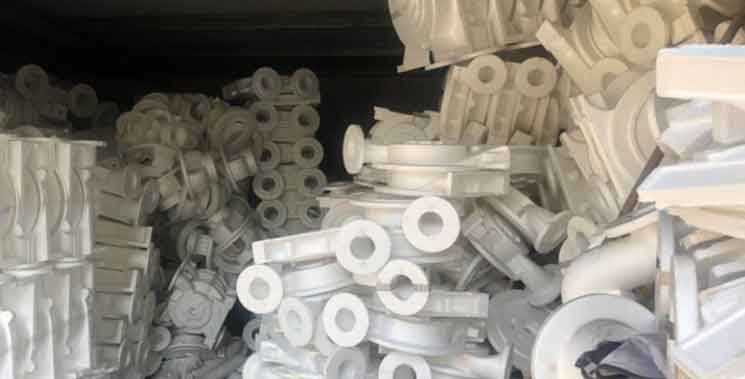
Lost foam casting offers several advantages that simplify design constraints and open up new possibilities in component manufacturing. Here are some key advantages of lost foam casting in this regard:
- Complex Geometry: Lost foam casting enables the production of components with complex geometries that would be difficult or costly to achieve using other casting methods. The foam patterns used in lost foam casting can be easily shaped and manipulated to create intricate details, undercuts, thin walls, and internal cavities. This design freedom allows for the creation of components with unique and complex shapes, opening up new design possibilities.
- Near-Net Shape Casting: Lost foam casting produces near-net shape components, reducing the need for extensive post-casting machining or finishing. The foam pattern accurately replicates the final shape of the component, minimizing material wastage and saving time and cost associated with material removal. This near-net shape capability simplifies the design process by reducing the complexity and cost of post-casting operations.
- Integrating Features: Lost foam casting allows for the integration of multiple features into a single cast component, reducing the need for separate parts and assembly operations. This integration of features simplifies the overall design and assembly process, reducing component count, improving assembly efficiency, and potentially reducing weight.
- Thin Walls and Lightweighting: Lost foam casting enables the production of components with thin walls, providing weight reduction opportunities. The foam patterns can be designed to create thin-walled sections without compromising structural integrity. This lightweighting capability is particularly advantageous in industries such as automotive, aerospace, and transportation, where weight reduction is a critical factor for improving fuel efficiency and performance.
- Elimination of Cores and Parting Lines: Lost foam casting eliminates the need for cores and parting lines, simplifying the design process and reducing manufacturing complexity. Without the constraints imposed by cores and parting lines, designers have more flexibility to create complex internal geometries and seamless external surfaces. This leads to components with improved aesthetics, reduced stress concentrations, and enhanced functionality.
- Reduced Tooling Costs: Lost foam casting can significantly reduce tooling costs compared to other casting methods. The foam patterns used in the process can be produced using low-cost molds or even 3D printing techniques. This eliminates the need for complex and expensive molds and cores, making lost foam casting a cost-effective solution for small to medium-scale production or for prototyping.
- Design Iteration and Prototyping: Lost foam casting allows for rapid design iteration and prototyping due to its lower tooling costs and shorter lead times compared to traditional casting methods. Design changes can be quickly implemented by modifying the foam pattern, enabling faster evaluation of design concepts and reducing time to market.
By simplifying design constraints and offering greater design freedom, lost foam casting empowers engineers and designers to push the boundaries of what is possible in component manufacturing. It enables the production of complex, lightweight, and highly integrated components that meet specific performance requirements while reducing costs and lead times.