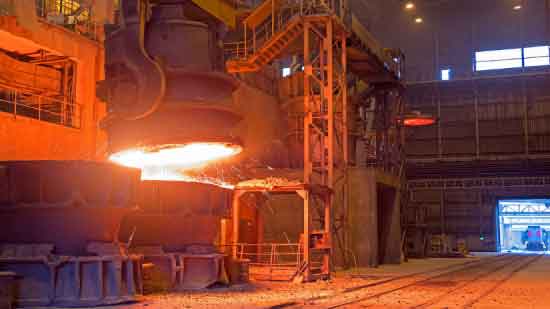
Steel sand casting offers cost-effective solutions for large-scale production due to its efficiency, scalability, and material optimization. Here are some key reasons why steel sand casting is a cost-effective choice for large-scale production:
- Economies of Scale: Steel sand casting is well-suited for large-scale production volumes. The process allows for the production of multiple castings simultaneously, maximizing the use of molds and optimizing production efficiency. As the production volume increases, the fixed costs associated with tooling, setup, and pattern making are spread across a larger number of castings, reducing the cost per unit.
- Material Optimization: Steel sand casting allows for efficient material utilization. The sand molds conform closely to the desired shape, minimizing material waste. Additionally, steel scrap and recycled material can be incorporated into the casting process, reducing the need for virgin steel and lowering material costs. The ability to recycle excess material and reuse sand molds further enhances material optimization and cost savings.
- Tooling and Equipment Efficiency: Steel sand casting benefits from well-designed tooling and equipment that can handle large-scale production. The initial investment in tooling and equipment can be justified over time as the production volume increases. Optimized tooling design and equipment utilization contribute to higher production efficiency and reduced per-unit costs.
- Process Efficiency: Steel sand casting is a relatively fast process compared to other metal manufacturing techniques. The cycle times for casting are typically shorter, allowing for faster production rates and increased throughput. The ability to produce multiple castings simultaneously and the simplicity of the casting process contribute to overall process efficiency and cost-effectiveness.
- Reduced Secondary Operations: Steel sand casting can often produce near-net-shape components, minimizing the need for extensive secondary operations. The dimensional accuracy and surface finish achieved through the casting process reduce the amount of machining or post-casting operations required. This leads to cost savings in terms of labor, time, and equipment associated with secondary operations.
- Flexibility and Adaptability: Steel sand casting offers flexibility in accommodating design changes and modifications during large-scale production. Adjustments to the mold design or gating system can be easily made to incorporate design improvements or address production challenges. This flexibility allows for continuous optimization of the casting process, resulting in cost savings and improved quality.
- Cost-Efficient Material Properties: Steel offers a favorable cost-to-performance ratio for many applications. Its high strength, durability, and versatility make it suitable for a wide range of industrial applications. The cost-effectiveness of steel, combined with the efficient production capabilities of steel sand casting, makes it an attractive option for large-scale manufacturing.
By leveraging the advantages of steel sand casting, manufacturers can achieve cost-effective solutions for large-scale production. The ability to optimize material usage, scale up production, and streamline the process contributes to overall cost savings. It is important to work closely with experienced foundries and implement effective quality control measures to ensure consistent quality and cost-effectiveness in large-scale steel sand casting production.