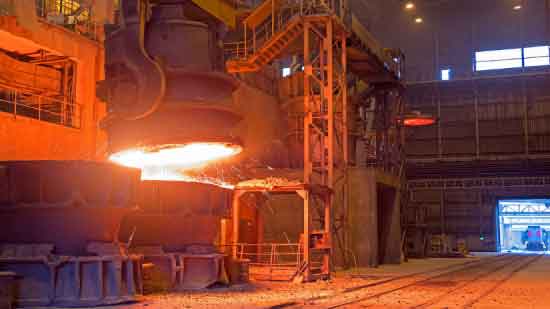
Steel sand casting is a manufacturing process that allows for the production of precise and high-quality metal components. With proper techniques and attention to detail, steel sand casting can achieve tight tolerances, excellent surface finish, and dimensional accuracy. Here are some key factors that contribute to precision and quality in steel sand casting:
- Pattern Design and Tooling: The pattern used in steel sand casting serves as the template for creating the mold cavity. Precision in pattern design and construction is crucial to ensure accurate dimensions and geometries of the final casting. High-quality tooling, including pattern materials and machining methods, helps maintain the integrity and consistency of the pattern.
- Mold Making and Preparation: The quality of the mold directly impacts the precision and quality of the castings. Careful attention is given to mold preparation, including proper sand mixing, compaction, and mold assembly. Accurate gating and riser systems are designed to ensure proper metal flow and solidification, minimizing the risk of defects.
- Molten Metal Quality Control: The quality of the molten metal used in steel sand casting plays a significant role in achieving precision and quality. Strict control of alloy composition, temperature, and cleanliness of the molten metal helps ensure consistent and reliable castings.
- Casting Parameters and Process Control: Controlling the key parameters of the casting process, such as pouring temperature, pouring rate, and solidification time, is essential to achieve precise and high-quality castings. Monitoring and maintaining these parameters within the specified ranges minimize the risk of defects and ensure dimensional accuracy.
- Solidification and Cooling Control: Proper control of solidification and cooling rates is crucial for achieving precise dimensions and minimizing casting defects. By implementing proper gating and riser design, the cooling rate can be controlled, ensuring uniform solidification and minimizing the risk of shrinkage or distortion.
- Post-Casting Processes: Post-casting processes such as heat treatment, machining, and surface finishing contribute to the precision and quality of the final components. Heat treatment processes help enhance the mechanical properties and dimensional stability of the castings. Precision machining operations ensure accurate dimensions, while surface finishing operations provide the desired surface texture and appearance.
- Quality Control and Inspection: Rigorous quality control measures are implemented throughout the steel sand casting process to ensure precision and quality. Non-destructive testing techniques, such as visual inspection, dimensional inspection, ultrasonic testing, and X-ray examination, are employed to detect any defects or deviations from specifications. Mechanical testing ensures the castings meet the required strength and performance criteria.
By implementing proper process controls, quality assurance measures, and continuous improvement practices, steel sand casting can achieve precise dimensions, tight tolerances, and high-quality components. It is important to work closely with experienced foundries and implement stringent quality control processes to ensure the desired level of precision and quality in steel sand castings.