Bridge bearing is the casting name of a kind of products. It is an important structural component connecting the upper structure and the lower structure of the bridge. It not only needs to bear a large load, but also has the function of reducing and isolating earthquake, so as to protect the bridge beam from being damaged by external forces. The bearing of iron main bridge beam is generally composed of steel bearing, wear-resistant plate, connecting components and embedded components. The research object of this project is the steel bearing component in the bridge bearing. The product type is a type I steel bearing steel casting, and its product structure is shown in the figure.
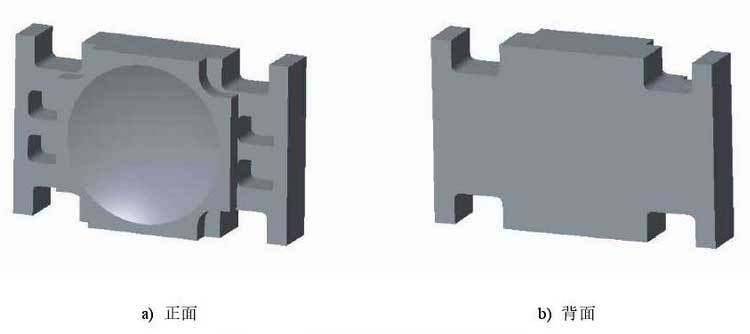
The overall dimension (length, width and height) of the cast steel bearing is 700mm × 445mm × 155mm and the weight is 262kg. It can be seen from Fig. that the wall thickness transition of the bearing is very uneven, the two sides of the long side are the plate reinforcement structure with square blind holes, and the thinnest part of the wall thickness is 30mm; in the middle is a cuboid structure with arc concave surface, and the maximum wall thickness is 155mm. The product is one of the more complicated steel castings of bridge bearing, and the internal quality requirements are very high, which must meet the class II standard of ultrasonic flaw detection.
The transfer casting process is sand casting, and the binder is sodium silicate. However, the surface of the casting is easy to stick sand, and the internal defects are easy to appear, and the process yield is low and the production cost is high. In this project, EPC process is used to solve the production difficulties of this kind of bridge bearing steel castings, improve product quality and process yield, and create economic benefits for enterprises.