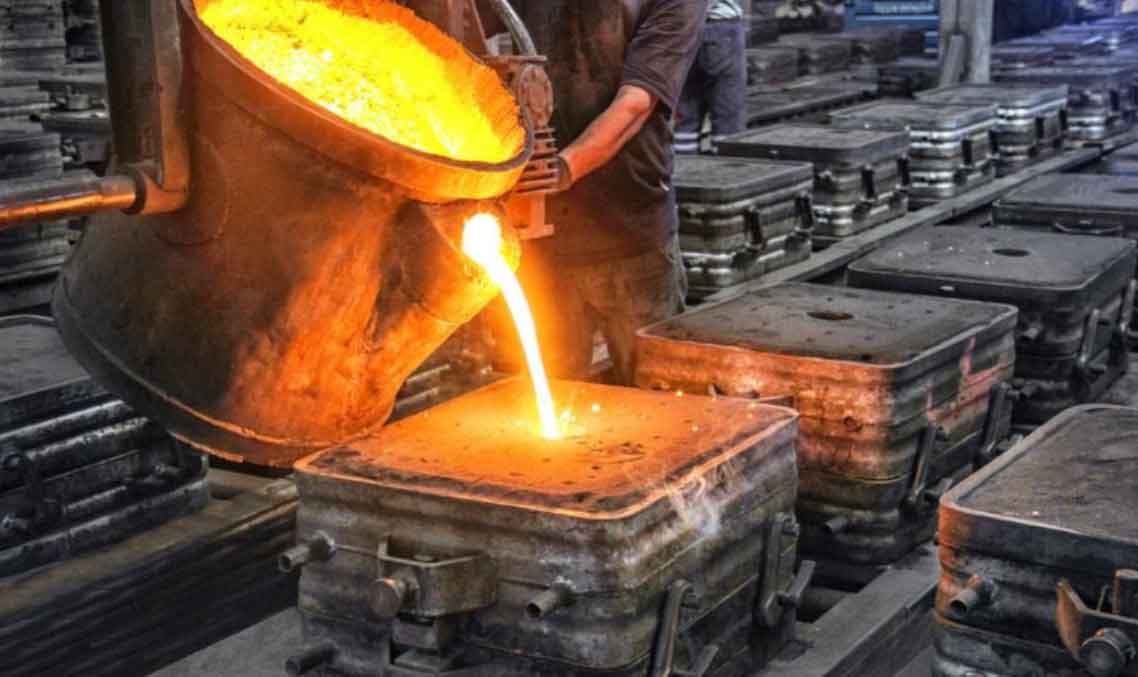
Implementing lean principles in sand casting manufacturing can significantly improve production efficiency, reduce waste, and enhance overall process effectiveness. Lean principles focus on maximizing value for the customer while minimizing resources and eliminating non-value-added activities. Here’s how sand casting manufacturers can streamline their production using lean principles:
1. Identify Value from the Customer’s Perspective:
- Understand the specific value that customers seek from the castings. Manufacturers should communicate with customers to determine their needs and requirements accurately.
2. Map the Value Stream:
- Create a value stream map that visualizes the entire casting process from raw material to delivery. Identify all steps, activities, and materials involved in producing castings.
3. Eliminate Waste:
- Identify and eliminate all forms of waste in the casting process, such as overproduction, excess inventory, unnecessary transportation, waiting times, and overprocessing.
4. Implement 5S Workplace Organization:
- Apply the 5S methodology (Sort, Set in Order, Shine, Standardize, Sustain) to organize the workplace and improve efficiency, safety, and cleanliness. Keep the casting area well-organized and free of unnecessary items.
5. Standardize Work Processes:
- Establish standardized work processes and procedures to ensure consistency and efficiency in casting operations. This helps reduce variations and ensures a stable production environment.
6. Use Pull Systems:
- Implement pull systems, such as a kanban system, to control production based on customer demand. This minimizes excess inventory and ensures castings are produced only when needed.
7. Reduce Changeover Times:
- Minimize changeover times between different casting jobs to improve productivity and responsiveness to customer demands.
8. Continuous Flow and One-Piece Flow:
- Aim to achieve a continuous flow of castings through the production process, whenever possible, to reduce waiting times and improve efficiency. One-piece flow can help identify bottlenecks and balance workloads.
9. Empower Employees:
- Involve employees in the process improvement efforts and encourage them to identify and solve problems proactively. Empowered employees are more likely to contribute to lean initiatives.
10. Continuous Improvement:
- Embrace a culture of continuous improvement, where all employees are encouraged to seek opportunities for streamlining processes and eliminating waste. Regularly review the casting process and implement improvements.
11. Value Stream Mapping for Suppliers:
- Extend value stream mapping beyond the manufacturing facility to include suppliers. Collaborate with suppliers to optimize material flow and reduce lead times.
12. Measure and Monitor Performance:
- Use key performance indicators (KPIs) to measure process performance and monitor the impact of lean initiatives. Regularly analyze data to identify areas for further improvement.
By implementing lean principles, sand casting manufacturers can achieve more efficient production processes, reduce lead times, eliminate waste, and deliver higher value to their customers. Lean manufacturing practices help manufacturers stay competitive, responsive to market demands, and adaptable to changing customer requirements.