller cavity and the integral resin sand casting of the gating system was realized by using additive manufacturing. The closed centrifugal pump impeller casting was successfully prepared by investment casting technology. Figure 2 shows the superalloy turbine blade test piece prepared by Wang Huaming, an academician of Beijing University of Aeronautics and Astronautics, using the laser additive manufacturing process. The primary dendrite spacing of the solidification structure obtained is two orders of magnitude finer than that of the casting alloy, without eutectic and porosity. Based on the analysis of the characteristics of the combustion cracking process of sintered material plastic powder, the selective laser sintering plastic powder is used as the process prototype to prepare ceramic shell on its surface. After high temperature roasting, investment casting can be realized. Sun Haixiao of Huazhong University of Science and Technology successfully cast zinc alloy metal castings using this process. Cui Jianfang of Central North University can use the laser sintering molding process, PS powder sintering molding and wax impregnation processing process to produce soluble resin mold for investment casting in batches. Figure 3 shows the aileron structural parts of civil aircraft developed by Cong Jingjie and others of COMAC Beijing Civil Aircraft Technology Research Center using liquid additive manufacturing technology. Figure 4 shows the base plate beam and joint components of RAH – 66 Comanche helicopter manufactured by Boeing of the United States using liquid forming additive manufacturing technology, and the manufacturing of additive for CH – 46 helicopter engine fairing is shown in Figure 5.
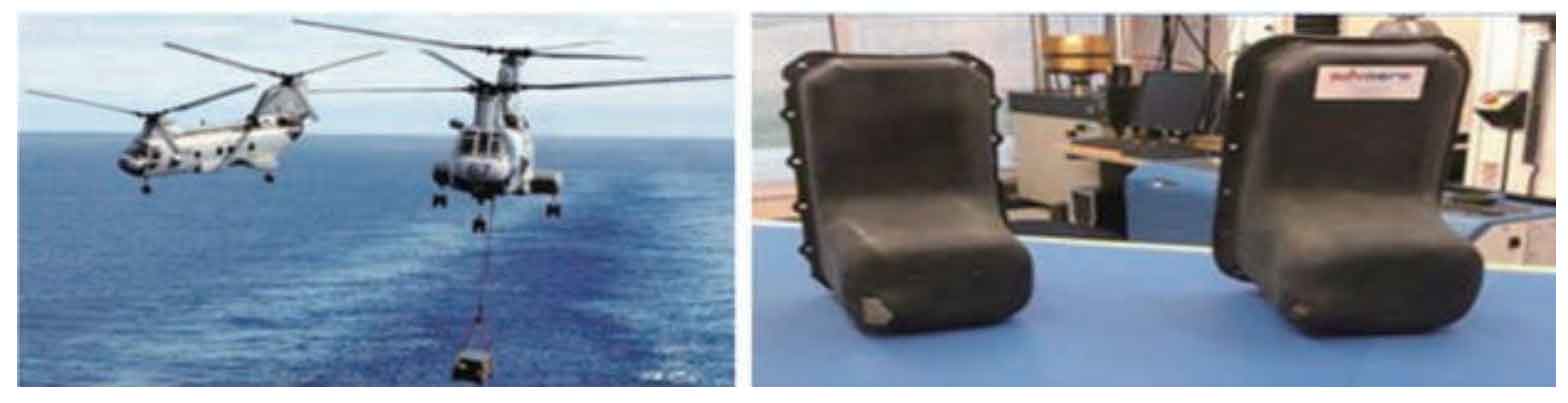