Figures 1 and 2 show Fe Ti binary phase diagram and N Ti binary phase diagram respectively. The maximum solid solubility of Ti in cast iron is 6%, and a considerable amount of Ti will be dissolved in the solidification process of molten iron. Tin is similar to NaCl in structure, which is of face and cubic structure. The Ti atom is located at the top of the corner of the face and cube, and the N atom is at the gap. Generally, the tin is a non stoichiometric compound with the composition of tin0.6-1.16. Because the lattice constants of tin, tic and TiO are relatively close, the N atom in tin is often replaced by C atom and O atom in any proportion to form a solid solution. Its chemical formula is Ti (cxn1-x). However, because the value of X is small, we collectively call it tin in this paper.
Tin crystal is yellow and has metallic luster. Due to the change of component content, its color is also dispersed to a certain extent. The soldering point of tin is 322, and the density is 5.43-5.44g / cm3, the Mohs hardness is 8-9, and the chemical stability is good.

Most of tin in grey cast iron comes from casting raw materials. As the main raw materials for smelting grey cast iron, scrap steel, pig iron and recycled materials contain a certain amount of tin inclusion or a part of Ti element of solid solution, as shown in Table 1. The composition control of grey cast iron production is shown in Table 2. Figure 3 shows the distribution of tin inclusion phase particles in scrap. The arrow in the figure indicates tin particles. The size of tin particles in scrap is about 2-4 μ m. The shape is mostly regular quadrilateral, and the black matter in the necessary part of the cross section of tin particles is the heterogeneous core of its nucleation and growth.
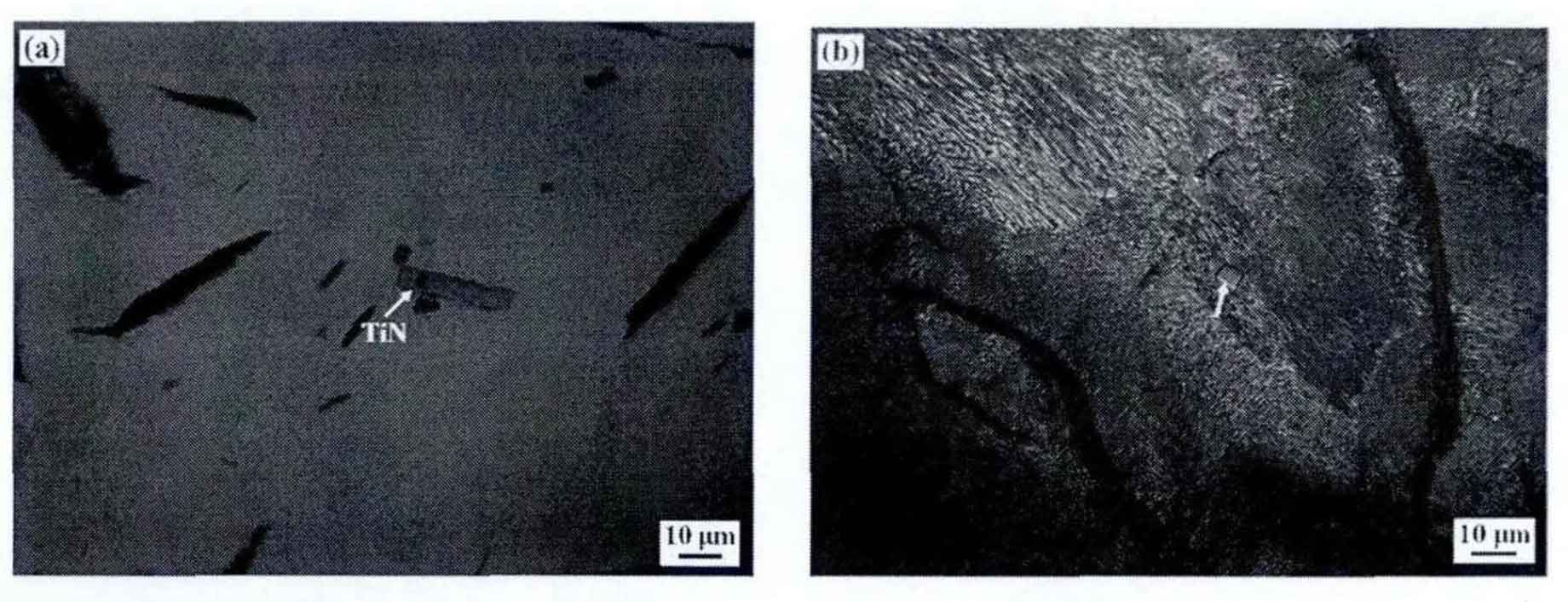
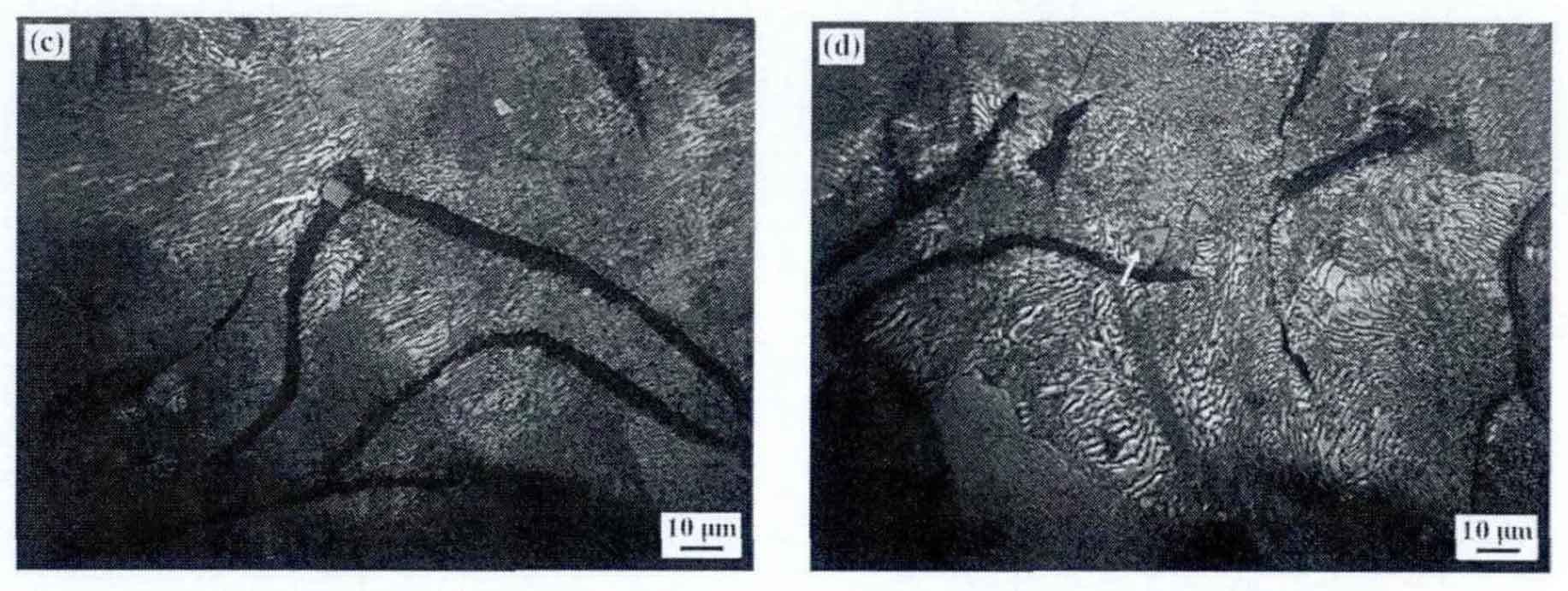
The microstructure analysis of gray iron castings shows that compared with tin in scrap, the size of gray iron castings is relatively large and mainly distributed in pearlite. Figure 4 shows the cross-sectional morphology and distribution of tin inclusions in gray cast iron. Figure 4 (a) shows the larger sized particles, whose length is measured to be 23.5 μ m 。 This kind of tin inclusion phase is mainly due to the existence of tin particles with slightly larger size during the remelting process of raw materials such as reheated materials and scrap, which are not completely pyrolytic and diffused during the remelting process. Therefore, during the solidification of molten iron, the Ti and n elements in molten iron will adhere to these larger tin particles to aggregate and grow. Therefore, we call the category by category phenomenon the heritability of tin. In addition, the tin particle size of more than 70% in the gray cast iron sample is relatively small (about 4-8 μ m) (Fig. 4 (b) and (d)), in Fig. 4 (c) and (d), tin particles grown close to graphite or with other inclusion phases as the core appear. Among them, in Figure 4 (c), tin particles growing close to graphite play a double-sided role in gray cast iron. On the one hand, they can serve as active particles for graphite nucleation and growth, providing a nucleation core for the nucleation process of graphite. On the other hand, it consumes and blocks the diffusion of C element in molten iron, so that the graphite sheet can not grow further, which plays a role in refining. From the above analysis, it can be seen that the tin size and distribution in gray cast iron are different, and its nucleation and growth mechanism are also different.