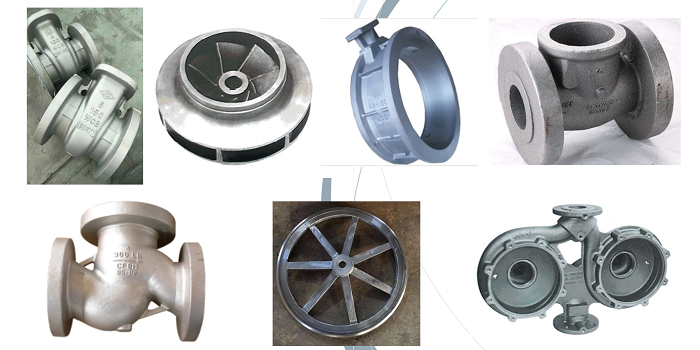
The shrinkage porosity and porosity are more common in ductile iron than in ordinary gray iron. To prevent them, more attention and control must be given. The large and concentrated holes that can be obviously seen are called shrinkage holes, and the small and scattered holes that are not suitable to be seen are called shrinkage porosity. Most of them produce shrinkage cavity in the upper part of the hot spot. At the hot spot of the casting and under the shrinkage cavity, there are usually scattered shrinkage porosity. However, for some centers with uniform wall thickness, or at the center of thick wall, shrinkage porosity can also occur.
Some of them are very small and can only be found under a microscope. This kind of shrinkage porosity is polygonal, sometimes continuous, sometimes intermittent, and distributed at the boundary of eutectic group. This shrinkage is called microshrinking. After the austenite dendrite solidification, the residual molten iron solidifies finally between the dendrites and forms micro shrinkage porosity due to the lack of feeding.
The volume of shrinkage cavity and porosity of ductile cast iron is larger than that of common gray cast iron, white cast iron and carbon steel. However, in production, the riser free process can also be used to obtain sound ductile iron castings.
Causes of shrinkage cavity and porosity increase in ductile cast iron
- After spheroidizing treatment, spheroidal graphite will precipitate in the molten iron immediately, and the spheroidal graphite in the molten iron will grow up with the gradual decrease of temperature. The process of graphite precipitation and growth is accompanied by the expansion of liquid metal.
- The divorced eutectic transformation of ductile cast iron is carried out in the way of divorced eutectic. It is easy to form microshrinking because of the atherosclerotic coagulation in which the internal and external processes are almost simultaneous.
- Due to the atheromatous solidification, the eutectic expansion of the castings will last for a long time during the eutectic transformation. The eutectic time of the ductile cast iron can be longer than that of the ordinary gray cast iron by more than one time. As a result, the graphitization expansion of the eutectic transformation is large.
- Mold wall movement during eutectic solidification, because of atherosclerotic solidification, the solidification layer on the surface of the casting is very thin, so that the solidification shell with sufficient strength can not be established to inhibit the graphitization expansion during eutectic solidification, resulting in the mold inner wall moving outward. When the mold rigidity is not enough, the cavity size increases, which leads to further increase of shrinkage cavity volume.
- After spheroidizing, the original hydrogen, oxygen, nitrogen and CO gas contents are reduced, and the molten iron is purified, resulting in the reduction of external core. Moreover, the higher the superheat temperature of the molten iron is, the higher the purification degree is, and the tendency of supercooling is more serious. In addition, the spheroidized elements magnesium and rare earth can form carbonization with carbon, which reduces the degree of graphitization and increases the tendency of shrinkage.