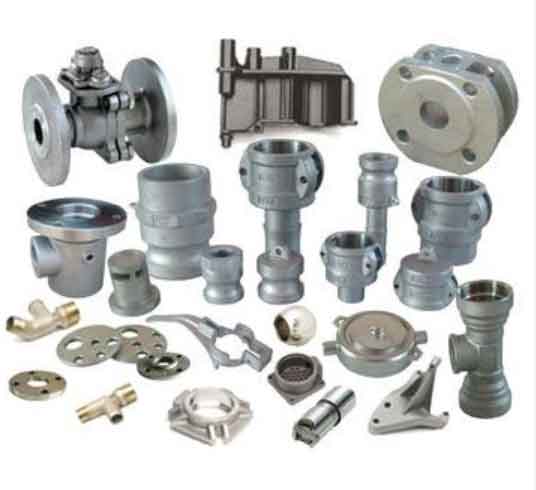
Sand casting offers several advantages that make it a popular choice in manufacturing. Here are some key advantages of sand casting:
- Versatility: Sand casting is a highly versatile process that can accommodate a wide range of part sizes, shapes, and complexities. It allows for the production of both small and large castings, including those with intricate designs and internal cavities.
- Cost-Effectiveness: Sand casting is a cost-effective method of producing metal parts, especially for low to medium production volumes. The tooling and equipment costs are relatively low compared to other casting methods, making it a viable option for manufacturers with budget constraints.
- Material Selection: Sand casting supports the use of a wide variety of metals and alloys, including steel, iron, aluminum, bronze, and brass. This allows manufacturers to choose the most suitable material for the desired properties and performance of the part.
- Design Flexibility: Sand casting enables the production of complex parts with intricate geometries, including features such as undercuts, internal cavities, and thin walls. It offers design freedom, allowing for the creation of custom parts tailored to specific requirements.
- Tooling and Lead Time: The lead time for sand casting is relatively shorter compared to other casting processes. The tooling and pattern-making process can be completed relatively quickly, reducing the time required for initial production.
- Repair and Modification: Sand castings can be easily repaired or modified if necessary. Any defects or imperfections can be addressed by reworking the mold or pattern, eliminating the need for scrapping the entire casting.
The applications of sand casting are extensive across various industries. Some common applications include:
- Automotive Industry: Sand casting is widely used in the automotive industry for the production of engine components, transmission parts, brake system components, and chassis components.
- Aerospace Industry: Sand casting is utilized in the aerospace industry for manufacturing engine components, turbine blades, structural components, and other critical parts.
- Construction Industry: Sand casting is employed in the construction industry to produce structural components, such as beams, columns, and brackets.
- Heavy Machinery and Equipment: Sand casting is used to manufacture parts for heavy machinery and equipment, including agricultural machinery, mining equipment, and industrial machinery.
- Pumps and Valves: Sand casting is commonly used to produce pump and valve components, including casings, impellers, housings, and flanges.
- Art and Decorative Objects: Sand casting is even utilized in the production of artistic and decorative objects, such as sculptures, ornamental fixtures, and custom-designed metal artworks.
Sand casting’s ability to produce large, complex, and cost-effective parts makes it a preferred choice in many industries. However, it is important to consider factors such as dimensional accuracy, surface finish, and mechanical properties to ensure the suitability of sand casting for a specific application.