Nodular cast iron (ductile iron for short) is the 50th century A kind of high strength cast iron developed in the S. after spheroidizing and inoculation, carbon atoms precipitate in the form of spheroidal graphite and are evenly distributed in the middle of ferrite structure (Fig. 1), which can effectively improve the mechanical properties of cast iron, especially the plasticity and toughness of collective structure, so as to obtain higher strength than carbon steel.
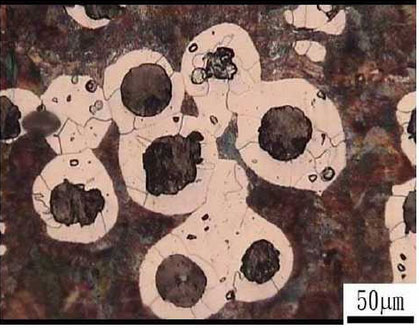
In recent years, with the improvement of production automation, the application of ductile iron has been developed rapidly, which plays an important role in the field of automobile industry. It is mainly used to manufacture automobile engine, gearbox and chassis related parts.
Nodular cast iron is “paste” solidified. Compared with gray cast iron, the eutectic solidification temperature range is wide, the number of eutectic clusters is more, and the solidification expansion pressure is higher. The composition of nodular cast iron is near the eutectic point, and its solidification characteristics are determined by the way of eutectic growth. During eutectic crystallization, the Mg content in the eutectic phase is higher than that in the eutectic phase As a result of element spheroidization, the core of graphite ball grows to a certain size in liquid phase and is surrounded by austenite. The free carbon atoms can only diffuse through austenite to make graphite grow. As a result, the growth rate is slow. Besides the existing eutectic head, the completion of eutectic reaction also depends on the precipitation of new crystal nucleus. Therefore, the eutectic transformation is in a wide temperature range and castings The results show that the solid and liquid phases coexist in a wide section for a long time.
Because the specific volume of graphite is greater than that of molten iron, with the increasing and growing of graphite balls, the volume of graphite balls expands due to the release of solidification latent heat. The graphite grows under the enclosure of austenite shell. After the austenite shells contact each other, the volume expansion caused by graphite growth is hindered, and the final expansion force will be transferred to the surface of casting, resulting in volume change.