This paper focuses on the structural characteristics and technical difficulties in the casting process of titanium alloy brush boxes. Based on an analysis of the causes of defects in titanium alloy brush box castings, a casting process method for high-strength, low-stress titanium alloy brush boxes is explored and studied. Through production verification, the casting process method developed in this study is proven to be successful and effective, providing guidance for titanium alloy casting of similar parts.
1. Introduction
Brush boxes are crucial components in generators, operating in harsh environments. They must not only be corrosion-resistant but also lightweight, with high dimensional accuracy and excellent mechanical properties. This paper takes the titanium alloy brush box used in a new type of generator produced by our company as an example to introduce the structural characteristics and technical requirements of titanium alloy brush boxes. It analyzes the technical difficulties in the casting process and proposes a new casting process design scheme along with multiple process measures to address casting defects. These ensure the successful casting of this new type of titanium alloy brush box, improve productivity, reduce production costs, and provide a reference for the casting of similar titanium parts.
2. Structural Characteristics and Casting Process Difficulties
2.1 Structural Characteristics and Technical Requirements
The titanium alloy brush box has dimensions of 238mm x 33mm x 70mm, with a part weight of approximately 0.74kg. The basic wall thickness of the part is 3.5mm, and the minimum wall thickness of the brush box is 1mm. The dimensional accuracy of the casting requires achieving grades CT6 to CT7 according to GB/T 6414. Its characteristics include a slender overall shape, small gaps between partitions, and complex structure, as shown in Figure 1.
The material of the brush box casting is TC4 alloy, with tensile strength ≥ 890MPa, yield strength ≥ 820MPa, elongation after fracture ≥ 5%, and reduction of area ≥ 10%. The product is delivered after precision machining.
2.2 Analysis of Casting Process Difficulties
The thin wall thickness of the brush box casting, with a minimum wall thickness of 1mm, poses difficulties in gravity pouring and filling, with a risk of incomplete filling. The slender shape of the part leads to a risk of deformation in the castings. The gaps between partitions are 1.5mm, making shell molding difficult. The slender cores have low strength, prone to deformation and fracture. Enclosed by molten metal, the cores are susceptible to “fire running” phenomena, making cleanup difficult, which can lead to clogging of partition gaps and scrapping of the casting. The casting process is challenging.
3. Casting Process Design Scheme
Due to the complex structure of the brush box, titanium investment casting is adopted for production. To successfully pour the brush box casting, two schemes are designed.
3.1 Scheme One
The brush box is directly connected to the sprue, with the direction pointing vertically upward. Only a riser and vent holes are set at the upper end of the brush box, and reinforcing ribs are set at weak parts of the casting to prevent deformation, as shown in Figure 2. This scheme has a short metal flow path, allowing the molten metal to enter the mold shell smoothly with strong filling capability, good surface quality of the casting, and a high yield rate of 45%.
3.2 Scheme Two
To improve filling capability, the top-pouring method is adopted for pouring. The advantages of this gating system are: simple and compact structure, easy modeling, metal conservation; the metal can easily fill the mold cavity, with the metal temperature being higher at the top and lower at the bottom, which is conducive to the riser’s role in feeding and compensating for shrinkage during casting, preventing defects such as misruns and cold shuts in thin-walled castings.
The brush boxes are placed side by side at the bottom, connected to the sprue through an H-shaped cross gate. The cross gate not only serves as a channel for molten metal to enter the brush box but also acts as a riser for feeding and compensating for shrinkage. The sprue is designed with a conical shape to maximize the smooth entry of titanium liquid into the mold shell. Since titanium is reactive at high temperatures and can react with most refractory materials, reaction-induced porosity is common in titanium castings. To further reduce porosity, vent holes are set at the parts of the brush box prone to porosity, and reinforcing ribs are added to reduce the possibility of deformation in the casting. This scheme has a lower yield rate of only 35%.
4. Simulation Scheme Design
To verify the rationality of the aforementioned gating system designs, this study will conduct numerical simulation of the casting process of the brush box based on the ProCAST software. The 3D models of the two gating schemes are imported into the ProCAST software for preprocessing. The brush box material is set as titanium alloy, the mold shell material as mullite, the contact surface type as COINC, the interfacial heat exchange coefficient as 500W/(m2·°C), the pouring temperature as 1800°C, the pouring speed as 6kg/s, the cooling method as air cooling, the initial mold shell temperature as 25°C, and gravity casting is adopted, with radiation ignored.
5. ProCAST Simulation Results and Analysis
Shrinkage cavities and porosity defects usually occur at positions with slower solidification, known as hot spots. This paper uses ProCAST software to analyze and compare temperature changes in different parts to quickly locate positions where shrinkage cavities and porosity defects may occur in the casting.
shows the changes in the temperature field during the solidification process of the casting in Scheme One at different simulation times. It can be seen that at the beginning of solidification, the casting solidifies rapidly, while the middle runner solidifies slowly. Almost the entire casting solidifies simultaneously, with a small temperature difference, reducing the likelihood of stress, deformation, and hot tearing. There is no feeding riser set on the casting, saving metal and simplifying the process. The vent holes are set at the top of the casting, facilitating gas expulsion. The disadvantage is that the area where the casting connects to the sprue solidifies slowly, prone to shrinkage cavities or porosity defects, resulting in less dense structure. Figure 5 shows the casting simulation results, with defects appearing in areas with slow cooling, and shrinkage porosity defects also appearing on the brush box body.
shows the changes in the temperature field during the solidification process of the casting in Scheme Two at different simulation times. It can be seen that at the beginning of solidification, the casting solidifies gradually from bottom to top, with a solidification time of 12.9s. The cross gate can feed the casting, providing good feeding results and obtaining a dense casting without shrinkage cavities. Liquid metal mainly concentrates in the sprue and cross gate. The solidification time of the cross gate is 822s, providing sufficient time for feeding and compensating for shrinkage of the connected casting, reducing the occurrence of shrinkage cavities and porosity, and obtaining a dense casting without shrinkage cavities. The vent holes are located at the top of the casting, facilitating gas expulsion. Figure 7 shows the casting simulation results, with defects mostly appearing in the gating system, and only a few defects on the brush box body, indicating a reasonable gating scheme.
Improvements were made to Scheme Two by adding risers at locations prone to defects and adding thermal insulation wool at the sprue and cross gate positions to further enhance sequential solidification characteristics. The improved gating scheme (Scheme Two) was simulated again, with simulation results shown.
“…have revolutionized numerous industries, from healthcare to finance, by enabling more accurate predictions, efficient data analysis, and seamless automation. In healthcare, AI algorithms assist doctors in diagnosing diseases with remarkable accuracy, often surpassing human capabilities in detecting early signs of illnesses. By analyzing vast amounts of medical data, AI can predict patient outcomes, personalize treatment plans, and even facilitate drug discovery.
In the financial sector, AI-driven systems enhance fraud detection, credit scoring, and algorithmic trading, leading to increased security and profitability. They process transactions in real-time, identifying patterns and anomalies that might indicate fraudulent activities. Additionally, AI-powered chatbots and virtual assistants provide round-the-clock customer support, improving customer satisfaction and operational efficiency.
Moreover, the integration of AI in education has transformed learning experiences. Personalized learning platforms leverage AI to tailor educational content to individual student needs, adapting to different learning styles and paces. This not only enhances engagement but also boosts academic performance. AI-driven analytics further help educators assess student progress, identify learning gaps, and make informed decisions about teaching strategies.
The retail industry has also benefited immensely from AI. From personalized shopping recommendations to inventory management and predictive analytics, AI optimizes the retail experience for both consumers and businesses. By analyzing customer behavior and preferences, retailers can forecast demand, streamline supply chains, and reduce waste. This, in turn, leads to increased customer satisfaction and loyalty.
However, despite these remarkable achievements, the deployment of AI also poses significant challenges and ethical considerations. Issues such as bias in AI algorithms, privacy concerns, and the potential displacement of human labor are critical areas of concern. Ensuring fairness, transparency, and accountability in AI systems is paramount to fostering trust and ethical use of these technologies.
In conclusion, the evolution of artificial intelligence continues to reshape our world in profound ways, offering immense opportunities for innovation and efficiency. As we navigate this exciting yet complex landscape, it is crucial to address the ethical and societal implications of AI, ensuring that its benefits are shared equitably and its use aligns with human values and aspirations.”
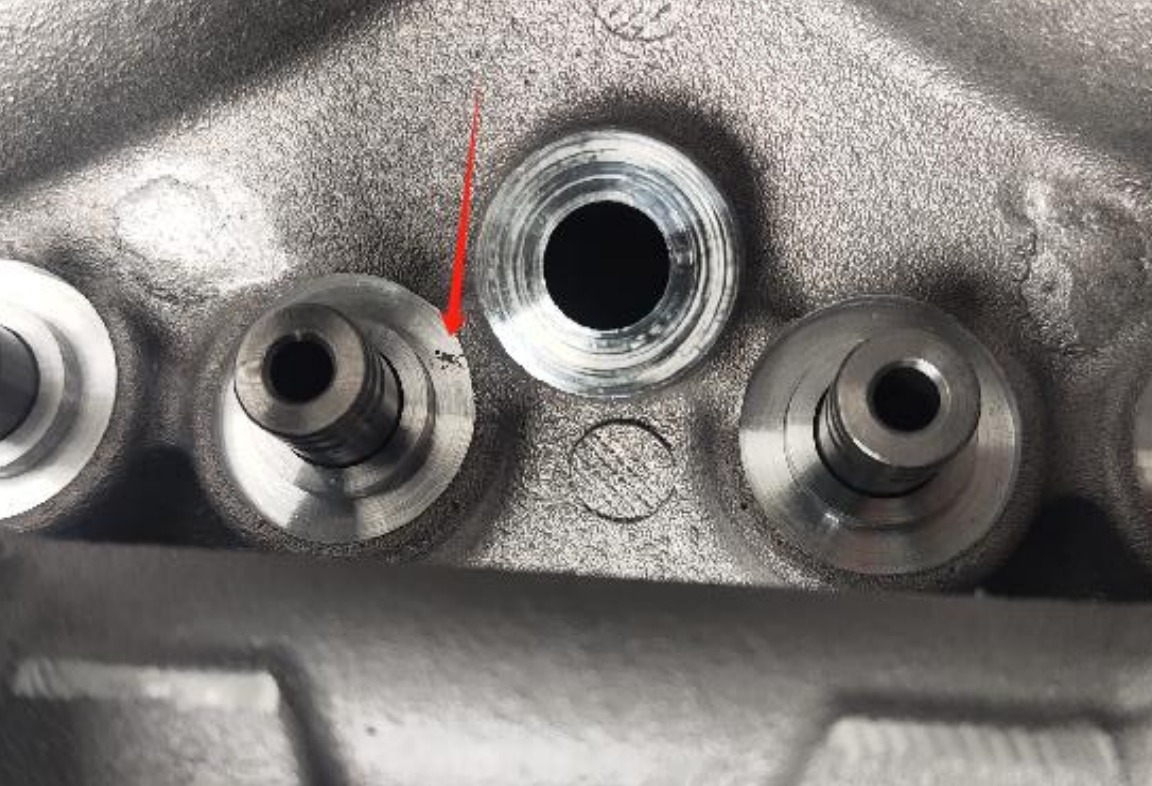