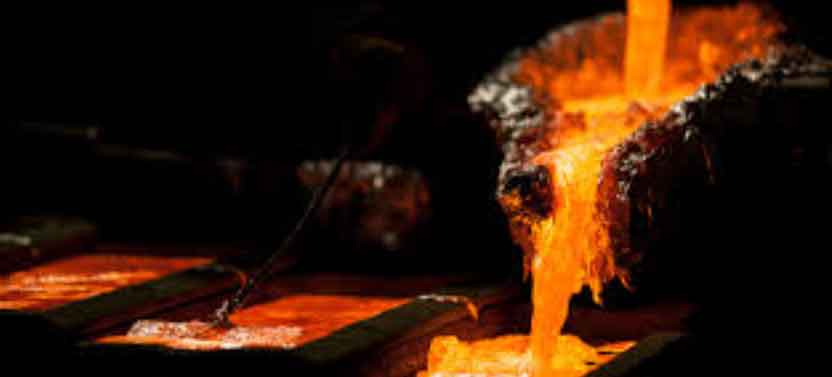
Steel casting offers numerous advantages, finds applications across various industries, and utilizes different manufacturing techniques to produce high-quality metal components. Let’s explore these aspects in detail:
Advantages of Steel Casting:
- Strength and Durability: Steel castings exhibit exceptional strength, toughness, and durability, making them suitable for demanding applications that require high performance and resistance to wear, corrosion, and heat.
- Design Flexibility: Steel casting allows for complex shapes, intricate details, and precise dimensions, offering design flexibility to engineers. It enables the production of components with internal features, undercuts, thin walls, and complex geometries that may be challenging to achieve through other manufacturing methods.
- Wide Material Range: Steel casting offers a wide range of steel alloys with varying properties, enabling engineers to select the most suitable material for the desired application. Different steel grades can be chosen based on mechanical properties, corrosion resistance, heat resistance, and other specific requirements.
- Cost-Effectiveness: Steel casting provides cost-effective solutions for producing high-quality metal components. It minimizes material waste by utilizing close-to-final shape casting, reducing the need for extensive machining operations. Additionally, steel castings have a long service life, reducing replacement and maintenance costs.
- Size Range: Steel casting can produce both small precision components and large-scale structures. It offers versatility in manufacturing components of various sizes, from intricate parts to heavy-duty machinery components or industrial equipment.
- Consistency and Reproducibility: Steel casting ensures consistent production of high-quality components with uniform mechanical properties, dimensional accuracy, and surface finish. This is crucial for industries that require a high level of consistency and reliability, such as automotive and aerospace.
- Integration with Other Processes: Steel casting can be seamlessly integrated with other manufacturing processes, including heat treatment, machining, and surface finishing. This allows for the production of fully finished, ready-to-use components.
Applications of Steel Casting:
- Automotive Industry: Steel castings are used in the manufacturing of engine blocks, cylinder heads, transmission components, steering system parts, suspension components, and other critical automotive components.
- Aerospace Industry: Steel castings find applications in the production of aircraft engine parts, landing gear components, structural elements, and other critical aerospace components that require high strength, durability, and precision.
- Energy Sector: Steel castings are utilized in power generation plants, including turbine components, boiler parts, and valves. They are also used in oil and gas applications, such as drill bits, pipe fittings, and offshore platform equipment.
- Industrial Machinery: Steel castings are employed in the manufacturing of heavy machinery components, including machine bases, gearboxes, pump housings, and hydraulic system parts.
- Construction and Infrastructure: Steel castings are used in construction and infrastructure projects for components such as bridge components, building frameworks, architectural elements, and ornamental fixtures.
- Mining and Earthmoving Equipment: Steel castings are employed in the production of mining equipment, including crusher parts, bucket teeth, and wear-resistant components for excavators, loaders, and draglines.
- Railway Industry: Steel castings are used in the manufacturing of railway components such as couplers, bogie frames, brake systems, and other critical parts.
Manufacturing Techniques for Steel Casting:
- Sand Casting: The most common technique, sand casting involves creating a mold using a mixture of sand and a binder. Molten steel is poured into the mold, and after solidification, the casting is removed.
- Investment Casting: Also known as lost-wax casting, this technique involves creating a wax pattern, coating it with a ceramic shell, and then removing the wax through melting. The remaining ceramic shell is filled with molten steel, and once solidified, the shell is broken to retrieve the casting.
- Continuous Casting: In this technique, molten steel is continuously poured into a water-cooled mold, where it solidifies into a continuous strand. This strand is then cut into desired lengths to form steel castings.
- Centrifugal Casting: This method involves rotating a mold filled with molten steel, creating centrifugal force that distributes the metal along the mold’s inner surface. This technique is often used for cylindrical or tubular components such as pipes or rings.
- Shell Molding: In shell molding, a resin-coated sand mixture is heated and formed around a pattern. The mold is then filled with molten steel, and after solidification, the shell mold is broken to retrieve the casting.
Steel casting, with its numerous advantages, wide range of applications, and diverse manufacturing techniques, remains a critical process in the production of strong and durable metal components for various industries.