Abstract:
The heavy-section machine tool tray castings produced by our company as an example to analyze and elaborate on the causes of slag hole defects on the casting surface during production. By optimizing the gating system process and adopting suitable coatings, the slag hole defect problem is solved, improving the product’s appearance quality and meeting customer technical requirements.
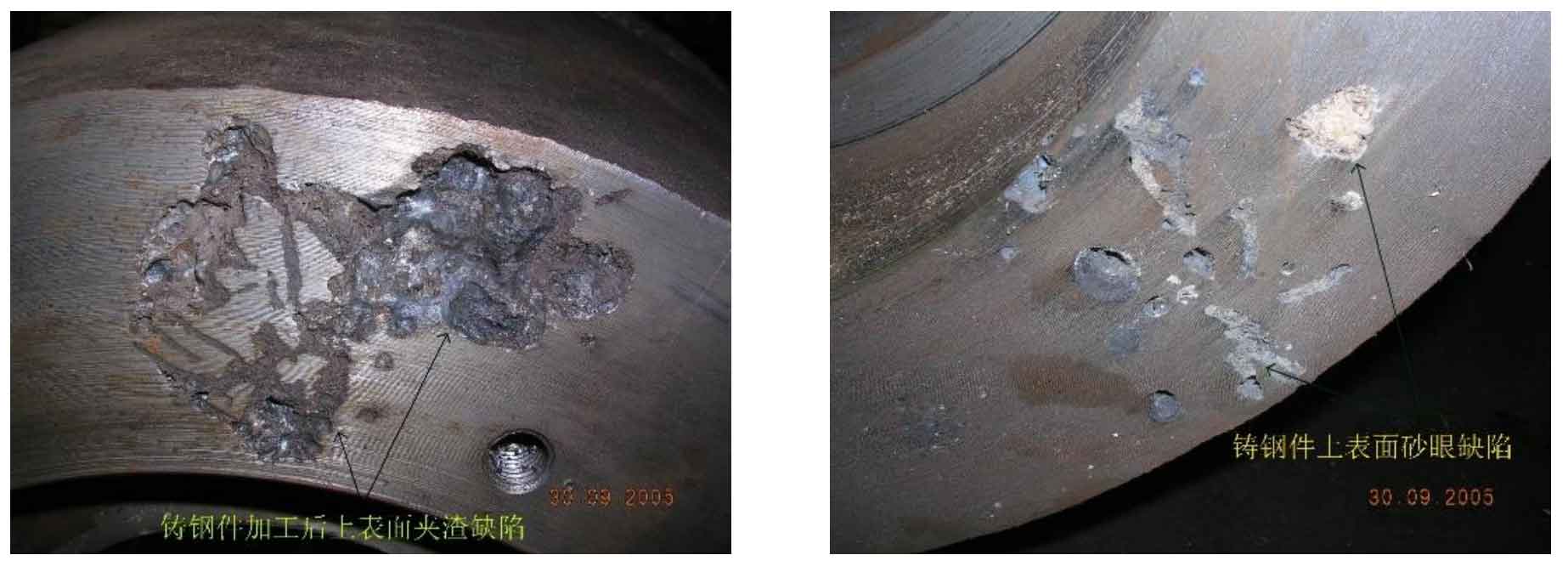
1. Product Structure Analysis and Technical Requirements
Machine tool tray castings are important components of numerical control machine tools, having a significant impact on the dimensional stability and processing accuracy of the machine tools. Some machine tool tray castings are exposed during use, and there are high requirements for their surface quality. Machine tool tray castings are typically thick and heavy, with wall thicknesses of over 100 mm, leading to slow solidification. Their surfaces are prone to slag formation, which initially forms in small amounts but can easily aggregate into larger pieces and adhere to the casting surface, especially in corners, grooves, and other areas. The generation of this slag is closely related to the gating system process, sand mold quality, and coating effectiveness.
Table 1: Product Specifications and Technical Requirements
Product Dimension | Approximate Outer Dimensions | 800 mm × 800 mm × 200 mm |
---|---|---|
Product Weight | Single Weight | 700 kg |
Material | Material Grade | HT300 |
Technical Requirements | Surface Quality | No casting defects such as pores, sand holes, or slag holes after processing |
2. Casting Defect Issues
During production, we found that every product’s upper surface had some slag holes, inclusions, and other defects, affecting the casting’s appearance quality and customer installation effects. Customers suggested continuous improvement, but we hadn’t achieved satisfactory results.
3. Casting Process Analysis
3.1 Casting Process Plan
Our company uses furan self-hardening resin sand technology for production, with pattern plate molding, one mold for one piece. The gating system consists of a φ60 mm ceramic tube for the sprue, trapezoidal runner dimensions of 40 mm (upper), 50 mm (lower), and 50 mm (height), and six ingates with dimensions of 60 mm (width) and 7 mm (thickness). The cross-sectional ratio of the gating system is sprue: runner: ingate = 1:1.8:1.2, semi-closed, with two 100 mm × 100 mm × 22 mm, 20 PPI filters placed on the runner.
3.2 Casting Process Simulation Analysis
We used AnyCasting numerical simulation software to analyze the filling, gas entrapment, and slag entrainment in the process to identify the cause of the issue.
The existing gating system is semi-closed. Through AnyCasting numerical simulation analysis, it can be clearly seen that when the molten iron enters the mold cavity, turbulence and gas entrapment are evident, leading to severe oxidation of the molten iron and the formation of secondary oxide inclusions. These inclusions will rise with the molten iron, causing slag defects on the sidewalls and upper planes. During ascent, the slag aggregates into larger pieces or dispersed on the casting surface, forming slag hole defects, sometimes leading to casting scrap.
4. Process Optimization and Improvement Results
Based on the analysis, we implemented the following optimizations and improvements.
4.1 Optimization of Gating System
We optimized the gating system from semi-closed to open, reducing the inlet velocity and pressure, allowing the molten iron to rise smoothly and slowly in the filling process, minimizing splashing in the mold cavity and eliminating turbulence, reducing secondary slag generation. We also optimized the filter’s slag-removing structure, placing the runner in the lower box and changing the ingate size from 60 mm × 7 mm to 100 mm × 10 mm, with the other dimensions unchanged. The cross-sectional ratio of the gating system was adjusted to sprue: runner: ingate = 1:0.75:0.47.
Table 2: Comparison of Original and Optimized Gating Systems
Gating System Characteristics | Original System | Optimized System |
---|---|---|
Type | Semi-Closed | Open |
Sprue Dimension | φ60 mm | φ60 mm |
Runner Dimension | Upper: 40 mm, Lower: 50 mm, Height: 50 mm | Adjusted as needed for open system |
Ingate Dimension | 60 mm × 7 mm | 100 mm × 10 mm |
Cross-Sectional Ratio | Sprue: Runner: Ingate = 1:1.8:1.2 | Sprue: Runner: Ingate = 1:0.75:0.47 |
Using AnyCasting numerical simulation software to analyze the optimized process, it was evident that the molten iron entered the mold cavity smoothly without significant turbulence or gas entrapment. This led to fewer secondary oxide inclusions during the filling and rising process, with smaller and dispersed oxide inclusions. The optimized pouring process showed significant improvement compared to the original process.
4.2 Pouring According to the Optimized Process
The melting process remained unchanged. After shot blasting inspection, the defects were less numerous and smaller. Although the slag defects improved compared to before, they hadn’t reached the ideal state, with some slag aggregation still present.
Changing the gating system alone couldn’t fully achieve the desired effect. We discussed the defect causes with casting experts from Foscor and analyzed them based on our existing production conditions. The slag defects mainly consisted of oxides and sulfides containing Ba, Ca, etc., sourced from the silicocalcium-barium inoculant we used. The sulfur content in the reclaimed sand was around 0.2%, slightly higher. To meet the production schedule and molding requirements, we selected a low-acidity curing agent with an addition rate controlled at about 45% to reduce the sulfur content in the reclaimed sand. We also switched from silicocalcium-barium inoculant to ferrosilicon inoculant, maintaining the same addition rate, controlling the elements like Ba, Ca, and S introduced by raw materials and inoculants that could react with molten iron to produce slag.
The product is thick and heavy, with slow solidification of molten iron. The mold undergoes long-term high-temperature baking, testing the coating’s high-temperature resistance and oxidation resistance. Ordinary cast iron coatings are ineffective. We recommended using an anti-oxidation and anti-sulfur infiltration coating to prevent sulfur infiltration in the mold and reduce molten iron oxidation, thereby reducing the production of slag and oxides.
4.3 Trial Production After Process Optimization
Following the re-optimized process, we conducted a trial production. After shot blasting inspection, the slag hole defects significantly decreased, with a cleaner surface and no large slag holes. The improvement effect was ideal.
We conducted multiple small-batch production verifications in similar products. The slag hole defects in castings significantly decreased, and the scrap rate greatly dropped. This issue was well resolved, and we have now formed batch supplies.
5. Conclusion
(1) The design of the gating system is crucial. An appropriate gating system for different product structures can effectively avoid slag, ensuring smooth molten iron flow during filling and preventing turbulence, thereby reducing casting defects.
(2) Numerical simulation technology can analyze the feasibility of the casting process, reference its simulation results, analyze the process rationality, and optimize and improve it to reduce potential production issues and casting defects, enhancing product quality.
(3) The choice of coating is also essential for different product structures and production processes. Suitable coatings can help reduce casting defects, improve product quality, and decrease the scrap rate.