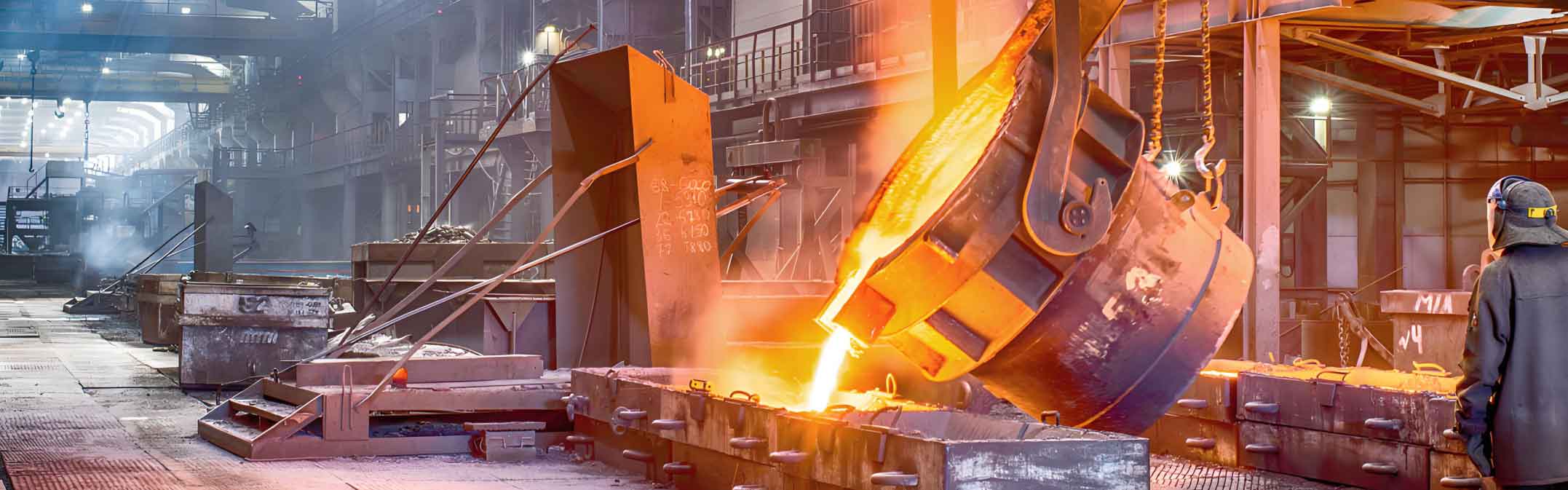
Casting is fundamental process in manufacturing, utilized to create complex and durable components for various industries. Steel casting and iron casting are two primary methods within this process, each offering unique properties and applications. This article provides a comprehensive comparative analysis of steel casting and iron casting, exploring their characteristics, benefits, drawbacks, and applications.
Overview of Steel Casting and Iron Casting
Steel Casting
The steel casting process involves melting steel and pouring it into molds to create components with high strength, durability, and precision. The process includes several stages:
- Raw Material Preparation: Selecting high-quality iron ore and alloys.
- Melting and Refining: Melting the raw materials in furnaces and refining the molten steel.
- Mold Preparation: Creating precise molds from materials like sand or ceramics.
- Pouring and Casting: Pouring molten steel into molds and allowing it to solidify.
- Finishing and Machining: Cleaning, machining, and inspecting the castings.
Iron Casting
The iron casting process involves melting iron, typically pig iron and scrap iron, and pouring it into molds to create components known for their castability and wear resistance. The process includes similar stages to steel casting:
- Raw Material Preparation: Selecting pig iron, scrap iron, and alloys.
- Melting and Refining: Melting the raw materials in furnaces.
- Mold Preparation: Creating molds from sand or other materials.
- Pouring and Casting: Pouring molten iron into molds and allowing it to solidify.
- Finishing and Machining: Cleaning, machining, and inspecting the castings.
Comparative Analysis
Material Properties
Steel Casting:
- Strength: Steel castings offer superior tensile strength, making them ideal for high-stress applications.
- Ductility: Steel castings exhibit excellent ductility, allowing them to deform under stress without breaking.
- Impact Resistance: Steel castings have high impact resistance, suitable for dynamic and heavy load applications.
Iron Casting:
- Castability: Iron castings are known for their excellent castability, allowing for the creation of intricate shapes and thin sections.
- Wear Resistance: Iron castings possess high wear resistance, making them suitable for applications involving friction and abrasion.
- Compressive Strength: Iron castings have high compressive strength, beneficial for load-bearing applications.
Mechanical Properties Comparison Table
Property | Steel Casting | Iron Casting |
---|---|---|
Tensile Strength | High | Moderate |
Ductility | High | Low |
Impact Resistance | High | Moderate |
Castability | Moderate | High |
Wear Resistance | Moderate | High |
Compressive Strength | High | High |
Applications
Steel Casting:
- Automotive Industry: Components such as engine blocks, crankshafts, and suspension parts.
- Aerospace Industry: Critical parts like landing gear and turbine blades.
- Construction Industry: Structural components, machinery parts, and tools.
- Oil and Gas Industry: Valves, pumps, and drilling equipment.
Iron Casting:
- Automotive Industry: Brake drums, engine blocks, and differential housings.
- Machinery and Equipment: Gearboxes, machine tool bases, and agricultural equipment.
- Construction Industry: Manhole covers, pipes, and fittings.
- Railway Industry: Rail tracks, wheels, and couplers.
Advantages and Disadvantages
Steel Casting:
- Advantages:
- High tensile strength and ductility.
- Excellent impact resistance.
- Suitable for high-stress and dynamic applications.
- Disadvantages:
- Higher cost compared to iron casting.
- More complex and energy-intensive process.
- Requires precise control of composition and cooling rates.
Iron Casting:
- Advantages:
- Excellent castability and wear resistance.
- High compressive strength.
- Cost-effective for large-scale production.
- Disadvantages:
- Lower tensile strength and ductility.
- Prone to brittleness and cracking under dynamic loads.
- Limited suitability for high-stress applications.
Environmental Considerations
Both steel casting and iron casting processes have significant environmental impacts. However, there are measures to mitigate these effects:
- Energy Consumption: Both processes are energy-intensive. Implementing energy-efficient technologies and using renewable energy sources can reduce their environmental footprint.
- Waste Management: Proper disposal and recycling of foundry waste, such as spent sand and slag, are crucial to minimize environmental pollution.
- Recycling: Utilizing recycled scrap materials in both steel casting and iron casting processes can reduce the need for virgin raw materials and decrease energy consumption.
Environmental Impact Comparison Table
Aspect | Steel Casting | Iron Casting |
---|---|---|
Energy Consumption | High | High |
Waste Generation | Significant | Significant |
Recycling Potential | High | High |
Emissions | Greenhouse gases and particulates | Greenhouse gases and particulates |
Conclusion
The comparative analysis of steel casting and iron casting reveals that each process has distinct advantages and is suited to specific applications based on their material and mechanical properties. Steel casting is preferred for high-stress, dynamic, and high-impact applications due to its superior strength, ductility, and impact resistance. In contrast, iron casting excels in castability, wear resistance, and cost-effectiveness, making it suitable for applications requiring complex shapes and high compressive strength.