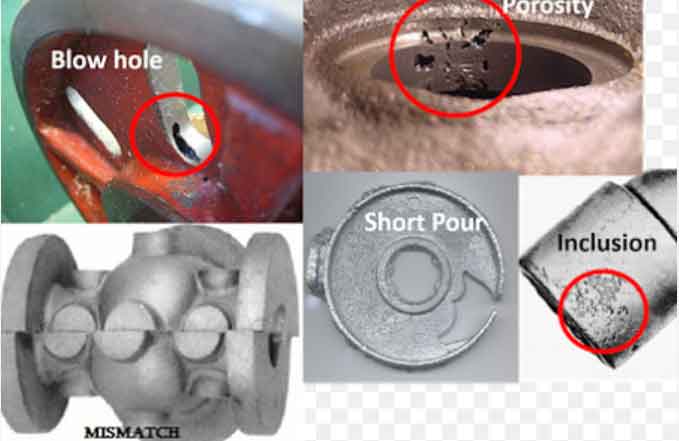
Managing casting defects is a critical aspect of ensuring the production of high-quality castings. Casting challenges can arise from various factors, including design flaws, process variables, and material considerations. This article provides strategies for effectively managing casting defects and overcoming common challenges, leading to improved casting quality and performance.
1.Design Optimization:
a) Design for Manufacturability:
Involve casting experts early in the design phase to optimize component geometry, wall thickness, fillet radii, and gating and riser placement to minimize potential defects.
b) Simulation and Analysis:
Utilize advanced casting simulation software to analyze the mold filling process, identify potential defects, and optimize gating and riser design for improved flow and reduced defects.
c) Prototyping and Testing:
Create prototypes to evaluate the design’s manufacturability and perform physical testing to validate the casting process and identify any design-related challenges or defects.
2.Material Selection and Preparation:
a) Material Compatibility:
Select casting materials that are suitable for the application, considering factors such as mechanical properties, fluidity, and solidification characteristics.
b) Material Quality Control:
Implement stringent material testing and inspection procedures to ensure the purity, consistency, and proper handling of raw materials, minimizing the risk of defects caused by material impurities.
c) Heat Treatment and Alloying:
Apply appropriate heat treatment processes and alloying techniques to enhance material properties and reduce the occurrence of defects like porosity and inclusions.
3.Process Control and Optimization:
a) Robust Process Parameters:
Establish and maintain optimal process parameters, including pouring temperature, pouring rate, mold temperature, solidification time, and cooling rates, to promote sound castings.
b) Effective Gating and Riser Design:
Optimize gating and riser systems to facilitate proper metal flow, reduce turbulence, and ensure effective feeding and riser performance to minimize defects such as shrinkage and misruns.
c) Process Monitoring and Control:
Utilize advanced monitoring technologies and techniques to continuously monitor process variables, detect deviations, and implement timely corrective actions, thereby minimizing defects.
4.Quality Assurance and Inspection:
a) Comprehensive Inspection Procedures:
Implement thorough inspection protocols, including visual inspection, dimensional measurement, and non-destructive testing (NDT) methods like X-ray, ultrasonic, or magnetic particle inspection.
b) Statistical Process Control (SPC):
Apply SPC techniques to monitor process data and identify trends or deviations that could lead to defects, enabling proactive interventions to maintain casting quality.
c) Supplier Quality Management:
Establish effective supplier quality management systems to ensure the consistent supply of high-quality raw materials, reducing the risk of defects caused by material variability.
6.Continuous Improvement and Training:
a) Defect Analysis and Corrective Actions:
Analyze casting defects, identify root causes, and implement appropriate corrective actions to prevent their recurrence. Document lessons learned to facilitate continuous improvement.
b) Training and Skill Development:
Provide comprehensive training programs to enhance the knowledge and skills of casting personnel, including design engineers, foundry operators, and quality control staff, ensuring a well-rounded understanding of defect prevention and resolution.
c) Cross-Functional Collaboration:
Foster collaboration among design, engineering, foundry, and quality teams to share knowledge, insights, and experiences, driving continuous improvement efforts and effectively addressing casting challenges.
Effectively managing casting defects requires a holistic approach that encompasses design optimization, material selection and preparation, process control and optimization, quality assurance, and continuous improvement initiatives. By implementing these strategies and fostering collaboration among various stakeholders, manufacturers can overcome casting challenges and achieve improved casting quality, reduced defects, and enhanced overall performance. Embracing a proactive mindset, investing in advanced technologies, and prioritizing training and continuous improvement are key to successfully managing casting defects.