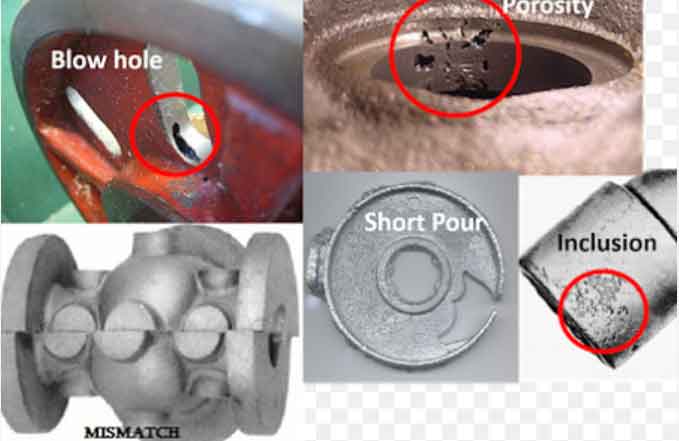
Ensuring high-quality metal castings requires proactive measures to prevent defects. By implementing effective strategies, manufacturers can minimize casting defects and enhance overall casting quality. This article outlines key strategies for preventing defects in metal castings, including process optimization, material control, mold design, and quality assurance.
1.Process Optimization:
a) Pouring Parameters:
Optimize pouring temperature, pouring rate, and metal flow to ensure proper filling of the mold and minimize defects like misruns, cold shuts, or inadequate filling.
b) Solidification Control:
Control cooling rates, use chills or risers to promote uniform solidification, and avoid shrinkage defects and residual stresses.
c) Gating System Design:
Design an efficient gating system to facilitate smooth metal flow, minimize turbulence, and prevent defects like porosity or incomplete filling.
d) Melt Treatment:
Implement proper melt treatment processes such as degassing, fluxing, or refining to remove impurities and minimize defects caused by inclusions or gas porosity.
2.Material Control:
a) Alloy Selection:
Choose suitable alloys based on their properties and compatibility with the casting process. Consider factors such as fluidity, solidification characteristics, and resistance to defects.
b) Metal Cleanliness:
Ensure the cleanliness of the metal through proper handling, storage, and melt treatment. Minimize contamination from oxides, slag, or other impurities that can cause defects.
3.Mold and Core Design:
a) Mold Material and Coatings:
Select appropriate mold materials and coatings to resist erosion, promote good surface finish, and prevent defects like metal penetration or mold degradation.
b) Mold Venting:
Optimize mold venting to allow for the escape of gases and prevent defects like porosity or blowholes.
c) Core Design and Assembly:
Ensure accurate core design, proper assembly, and alignment to prevent defects related to misruns or dimensional variations.
4.Quality Assurance:
a) Inspection and Testing:
Implement thorough inspection and testing techniques, including visual inspection, non-destructive testing (NDT), and dimensional measurement, to detect defects early and ensure casting quality.
b) Process Monitoring:
Continuously monitor process parameters, such as temperature, pressure, and time, to detect deviations and prevent defects.
c) Training and Skills Development:
Provide comprehensive training programs to casting personnel to enhance their knowledge of defect recognition, process optimization, and quality control techniques.
5.Continuous Improvement:
a) Root Cause Analysis:
Perform detailed root cause analysis of casting defects to identify the underlying causes and implement corrective actions.
b) Data Analysis:
Analyze historical defect data, process parameters, and quality metrics to identify trends, patterns, and areas for improvement.
c) Collaboration and Feedback:
Foster collaboration between casting personnel, engineers, and quality control teams to share knowledge and feedback for continuous improvement.
Preventing defects in metal castings requires a systematic and proactive approach. By optimizing the casting process, controlling materials, designing molds and cores effectively, implementing robust quality assurance practices, and continuously striving for improvement, manufacturers can enhance casting quality, reduce defects, and achieve higher customer satisfaction. Emphasizing process optimization, material control, and quality assurance throughout the casting production cycle will contribute to the production of defect-free castings and ensure consistent and reliable performance in various applications.