The lost foam casting products have the advantages of good surface quality, high dimensional accuracy, and high process yield, and can be applied to the production of ductile iron. The gearbox housing requires high strength, toughness, wear resistance, and seismic performance, and is made of QT450-10 material. The weight of the gearbox housing casting is 112 kg, with a wall thickness of 54 mm at the thickest part and 14 mm at the thinnest part, and a concentrated geometric hot spot. Based on the equipment production capacity and casting characteristics of the author’s foundry, the lost foam casting process is selected.
Original process of ductile iron reducer housing
The end face design process margin is 4 mm, the furnace temperature is 1580-1600 ℃, the pouring temperature is 1370-1440 ℃, the pouring negative pressure is -0.06~-0.04 MPa, and the negative pressure holding time is 900 seconds. The chemical composition of the reducer housing is shown in Table 1. The mechanical properties of the Y-shaped specimen meet the requirements of QT450-10, and the spheroidization rate of 2-3 levels also meets the technical requirements of the ductile iron reducer housing. However, defects such as wrinkling, shrinkage porosity, and shrinkage porosity occurred during the trial production of the reducer housing using lost foam casting. In the process of small-scale production, the proportion of wrinkled skin on the end face of the reducer housing and shrinkage defects at the geometric hot joint is also relatively high.
The carbon content of ductile iron castings is generally 3.5%~3.8%, which is prone to carbon defects. Considering both gas generation and carbon content, the white mold of ductile iron is selected with copolymer material. The copolymer material balances the gas evolution and solid carbon content of EPS and EPMMA (expandable polymethyl methacrylate), reducing the possibility of carbon defects in castings and decreasing the risk of porosity defects in castings. The reducer housing made of ductile iron material has wrinkles on the end face and shrinkage holes at the geometric hot joint during mass production. The reasons for the formation of these two defects are now analyzed.
Wrinkle defects often occur at the final flow point of molten metal or at the “cold end” of the flow. It usually appears at the top, vertical side walls, or dead corners of castings. Heating of Copolymer foam Pattern Used for Forming in EPC During the decomposition process, a large amount of gaseous, liquid, solid products and other pyrolysis products are generated. These products are affected by various factors during transportation, and the state, composition, and discharge form of pyrolysis products vary greatly. This is the fundamental reason for the occurrence of dispersed carbon defects in lost foam casting. The original process of the gearbox housing was top injection, but in reality, it is A midsole injection process using a mold cavity as a sprue. The casting is a rotating body, with a thickness of 35 mm at the upper end and a sharp thinning of 13 mm at the bottom below 50 mm. The design of the sprue in the original process is on the top surface. During the pouring process, high-temperature molten iron enters the top surface of the white mold from the sprue, without gradually filling downwards from top to bottom. Instead, it directly penetrates the thick walled area at the top and uses the top of the mold cavity as a sprue. The high-temperature molten iron reaches the thin-walled area and starts to fill downwards in a fan-shaped manner. After reaching the bottom, it fills upwards again, ultimately presenting a turbulent filling method in the middle bottom, causing “cold ends” in the thick dead corners of the top and side surfaces, resulting in wrinkling defects.
From the carbon equivalent of ductile iron, it can be seen that the mechanical properties of the Y-shaped specimen meet the requirements of QT450-10, and the spheroidization rate of 2-3 levels also meets the technical requirements of the ductile iron reducer housing. The chemical composition of the reducer housing meets the requirements Request; At the same time, from the observation of the surface quality of the ductile iron reducer housing, there is no cold insulation or sand sticking problem, and the influence of spheroidization treatment temperature, pouring temperature, and negative pressure on the shrinkage of the reducer housing is excluded; The fundamental reason for the formation of shrinkage holes in ductile iron castings is that during liquid shrinkage and solidification of the alloy, a certain part of the casting (usually the final solidified hot spot) cannot receive timely replenishment of liquid metal, resulting in irregularly shaped holes with rough walls. The shrinkage defect of the gearbox housing mainly exists in the thick and large positions of the side machined holes, mainly caused by geometric hot spots. Therefore, to solve the shrinkage defect of the gearbox housing, it is necessary to start from the casting process, change the cooling structure of the casting, increase the heat dissipation surface area, reduce the local modulus, and eliminate the geometric shape of the casting Hot Festival.
The wrinkling defect of the gearbox housing is mainly due to the unreasonable design of the pouring system, which forms a filling method of mid bottom injection, causing turbulent flow of molten iron during the pouring process, resulting in wrinkling defects on the surface of the casting. The solution to this defect is to redesign the pouring system and replace it with a bottom injection pouring system, so that the filling method is pure bottom injection. During the filling process, the high-temperature molten iron gradually and steadily fills the mold from the ground, ultimately causing the low-temperature molten iron at the front end and the insufficiently vaporized products of the white mold to remain at the machining allowance position on the top surface of the mold cavity, resulting in a casting with a sound surface.
There are two traditional solutions for shrinkage defects in castings: one is to set up a riser at the hot junction and provide metal liquid that needs to be compensated for due to volume changes during the casting forming process to eliminate shrinkage; The second is to use a rapid cooling system, the most commonly used being to use a cold iron to form a human end zone at the hot junction, transforming the originally almost temperature free middle zone into a rapid cooling zone with a larger temperature difference, forming a sequential solidification, thereby eliminating shrinkage defects. Although both methods can solve shrinkage and porosity defects, they are not suitable for lost foam casting of gearbox housings because adding risers will reduce the process yield of gearbox housing castings and increase the overall process difficulty. However, using the cold iron process, due to the characteristics of lost foam casting, the cold iron is prone to detachment during molding and may cause deformation of the casting, resulting in high process difficulty and significant impact on the quality stability of the gearbox housing, as well as increasing casting costs. A new lost foam casting process, heat dissipation technology, has been developed to address the issue of hot spot shrinkage in ductile iron. The core purpose of heat dissipation technology is to change the structure of the casting, increase the heat dissipation surface area, reduce the modulus at the hot junction of the casting, and remove a large amount of heat with negative pressure gas during the solidification stage, which has a chilling effect. The heat sink has a larger specific surface area, which reduces the local modulus of the casting. Cold air carries away a large amount of heat, and the local sand in contact with the casting and the heat sink forms a microchannel flow heat exchange, forming a cooling zone with a large temperature difference. The heat sink acts as a cold iron, making the casting change from local solidification to a similar sequential solidification, eliminating shrinkage and porosity defects. The process advantages of the heat sink are simple and convenient operation; The casting process has little impact; Almost does not affect the process yield of gearbox housing castings; The post-processing of the gearbox housing is simple.
Conclusion
(1) By optimizing the pouring system, the filling process of the casting is smooth, and the iron liquid with impurities at the front end is collected using the process margin to solve the wrinkling defect of the casting.
(2) The production of ductile iron parts by lost foam casting results in shrinkage due to hot spots, making it difficult to use traditional riser and cold iron processes. Therefore, a new process method, namely the heat sink process, has been designed. Install a certain number of heat sinks at the hot nodes of castings to enhance local heat dissipation speed, eliminate geometric hot nodes, and solve shrinkage defects in castings. The heat sink process has been verified through practical testing of the gearbox housing casting, proving that this process meets the design requirements and can solve the shrinkage cavity defect of the casting. This is a new method of using lost foam casting to solve shrinkage cavity defects.
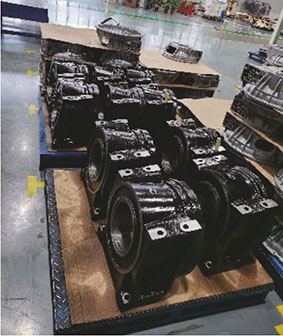
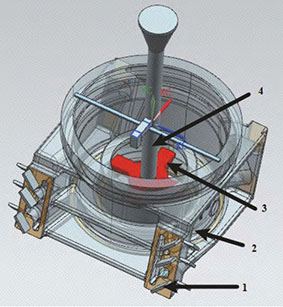
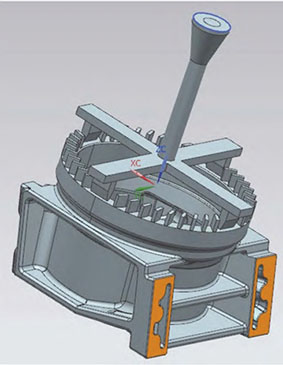