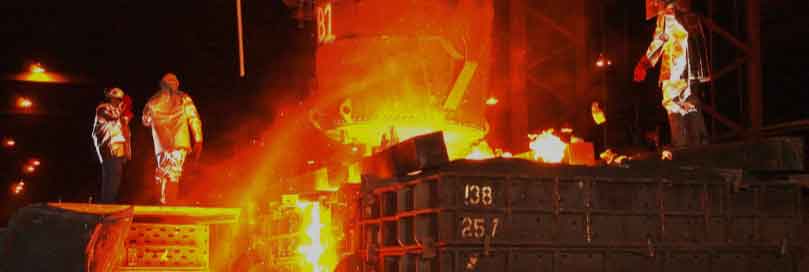
Sand casting is a traditional and time-honored casting method that continues to preserve its place in the modern industrial world. It represents a link between the past and the present, combining age-old techniques with modern advancements. Sand casting retains its relevance by offering unique benefits, preserving craftsmanship, and enabling the production of large and complex metal components. In this response, we will explore how sand casting preserves tradition in the modern industrial world.
- Historical Significance and Craftsmanship: Sand casting has a rich history that spans centuries, making it a significant part of our cultural and industrial heritage. The process embodies the traditional craftsmanship and artistry that have been passed down through generations. Sand casting techniques have been refined and perfected over time, and the knowledge and skills associated with the process have been preserved and handed down by artisans. By continuing to practice sand casting, we honor the legacy of those who came before us and preserve the traditional craftsmanship that is deeply rooted in our history.
- Versatility and Scalability: Sand casting is known for its versatility and ability to produce large and complex metal components. It can accommodate a wide range of metals and alloys, making it suitable for various applications across industries. Whether it’s casting engine blocks for automotive manufacturing, creating intricate sculptures, or producing structural components for industrial machinery, sand casting offers a scalable solution. Its versatility and scalability allow for the production of both unique, one-of-a-kind pieces and large quantities of components.
- Cost-Effectiveness: Sand casting remains a cost-effective casting method, particularly for large-scale production or components with irregular shapes. The materials used in sand casting, such as silica sand, are relatively inexpensive compared to specialized refractory materials used in other casting methods. Additionally, the tooling costs for sand casting can be lower compared to other casting processes, allowing for cost savings, especially for shorter production runs. Sand casting’s cost-effectiveness makes it an attractive choice for manufacturers seeking to balance quality and affordability.
- Adaptability to Complex Geometries: Sand casting excels in handling complex geometries and large-sized components. The mold cavity is created by compacting sand around a pattern, allowing for the formation of intricate shapes and internal cavities. The mold can be constructed in multiple parts to accommodate undercuts and complex features, enabling the production of components with intricate designs and details. This adaptability to complex geometries is a unique strength of sand casting and sets it apart from other casting processes.
- Sustainability and Environmental Considerations: Sand casting aligns with the growing emphasis on sustainability and environmental consciousness. The primary molding material, sand, is reusable and recyclable, contributing to reduced waste and resource conservation. Additionally, the sand casting process typically utilizes low energy consumption compared to other casting techniques. The ability to recycle sand and the environmentally friendly nature of sand casting make it an environmentally conscious choice in metal production.
- Cultural and Artistic Significance: Sand casting has cultural and artistic significance beyond its industrial applications. It is often embraced by artists and sculptors who appreciate the hands-on nature of the process and the ability to translate their artistic vision into tangible metal artworks. Sand casting allows for artistic expression, capturing the intricacy and uniqueness of sculptural forms. By preserving sand casting techniques, we ensure the continuation of artistic traditions and the creation of metal sculptures that embody creativity and cultural significance.
Sand casting preserves tradition in the modern industrial world by combining historical significance, craftsmanship, versatility, cost-effectiveness, adaptability to complex geometries, sustainability, and cultural/artistic value. It bridges the gap between traditional practices and modern advancements, ensuring the continuation of a time-honored casting method that holds its own unique place in today’s manufacturing landscape. Sand casting allows us to honor the past, celebrate craftsmanship, and produce large and complex metal components that contribute to various industries.