Figure 1 shows the solidification process of the hot spot of nodular iron nuclear spent fuel container under the conditions of sand mold chill process and full chill process. According to the analysis of figure 5-4, due to the poor heat dissipation condition of sand mold, slow heat transfer and slow solidification of hot spot, the solidification time of nodular iron spent fuel container under sand mold chill process is about 8.5H; the solidification speed of body is fast under the action of metal mold, and the solidification is completed earlier, and the temperature field between hot spot and body is quite different; the temperature field of top full chill is relatively low The solidification time of nodular iron spent fuel container with 300 mm full chill process is 4.5 H.
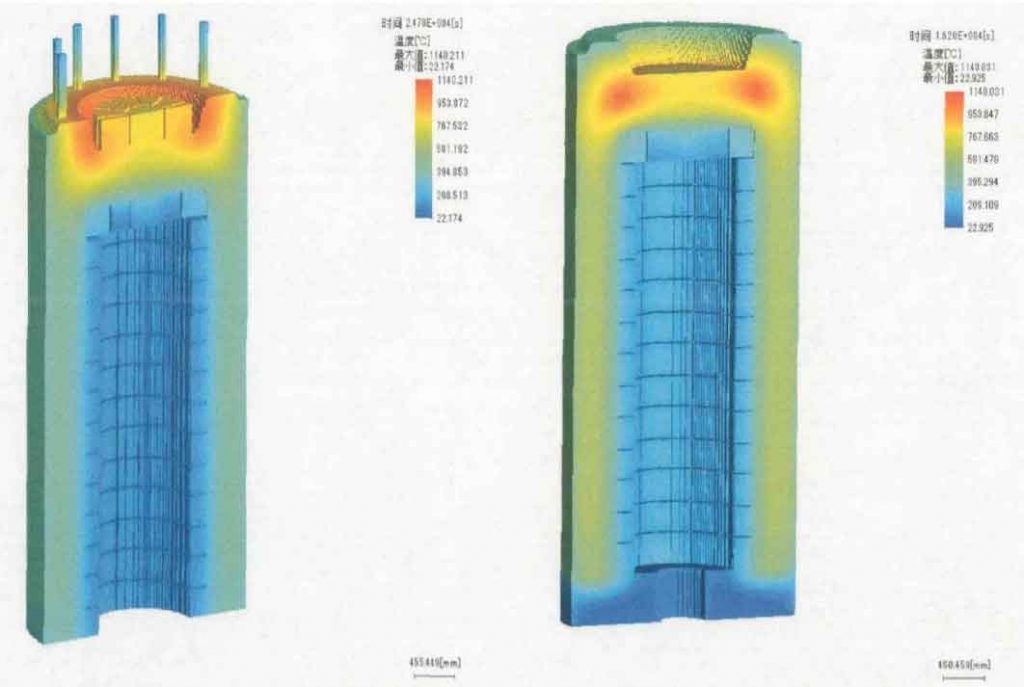
(1) 300 metal mold + 300 mm sand mold chill (2) 300 mm metal mold + 300 mm full chill
In order to understand the solidification characteristics of nodular iron nuclear spent fuel container under sand mold chill process and full chill process, the solidification temperature field is analyzed, as shown in Figure 2.
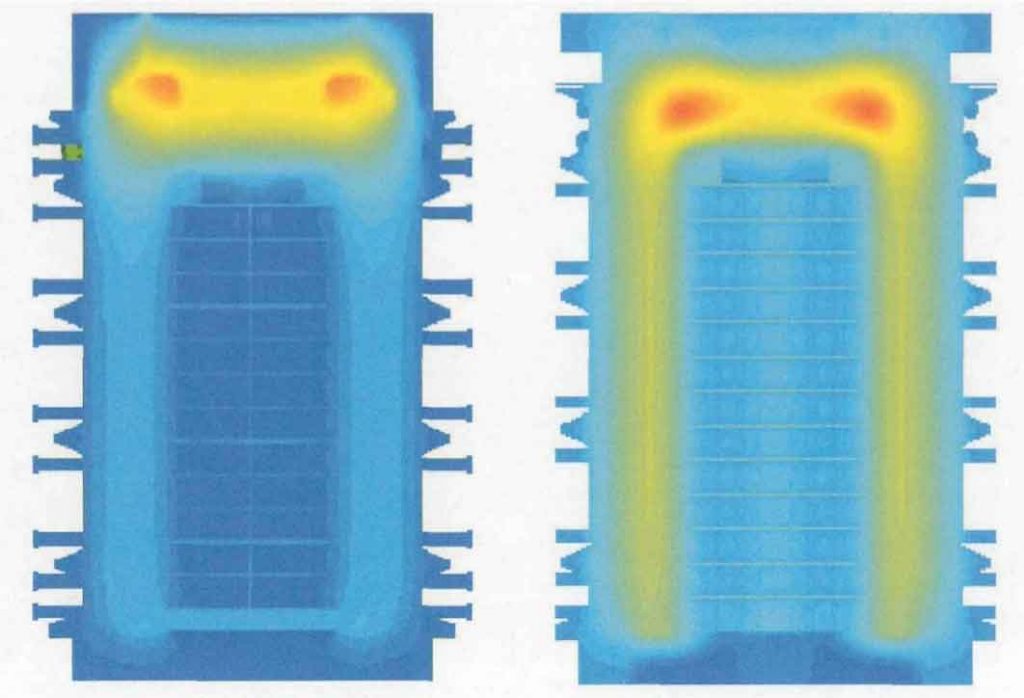
According to figure 2, under the sand mold chill process, the solidification speed of the body part of the nodular iron nuclear spent fuel container is faster than that of the hot spot part, and the solidification temperature field of the hot spot part and the body part is isolated from each other; under the condition of full chill casting process, the cooling capacity of the hot spot part on the top of the nodular iron nuclear spent fuel container is significantly enhanced, the heat dissipation condition at the hot spot is significantly improved, and the solidification speed is significantly improved With the increase of temperature, the hot spot area moves inward, the hot spot area decreases, and the temperature field distribution of the body and the top hot spot is more coordinated.
The results show that the 300 mm full chill process can accelerate the solidification rate of the hot spot and reduce the hot spot area, but the solidification time is slightly longer; when the metal mold thickness and full chill thickness of the hot spot continue to increase to 450 mm, the solidification rate of the hot spot on the top of the nodular iron spent fuel container increases with the increase of the thickness of the cold iron and metal mold, and the nodular iron spent fuel container is stable The solidification speed of the container is obviously accelerated, and the solidification time is shortened to 3.5H, as shown in Fig. 3. When the thickness of full chill iron and metal mold at the hot spot continues to increase to 500mm, the solidification time of the ductile iron spent fuel container has no obvious change.
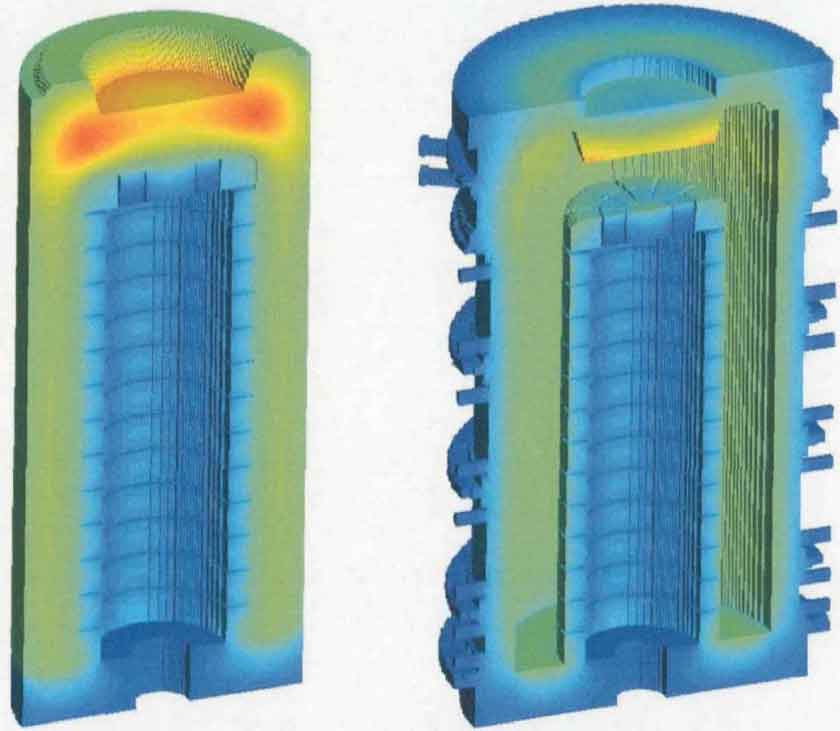
(1) Casting temperature field (2) mold temperature field
The solidification time of nodular iron spent fuel container hot spot under different processes was counted. The solidification time of nodular iron spent fuel container hot spot under different casting process is plotted and fitted, as shown in Figure 4. It can be seen that:
(1) At the same solidification ratio, the time of full chill process is less than that of sand chill process, and the effect of full chill process on accelerating the solidification of ductile iron nuclear spent fuel container is significant;
(2) The results show that the solidification time of ductile iron spent fuel container is the shortest, which is 3.5H;
(3) When the total chill thickness is more than 450mm, increasing the total chill thickness can not shorten the solidification time of ductile iron nuclear spent fuel container.
To sum up, 300 mm metal mold + 300 mm chill process is adopted for the body of the spent fuel container, and 450 mm metal mold + 450 mm full chill process is adopted for the top hot spot. By adopting the above process, the solidification temperature field of the body part and the hot spot part of the ductile iron spent fuel container can be coordinated, and the consistency of the structure and performance of the ductile iron spent fuel container can be ensured.