In order to limit the speed of each axis in the process of five axis simultaneous high-speed forming of sand mold, adopting look ahead control is an effective method. According to the formula, the speed of x-axis and y-axis is as follows:
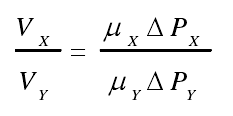
According to the formula, the machining speed curve can be planned in the process of five axis linkage machining, but the speed ratio of each axis is always constrained by the ratio of position change rate. In the same way, there is a proportional constraint relationship between the other axes’ velocities. Therefore, the speed of any coordinate axis can be limited by look ahead control, and the speed control of the other four axes can be realized, and online look ahead calculation of five coordinate axes can be avoided. When there are positive and negative speed limits on each axis, the formula for calculating the velocity of five coordinate axes constrained by the x-axis velocity VX can be obtained by using the formula
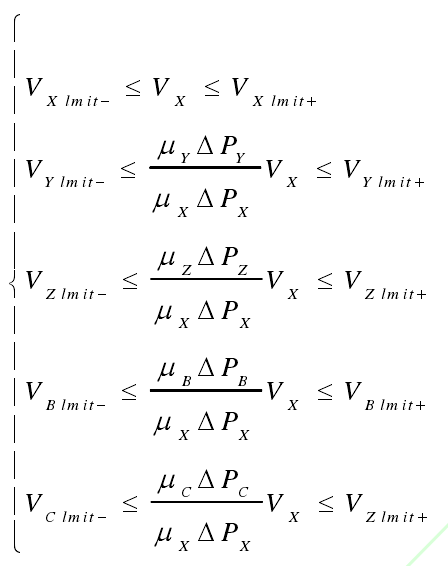
According to the formula, the velocity range of x-axis can be obtained. The boundary value is called X-axis forward looking velocity threshold, which is expressed by vxthreshold. By setting the x-axis maximum speed as the preview speed threshold, the five axis linkage speed overall control can be realized through the x-axis single axis speed look-up control. In the same way, when y-axis, z-axis, b-axis and c-axis are used as single-axis look-ahead control axis, the calculation formula of speed range is shown in the formula, and the minimum velocity boundary value obtained can also be used as the speed threshold of single axis look ahead control.
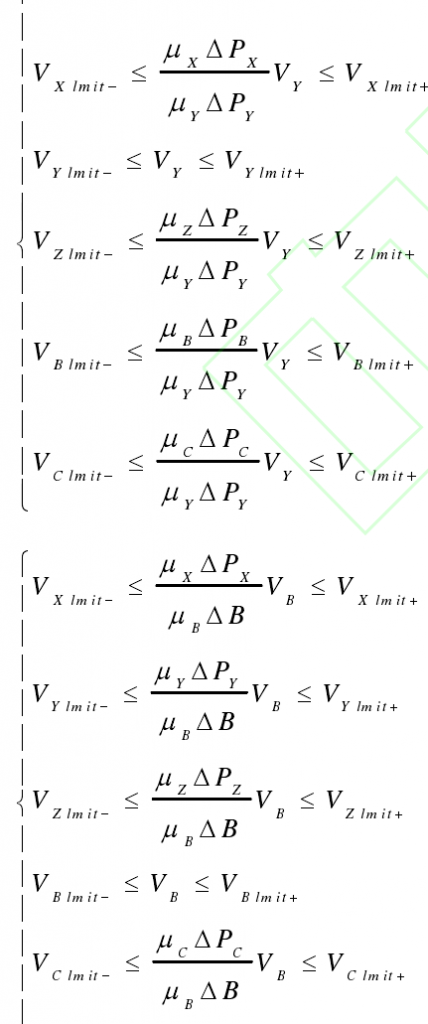
The schematic diagram of prospective dynamic control for five axis linkage high speed forming of sand mold is shown in the figure. CNC system circularly reads machining coordinates from the machining file to obtain the tool tip position. According to the look ahead control mechanism of PMAC system, the number of time periods required for look ahead operation is calculated, and the maximum speed value of the axis and the look ahead operation buffer area are set to store historical data and prospective calculation data; one coordinate axis is selected from the five axes of X, y, Z, B and C as the look ahead control axis, and the preview speed threshold of the axis is set. After running the program, the RTCP forward and inverse solution operation is performed, and the operation period is usually 1 ~ 10ms. In the process of five axis linkage high-speed feed of sand mold, the forward-looking dynamic control divides the motion into small segments in advance, and carries out prospective calculation according to the set time interval. If it is found that the speed of inverse solution of RTCP exceeds the limit, the appropriate acceleration and deceleration will be planned by adjusting the time base to ensure the stable processing.
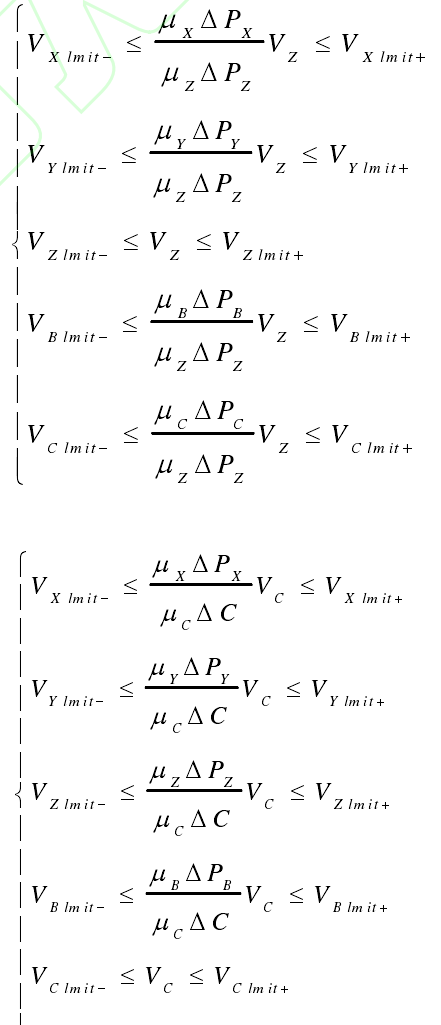
The number of time periods required for the single axis look ahead control can be calculated according to the formula, where TS is the look ahead servo period and Amax is the maximum acceleration of the axis.
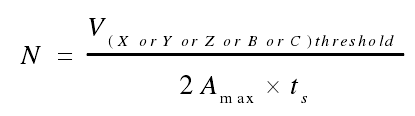