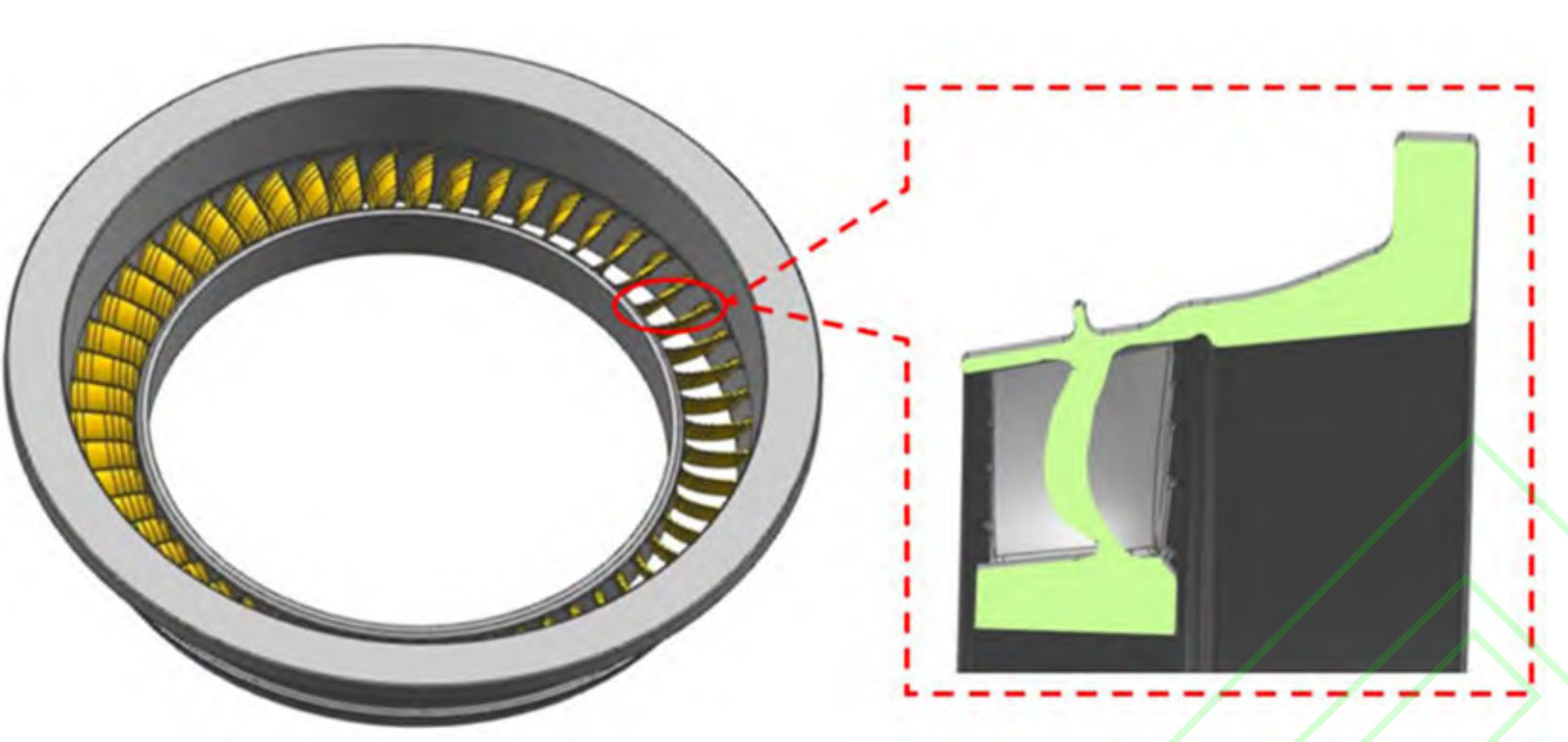
The turbine guide is made of K4169 superalloy, and its structure consists of inner ring, outer ring, flange and blade. The specific geometric modeling is shown in Figure 1. Among them, the inner ring has a diameter of 236 mm and a thickness of 8mm; The outer ring has a diameter of 366mm and a thickness of 2mm at the thinnest point; The flange thickness is 24mm, which is the thickest area of the casting. It is necessary to match a suitable gate or riser to compensate for the liquid and solidification shrinkage of the alloy liquid in the mold cavity, ensuring the density of this part.
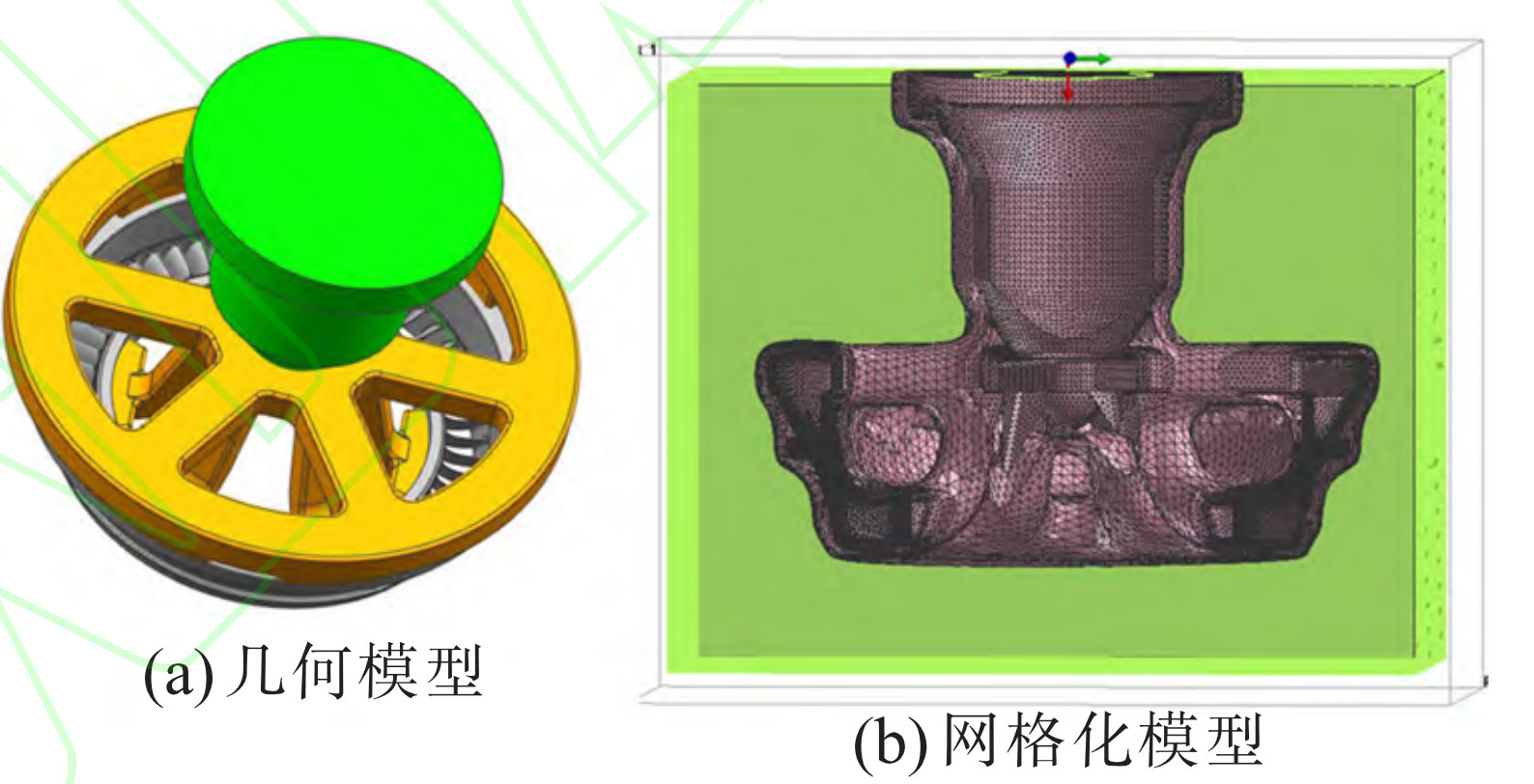
The shape of the blade is similar to a “crescent” shape, presenting a thin and thick appearance on both sides and a thick middle. Its structure differs greatly from traditional blades, with a thickness of only 0.5 mm at the thinnest point and up to 51 pieces. This part should focus on considering the integrity of filling and the excellent metallurgical quality, to avoid problems such as insufficient pouring or the formation of shrinkage and porosity defects. In addition, according to the local cross-sectional morphology in Figure 1, it can be seen that there is a significant difference in the thickness ratio of some areas of the guide. It is necessary to match reasonable pouring time, pouring temperature, cooling environment, etc. to avoid metallurgical defects such as cold shuts, insufficient pouring, and shrinkage porosity in the casting.
Simulation parameters | Casting material | Shell material | Shell thickness/mm | Pouring temperature/℃ | Mold shell temperature/℃ | Furnace size/m | Cooling method | Pouring time/s | Interface heat transfer coefficient/(W · m ^ -2K ^ -1) | Termination Steps | Convergence accuracy | Filling ratio (%) |
Set value | K4169 | Mullite | 10 | 1500 | 1050 | φ2.2×2.6 | Vacuum cooling | 4 | 500 | 100000 | 1X10^-5 | 100 |
Based on the above analysis of the structural characteristics of the turbine guide and the melting characteristics of K4169 high-temperature alloy, the initial pouring system and key process parameters of the turbine guide have been developed. The casting process requires a matching sand box size of 500mm × 500mm × 400 mm。 Use ProCAST software to mesh the sand box pouring system turbine guide model, and then assign simulation parameters such as material, pouring temperature, and boundary conditions of the sand box, casting, and mold shell in the model. The relevant pouring system and key process parameters are shown in Figure 2 and Table respectively. In addition, using ProCAST software to calculate the weight of the initial pouring system of the turbine guide, it was found that the part mass was 7.25 kg, and the pouring system mass was 59.77 kg, resulting in a metal utilization rate of 12.13% for this time.