Create a 3D model of the investment casting and gating system based on the designed gating system, and import it into ProCAST software for defect prediction. Mesh the imported model. In order to improve the accuracy of the calculation results, the unit grid density is set to 4, and the total number of face grids is 147072. Then, perform volume grid division, and the total number of volume grids is 785303. Enter the cast module and set the process parameters according to the traditional scheme data. After comparing the pouring situation in the gravity filling directions of ± x, ± y, and ± z, it was found that the filling effect is best when the gravity direction is set to – z direction, and the shrinkage of investment castings is less. The edited material is the composition of 304 stainless steel in the table. Without considering radiation heat transfer, the cooling method is air cooling, and the interface heat transfer coefficient between stainless steel and membrane shell is 500W/(m2 · K).
C | Cr | Mn | Mo | Ni | S | Si |
0.08 | 18 | 1.5 | 0.5 | 8 | 0.03 | 1 |
The analysis results of shrinkage porosity and porosity after optimizing the pouring system are shown in Figure (a). The shrinkage porosity at the corners has been improved, and the maximum shrinkage porosity is 3.75%. From the solidification process of investment castings (Figure (b)), it can be seen that the solidification of castings is basically sequential solidification, without isolated liquid phase zones. From the simulation results, it can be seen that optimizing the pouring system has reduced a large number of shrinkage cavities, but a small amount of shrinkage porosity still exists. Therefore, it is considered to adjust and optimize the process parameters.
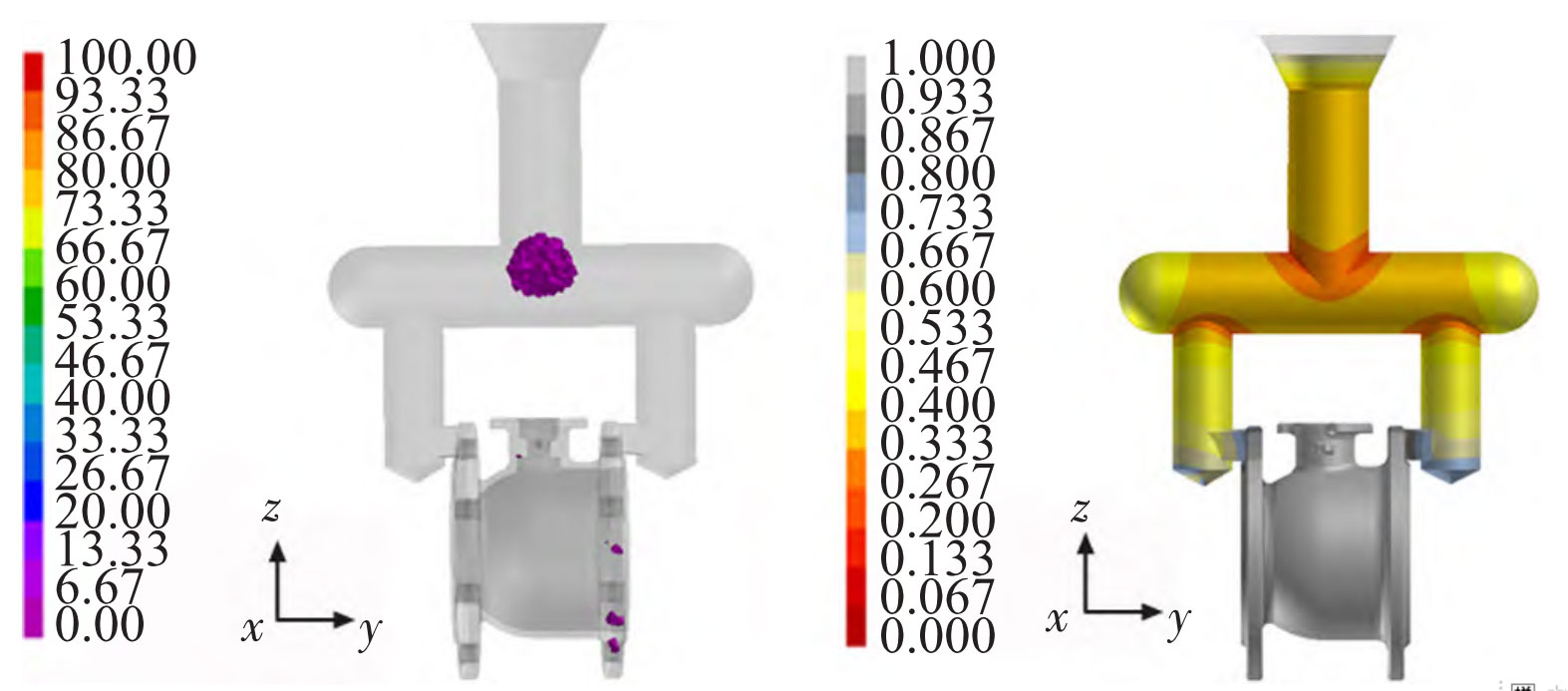