Spheroidal Graphite Iron (SGI), also known as ductile iron or nodular iron, is a type of cast iron that has revolutionized the manufacturing industry with its exceptional combination of strength, durability, and lightweight properties. Spheroidal Graphite Iron is formed by adding magnesium to molten iron, which causes graphite to form in a spherical or nodular shape rather than the flake-like structure found in traditional cast iron.
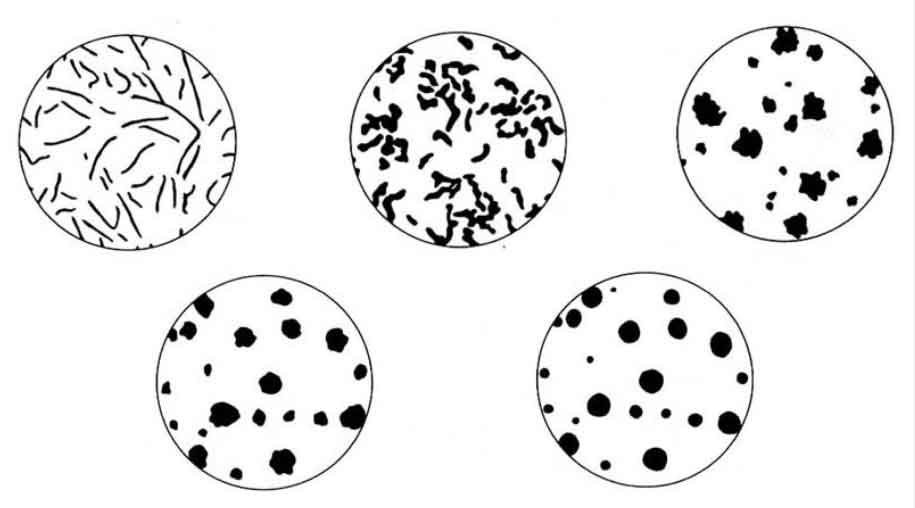
The unique microstructure of Spheroidal Graphite Iron gives it several advantages over other types of iron and even some steel alloys. Here are some key reasons why Spheroidal Graphite Iron is redefining the future of durable and lightweight iron components:
- High Strength: Spheroidal Graphite Iron possesses excellent mechanical strength, making it stronger than traditional cast iron and comparable to low to medium carbon steels. Its tensile strength can reach up to 700 MPa, allowing for the production of components that can withstand heavy loads and high-stress environments.
- Ductility and Toughness: Unlike conventional cast iron, Spheroidal Graphite Iron exhibits high ductility and toughness, making it less brittle and more resistant to cracking or fracturing. It can absorb more energy before failure, making it suitable for applications requiring impact resistance.
- Lightweight: Spheroidal Graphite Iron offers a remarkable strength-to-weight ratio, making it significantly lighter than many other materials with similar strength properties. This makes it an ideal choice for applications that require reduced weight without sacrificing structural integrity, such as automotive components.
- Fatigue Resistance: Spheroidal Graphite Iron has superior fatigue resistance compared to conventional cast iron, making it highly suitable for components subjected to cyclic loading or prolonged stress. Its ability to withstand repeated stress without failure makes it an excellent choice for critical parts in various industries, including automotive, aerospace, and machinery.
- Machinability: Spheroidal Graphite Iron is known for its good machinability, allowing for easier production of complex shapes and precision components. It can be easily cast into intricate designs, making it a versatile material for various applications.
- Corrosion Resistance: Spheroidal Graphite Iron exhibits better corrosion resistance than standard cast iron due to its graphite nodules, which act as barriers against corrosive agents. However, it is important to note that Spheroidal Graphite Iron still requires proper protective coatings or surface treatments in highly corrosive environments.
- Cost-Effectiveness: Spheroidal Graphite Iron provides an attractive balance between performance and cost. While it may be more expensive than conventional cast iron, it offers significant advantages over other materials like steel, aluminum, or titanium. Its cost-effectiveness, combined with its superior properties, makes it a preferred choice for many engineering applications.
Due to its outstanding properties, Spheroidal Graphite Iron is widely used in various industries, including automotive, heavy machinery, energy, agriculture, and more. It can be found in engine blocks, crankshafts, suspension components, gears, valves, and many other critical parts where a combination of strength, durability, and lightweight characteristics is required.
Spheroidal Graphite Iron is redefining the future of durable and lightweight iron components by offering an excellent balance of strength, ductility, toughness, and weight reduction. Its unique properties make it an ideal choice for demanding applications, enabling manufacturers to create innovative designs that optimize performance and efficiency.