At present, the theoretical analysis method of squeeze casting is not very perfect. There is no ideal design method of extrusion process parameters at home and abroad. Theoretically, the extrusion force is related to various casting parameters, such as material, overall dimension, density, forming process and other objective factors. Therefore, this index is mainly determined by experimental research and theoretical calculation. Among them, the experimental research is mainly aimed at different materials such as aluminum alloy, copper alloy, magnesium alloy, zinc alloy, steel and composite matrix materials to study the influence of squeeze casting process parameters on mechanical properties and microstructure. For example, S. souissi et al. Have studied the direct squeeze casting of Al – 13%si alloy. It is concluded that increasing the specific pressure from 10MPa to 100MPa can significantly improve the microstructure, tensile strength and hardness of products; When the specific pressure is 100mpa-150mpa, the alloy is severely deformed at high temperature, resulting in coarse microstructure, which reduces the tensile strength and hardness. H. Khodaverdizadeh et al. Studied the specific pressure of direct squeeze casting of nodular cast iron, and concluded that when the pressure increased from 0mpa to 75mpa, the sample with the best comprehensive mechanical properties was obtained when the specific pressure was 50MPa. Lirunxia studied the specific pressure of ZA27 alloy in direct squeeze casting. Zhang Ming et al. Analyzed the effect of specific pressure on the microstructure and properties of Al Cu alloy extruded castings. The optimum specific pressure of different materials and direct squeeze casting obtained from the experiment is shown in the table, which can be used as a reference for the design of composite extrusion equipment for large parts.
Material Science | Main components | Mold filling temperature | Mold temperature | Optimum specific pressure |
Al–13%Si | 13.1wt.% Si Rest Al | 750°C | 250°C | <100Mpa |
Al-Cu | 3.2-4.5 wt.% Cu 0.5-1.0 wt.% Mg 0.05-0.8wt.% Mn | 730°C | 200°C | 50Mpa |
Ductile iron | 3.65wt.% C 2.24wt.% Si 0.46wt.% Mn Balance Fe | —— | 400°C | 50Mpa |
At the same time, the theoretical or empirical calculation formula for specific pressure or pressure holding of squeeze casting is studied. For example, chenbingguang has established an empirical formula for calculating squeeze pressure. As shown in the formula, h is the height of the casting, a is the average thickness corresponding to the H part, and K1 and K2 are the coefficients selected according to different metal materials and extrusion methods. It is introduced that the empirical formula has a large error in engineering application.
Luoshoujing et al. Based on the principle of metal plastic forming, assuming that there is no gap between the plastic body and the die, and that the liquid metal does not bear isostatic pressure throughout the squeeze casting process due to the existence of shrinkage cavity, obtained the formula of the required extrusion critical pressure, as shown in the formula, where σ S is the critical deformation stress of the plastic body interception element, μ Is the friction coefficient between the plastic body and the mold, R0 is the outer diameter of the annular plastic body, R0 is the inner diameter of the annular plastic body, and H is the height of the casting.
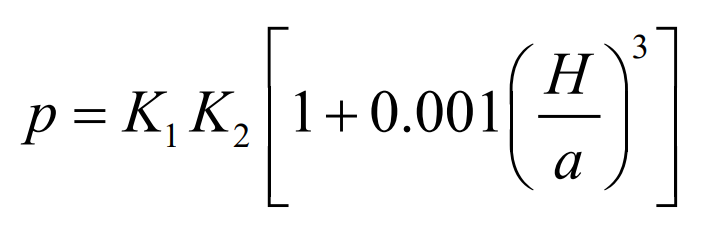
Since R0 and R are variables that cannot be determined, and the formula artificially divides the solidification process of squeeze casting into three independent regions that are different from the actual situation: liquid phase, solid-liquid composite phase and solid-semi-solid-liquid composite phase, and does not consider the influence of extrusion temperature and speed on deformation, the formula is also quite different from the actual situation.
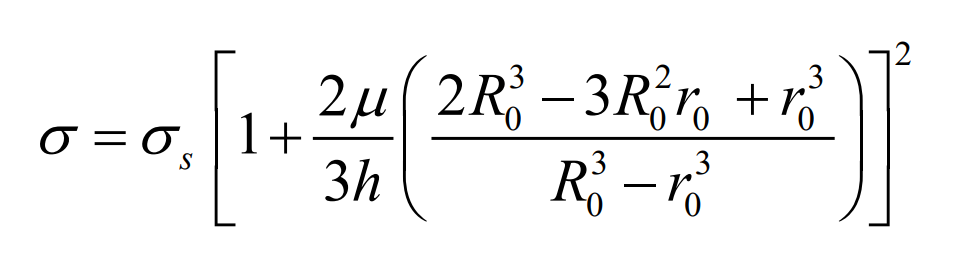
According to Clausius Clapeyron equation, vijian et al. Also put forward a rough formula for calculating the extrusion pressure, where TF is the equilibrium solidification temperature, LF is the latent heat of solidification, P0 and R should be estimated according to the experiment.
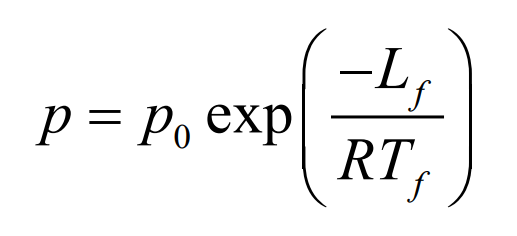
At present, there is no recognized and exact expression in various theoretical analysis methods. Experiments and theoretical calculations are based on simple parts, without considering the influence of the complexity of the parts on the process parameters. At the same time, the calculation formula also less considers the influence of different process parameters, ignoring the coupling relationship between various parameters, such as the increase of extrusion pressure will increase the heat flux and affect the solidification time.